Warehouse Management: Definition, Challenges, and Why It’s Crucial for Business
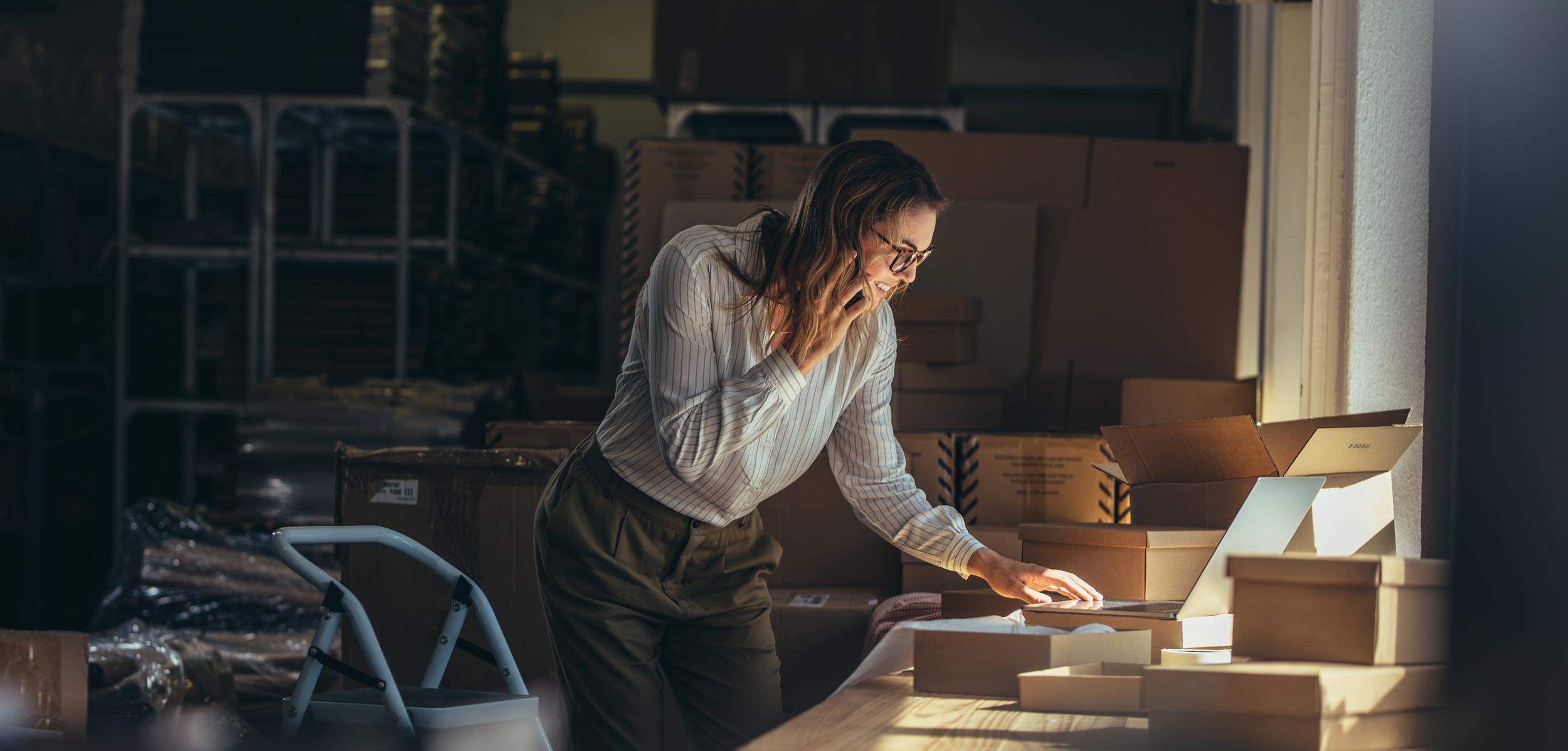
Whether you have enough inventory to fill multiple football stadiums or barely enough to fill a one-car garage, managing your products’ journey is essential for ecommerce and retail success. Customers expect to receive the products they order in the specifications they selected as quickly as possible.
