Distribution Center Processes and Best Practices You Need to Know
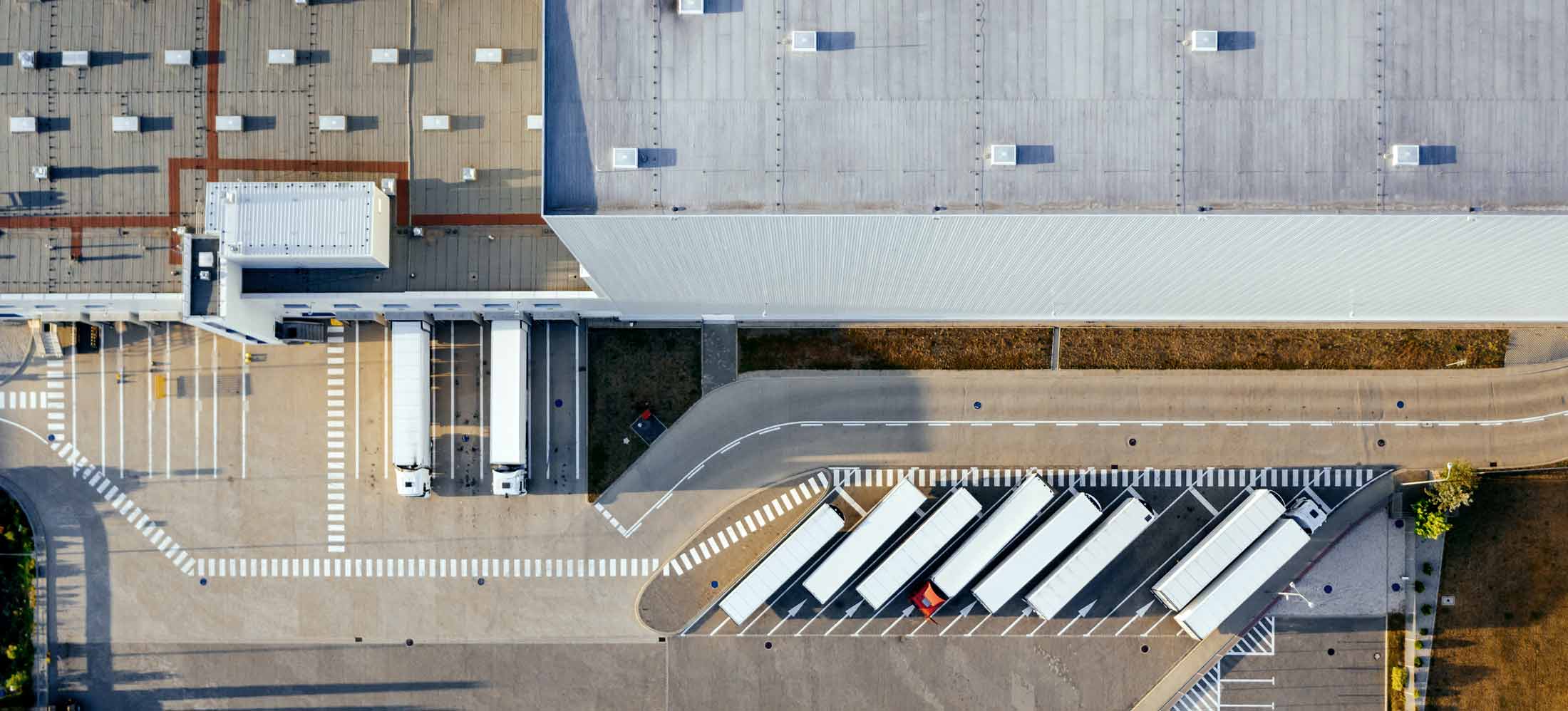
A well-run distribution center should be a bit like a symphony. Every department plays its part precisely, and when you put them together, they create a smooth and harmonious whole.
But even Beethoven didn’t conduct symphonies 40+ hours a week, and that’s the challenge of distribution centers—running a complex supply chain smoothly and precisely at all times. There are a few distribution center best practices—like better last mile delivery—you need to know if you expect your warehouse to run flawlessly. Read on to learn:
Essential Distribution Center Processes and Procedures
Before we dive into best practices, let’s review the essential processes distribution centers use to keep their supply chain logistics organized. These are the basic functions of a distribution center:
- Receiving – Receiving clerks inspect deliveries to make sure incoming products match the purchase order and nothing was damaged in transit. Reception teams may also be in charge of scanning incoming products for inventory tracking.
- Put-away – After intake, warehouse workers and forklift operators move products to a secure storage location where they will be safe until they’re purchased by a customer.
- Storage – Warehouse workers keep track of stock to make sure items are secure the entire time they are in the warehouse. Temperature-sensitive items, such as food, must be checked to make sure they don’t spoil and discarded if they expire. Products may also need to be relocated to ensure that the most popular or most frequently purchased items in the warehouse are the easiest to access.
- Picking – When a customer places an order, pickers physically pick up items from storage shelves and move them to a packing location.
- Packing – Customer orders are boxed and labeled for shipping or delivery by packers.
- Restocking (Returns) – When a customer returns a product, it is inspected by a warehouse worker to ensure it hasn’t expired and no parts are missing. Once it passes quality control, it gets restocked.
- Auditing – Warehouse audits are used to gauge the overall efficiency and effectiveness of distribution center processes. Auditing can also help management teams understand how well their team is performing.
Many distribution centers have separate teams that handle each of these inventory management processes. Communication across all of these teams is essential for success. For example, if your storage team rearranges stock, they need to let pickers and put-away workers know. Otherwise, you’ll have workers searching aimlessly for products and slowing down your supply chain.
Don’t forget last mile delivery
Supply chain management within your distribution or fulfillment center is only part of the equation. The other part is coordinating with last mile delivery. The importance of this partnership sometimes gets overlooked, but it’s vital for your success because it ensures quick turnaround times for customers.
You could have the most efficient pickers and packers in the world and still wind up with delivery delays if you aren’t communicating with your delivery team. Worse yet, products could spoil. Say you receive an order for two gallons of milk. Your pickers retrieve the milk and move it to packing. Then, it winds up sitting on a balmy loading dock for four hours before it