It sounds simple enough, but how do you ensure that your inventory list is up to date and matches the stock on your shelves right this minute? How do you make sure refrigerated items are packaged for shipping just before your delivery driver arrives to load them so the products don’t spoil?
You’ll find answers to these questions and many more in this in-depth guide to warehouse management. If you want to brush up your warehouse terminology as well, check out our guide!
From product acquisition to final delivery, we’ve compiled top strategies and key insights, along with software and service-provider recommendations for product companies of all sizes.
Here’s what we’ll cover in this article:
- What is Warehouse Management?
- Why Warehouse Management is Crucial for Your Bottom Line
- The Importance of Last-Mile Delivery
- 7 Key Responsibilities of Warehouse Management
- Challenges of Warehouse Management
- How to Improve Warehouse Management
- 4 Top Warehouse Management Providers
- OptimoRoute: A Partner in Logistics and Beyond
What Is Warehouse Management?
Warehouse management is the process of receiving, storing, stocking, and protecting inventory while it waits to be shipped to its final destination (the customer). Warehouse management is a crucial function for businesses that sell physical goods. It encompasses seven different stages in a supply chain and is the origin point for last-mile delivery. The efficiency of your warehouse and delivery teams determines how fast (or how slow) your customers get their orders.
Warehouse management can also refer to the team of employees who work in a warehouse and carry out the day-to-day functions of a supply-chain management process.
Why Warehouse Management Is Crucial for Your Bottom Line
The better your warehouse management process, the faster you will be able to get your products into the hands of your customers (and ensure that those customers keep coming back). Online shopping is booming. At OptimoRoute we recently published statistics collected from users across the restaurant and retail industries to have a better understanding of current consumer trends and help us all prepare for the future.
What the data shows is that as businesses enter economic headwinds due to reductions in demand, it’s becoming essential to leverage route optimization to efficiently deploy delivery labor and recover margins. For instance, it’s more important than ever to keep the number of orders per driver high and keep the number of miles down.
eMarketer predicts that direct-to-consumer (DTC) ecommerce will generate almost $18 billion in revenue this year (up more than 24% from last year). If you want to capitalize on this, you need top-notch warehouse management.
Teamwork between your warehouse and last-mile delivery teams is essential if you want to compete with ecommerce giants like Amazon. Warehouses tee up your last-mile delivery team to knock order delivery and customer experience out of the park.
The Importance of Last-Mile Delivery
The key to improving product deliveries and minimizing turnaround times is combining warehouse management with top-tier last-mile delivery. Last-mile delivery is the final stage in a forward logistics process and, most importantly, it’s the customer-facing part.
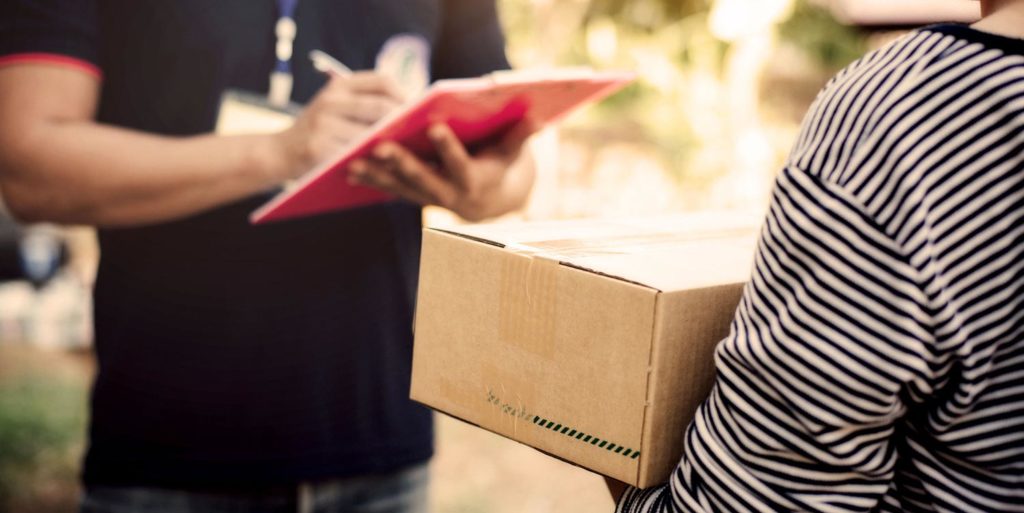
If your warehouse or distribution center is operating at peak efficiency, but your last-mile delivery is subpar, your customer may get their delivery late, resulting in a bad experience. The results are the same if you have great last-mile delivery but your drivers have nothing to ship because your warehouse is backed up.
Warehouse management and last-mile delivery are two sides of the same coin, and they both need to be optimized for your business to succeed. If they aren’t, you risk losing customers permanently. Read more on last mile delivery and how OptimoRoute helps businesses tackle the problem.
Use OptimoRoute to nail last-mile delivery
It’s safe to assume that nobody is going to care more about your products and your customers than you, which is It’s safe to assume that nobody is going to care more about your products and your customers than you, which is why the best retail distribution strategy is often to keep last-mile delivery in-house. OptimoRoute has helped retail and ecommerce businesses across the globe drive revenue by improving key performance indicators (KPIs) such as delivery capacity and on-time deliveries.
OptimoRoute can be seamlessly connected to other third-party software, such as warehouse management software. You can use API integration to make sure that your whole team is on the same page and that products move quickly from packing to loading and final delivery.
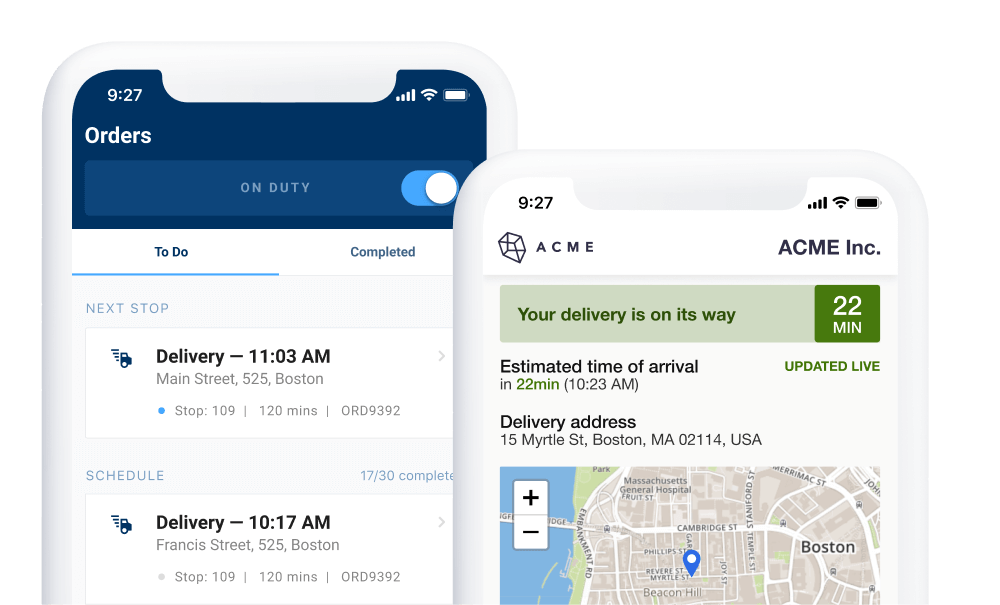
Reduce your operational costs by 30%
Increase delivery capacity by 43%
Plan 7x faster
Fleet managers can spend more time on strategic planning when they let OptimoRoute calculate optimized delivery plans for them. All they have to do is upload orders, input any specific constraints, and click “Plan routes.” They can use the “Return to Depot” feature to easily plan multiple delivery runs in a single shift and synchronize with warehouses that use wave-picking schedules (which we’ll explain in just a minute).
OptimoRoute also enables you to send customers real-time order updates via email or SMS notifications, which not only makes for a better customer experience but also minimizes calls from customers asking where their packages are. Customer notifications are fully customizable and include a link to live tracking that shows exactly when orders will arrive.
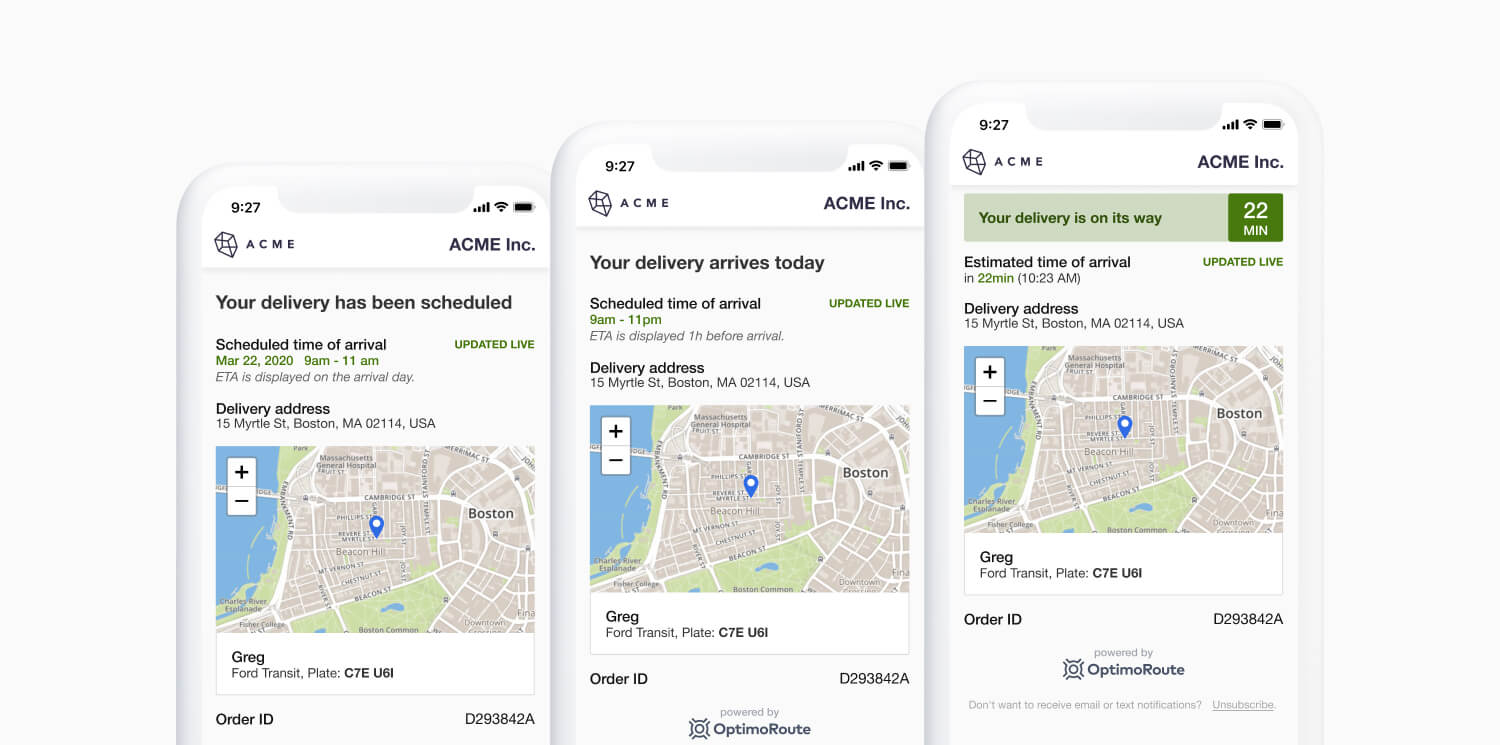
When you do need to use a shipping service or courier, this article provides some helpful tips and ideas for cutting down on shipping costs. We’ve also shared a guide for package tracking through the most popular global couriers that contains links, so you can track a package right now.
The 7 Key Responsibilities of Warehouse Management
Warehouse management oversees seven major fulfillment processes in logistics supply chain operations:
1. Receiving + inspection
The first thing warehouse management teams do is inspect incoming products or raw materials before they’re put away. Warehouse employees receive pallets of inventory and check inbound products (sent from a vendor or supplier) to make sure that they match the purchase order and that nothing was damaged or lost along the way. If they find any discrepancies, a new purchase order should be placed.
Sometimes, warehouses will receive a shipment that contains products that are the wrong color or size or are made of the wrong material. Occasional mistakes usually aren’t a big deal. However, managers need to identify if certain suppliers or vendors continually deliver damaged goods or often miss delivery deadlines. Repetitive issues must be brought up to brand leaders so they can determine whether a new supplier needs to be found.
2. Storage
Next, warehouse workers transport the inspected products to a designated location inside the warehouse, where they will be stored safely until a customer orders them. Great consideration should be given to precisely where and how items are stored. Products need to be secure. Heavy products shouldn’t be stacked on top of lighter ones, sensitive items may need to be placed in temperature-controlled environments, and all products need to be handled with care.
The bigger and more complex a warehouse is, the greater the impact that warehouse layout and storage allocation has on order processing time. Stockists need to store products that are often bought together in proximity to one another, so pickers don’t have to waste time traveling a long distance to gather those products over and over. It’s also a good idea to store popular products in locations that are easiest to access (lower shelves, closer to the front). Items that expire should be stored in priority order, so those expiring soonest are closest to the front (and get shipped out first).
3. Picking
When a customer places a new order, it’s a picker’s job to retrieve that order from the shelf and bring it to a packing location. Good pickers work quickly and have a high accuracy rate (they pull the right item, size, color, etc., almost all of the time). It’s easier for pickers to do their jobs well if your warehouse or distribution center follows best practices and is smartly laid-out, as explained in step 2.
These are the most common picking processes:
- Single order picking is the most basic picking strategy and is commonly used by small warehouses or storage facilities with low order volume. In this method, a picker gathers items one order at a time and brings all of those items for a single order to a packer before beginning to pick items for the next order.
- Wave picking is similar to single-order picking, with one difference: picking is scheduled at specific times of day and in short intervals. This strategy can help avoid congestion on a warehouse floor. It can also be used to match packing times with truck-loading times.
- Batch picking is a process in which multiple customer orders are grouped (or batched) to be picked up from their storage locations at the same time. Similar orders are batched, and items are picked up by SKU rather than order. This reduces the number of trips a picker needs to make to get popular items. If a batch of five different orders contains three bags of pastry flour, for example, all three bags can be picked up at once.
- Cluster picking is similar to batch picking. Pickers work on multiple orders at the same time, but grouping similar orders isn’t a priority. Picking isn’t necessarily done by SKU, either, though items that are close to one another from different orders may be picked close together to cut down on travel time across a warehouse.
- Zone picking is typically reserved for large warehouses or those with clearly divided sections, such as refrigerated and unrefrigerated zones. In this method, pickers are assigned a zone. This method can be combined with wave, batch, or cluster picking, and orders can be passed from one zone to the next before being delivered to packing.
Picking is the first step in the logistics process after a customer places an order, which means that the turnaround clock is counting down. From this step forward, delays and inefficiencies directly affect delivery time.
4. Packaging
Packers take items from pickers, confirm that they were picked accurately, and do a final check to make sure items are in good condition (and not expired). They then pack the items for safe shipping and update the warehouse’s inventory. Packers must take care to ensure that fragile items don’t get injured or broken in transport. In some cases, specific packaging will need to be used to meet packaging restrictions for a particular courier. Packers typically print shipping labels and may help load courier vehicles as well.
5. Coordination with last-mile delivery
Last-mile delivery is the transportation of goods from the warehouse to the customer. This can be handled in one of two ways:
- For long-distance and international shipping, warehouses often have relationships with multiple couriers, such as USPS, UPS, and FedEx. Freight, air, and rail transportation may be used, depending on the size of items being shipped and the distance they need to travel. Warehouse management is responsible for getting orders into the hands of couriers safely and ensuring customers get the appropriate tracking information associated with that courier.
- For local orders and businesses with a smaller territory, self-delivery is a great option for last-mile delivery. You can seamlessly guide a team of couriers to deliver an exceptional customer experience yourself using delivery management software such as OptimoRoute. There are a lot of benefits to keeping this stage of the product cycle in-house, which we’ll dive into later in this article.
Regardless of which option you choose, it is vital for warehouse management and last-mile delivery to work in unison. Packing needs to be timed to line up with a courier’s arrival, so delivery trucks can be loaded right away, and temperature-sensitive items aren’t sitting out too long.
6. Auditing
Auditing a warehouse is the process used for inventory control and QA to make sure small inventory errors or damaged products don’t turn into huge problems. Managers perform audits with different frequency, depending on the size of a warehouse and the intricacy of an operating floor. Often, auditing includes spot-checking inventory levels against digital manifests to make sure the numbers line up for accurate inventory forecasting. Managers may also check products with expiration dates to make sure nothing on the warehouse floor needs to be disposed of and restocked.
Managers auditing a large warehouse may also assess personnel, product layouts, scheduling strategies, and any other aspect of day-to-day operations. They use these checks to spot potential issues and fix them before they affect customers or result in injury on a warehouse floor.
7. Returns and restocking
Returns and restocking are a sometimes overlooked but extremely important facet of warehouse management. Providing a seamless reverse logistics process (returns management) for customers is an essential component in a product supply chain. No matter how good your team is and how great your product is, returns happen. Warehouse management teams handle receiving and restocking returned products as well as picking and packing new items for exchanges.
The Challenges of Warehouse Management
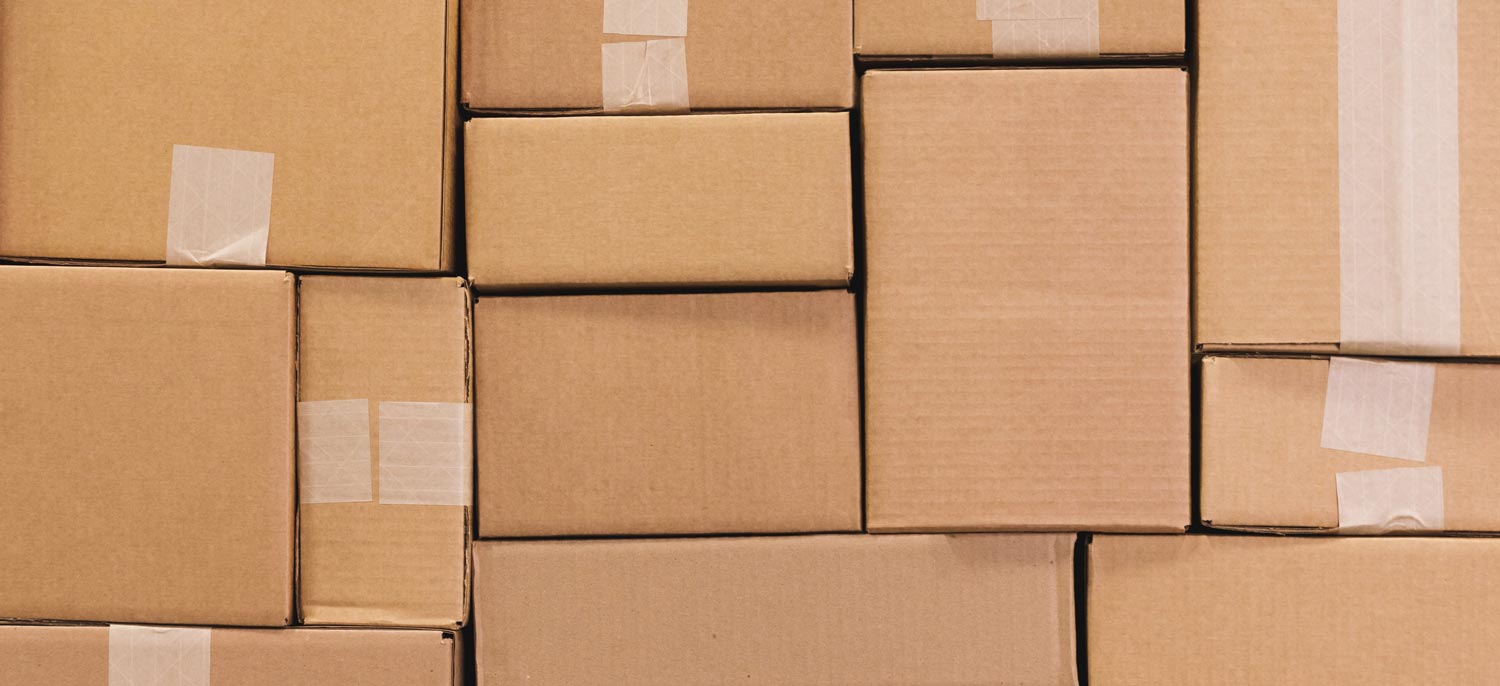
All of the common challenges of warehouse management can be addressed with software or outsourcing (or both). These challenges are:
- Material handling: Every member of your staff needs to handle packages with care. Goods should never be carelessly thrown around or stacked in ways that could damage them.
- Space: Simply finding enough space to store products can be a monumental task, especially for small businesses. Once you secure warehouse space, organizing products for optimal efficiency and product security is another hurdle.
- Processing efficiency: Every single facet of warehouse management (and of last-mile delivery) needs to be organized and streamlined for maximum efficiency. This is nearly impossible if your business runs on paper records and manual planning.
- Customer experience: At the end of the day, the success of any business hinges on customer satisfaction and meeting customer demand. A great warehouse management strategy takes this into account and proactively keeps customers updated about the status of their order while working to get product delivered as quickly as possible.
How to Improve Warehouse Management
Fortunately, there are some simple strategies you can use to overcome these challenges.
Develop a great recruiting process
Hiring top-tier talent should be a priority for any warehouse management team. Employees who are constantly late or don’t handle your products appropriately can cost you a lot of money. A solid employer branding strategy, a targeted recruiting process, and great salaries will help you avoid pitfalls in your recruiting and hiring process. You can also work with a recruitment agency that specializes in warehouse management job placement to find great employees.
Outsource your warehouse management
Hiring a third-party logistics company (3PL) to manage products is the best solution for some businesses. No matter how big or small your company (or your inventory), there’s a 3PL that can meet your needs. Warehouse management providers specialize in keeping your products stocked and safe while delivering a great experience for your customers. Most 3PL’s have direct relationships with multiple couriers, such as UPS and FedEx. You can use these shippers and/or your own courier team to deliver products locally.
Use software
You can improve both your day-to-day operations and high-level capacity planning by implementing software solutions such as Warehouse Management Software (WMS) or Enterprise Resource Planning (ERP) software. Using SaaS tools is an easy way to make sure everyone is working off of the most up-to-date information and is able to access that information quickly.
Warehouse management software (WMS software) serves as a central command for warehouses and helps reduce human error. Warehouse managers can use it to oversee operations from anywhere — even on a tablet or a mobile device while on the go. Pickers can use WMS software to locate SKUs in seconds. Packers can use WMS software to let your whole team know when orders are headed out the door. Pair that with delivery management and route optimization software, such as OptimoRoute, and you’ve got a tech-driven system for total logistical success.
4 Top Warehouse Management Systems
Keep your product journey in-house, and streamline your fulfillment and logistics processes with WMS solutions tailored to your needs. Below, you’ll find a breakdown of 4 software, along with the types of businesses they best serve and an explanation of their distinguishing features and functionality. The best part? All of these warehouse management solutions can be paired with OptimoRoute for seamless end-to-end logistics management.
Fishbowl
Fishbowl inventory management software makes every facet of warehouse management easier (and then some). Fishbowl helps you quickly process incoming stock with barcode scanners and enables inventory tracking by expiration date or serial number. You can create work orders for repairs and save them for reuse in the future. Fishbowl can be easily integrated with popular ecommerce software and platforms, including QuickBooks, Shopify, and Amazon.
Sortly
Sortly is an intuitive inventory management system for businesses of all sizes, especially small businesses. Employees can use Sortly’s in-app scanner to process inventory by scanning product barcodes or QR codes with a cell phone, tablet, or handheld scanner, which helps with inventory accuracy and overall efficiency. Specific access permissions can be granted to individual employees, so your team can get things done without needing manager approval every step of the way.
Logiwa
Logiwa is cloud-based warehouse management software that uses automation help businesses streamline complex warehouse workflows. Save time picking and packing with wave, batch, and cluster picking optimization. Logiwa features multi-warehouse management capabilities, which makes it a great choice for larger companies and businesses looking to scale. Logiwa also offers seamless integration with marketplaces and ecommerce platforms, such as Amazon and Shopify.
Infoplus Commerce
Infoplus Commerce is used by small independent companies and large 3PL’s alike. Whether you’re looking for inventory management software with marketplace integrations or artificial-intelligence technology that can help you prioritize tasks, Infoplus Commerce has a solution. Infoplus Commerce also offers marketplace, shopping cart, and various other integrations.
4 Top Warehouse Management Providers
Prefer to outsource? Below, you’ll find a breakdown of four warehouse management providers you can hire to manage your inventory. You can still keep your last mile delivery in-house by using any of these providers in conjunction with OptimoRoute.
ShipBob
ShipBob is a full-service 3PL providing both forward and reverse logistics (returns processing), inventory management and order management. ShipBob is a tech-enabled management provider specifically tailored to ecommerce companies using the DTC model. Online stores and ecommerce platforms, such as Amazon, Walmart, and Shopify, can be seamlessly integrated with ShipBob’s tech-enabled system.
eFulfillment Service
eFulfillment Service also serves ecommerce businesses and offers seamless integration with popular selling platforms, such as eBay and Shopify. They are a family-owned business based in Traverse City, Michigan. eFufillment Service has no minimum for orders or storage space, making them a great option for small businesses and a flexible choice for companies looking to scale.
FLEXE
FLEXE provides on-demand warehousing, order fulfillment, and distribution for retail stores and ecommerce businesses. They serve enterprise companies as well as smaller businesses and have numerous warehouses spread out all over the United States. FLEXE has worked with major brands, including Ralph Lauren, Staples, and Ace Hardware.
Red Stag Fulfillment
Red Stag Fulfillment uses a proprietary cloud-based system (RSF OPS) to manage warehouse operations, storage, and fulfillment. They provide real-time monitoring for DTC and business-to-business (B2B) ecommerce companies that can check on order status and inventory from a computer or a mobile device.
A Partner in Logistics and Beyond
Whether you adopt warehouse management software to keep your entire product journey in-house or hire a 3PL, OptimoRoute can help you conquer the last mile. Our delivery management software can optimize routes for the lowest cost or for even distribution among drivers, or a combination of the two. OptimoRoute enables managers to easily input and save constraints that are unique to your business and provides analytics that managers can use to make informed strategy decisions for future planning.
We’re committed to delivering top-notch customer service to you so you can do the same for your customers. Have a question about our integrations or want to know more about how you can use delivery management software to manage your own team of couriers? Simply send us a message, or give us a call anytime. We’ll be happy to answer any questions and get you set up with a 30-day free trial.
Try OptimoRoute™ for Free
No installation or credit card required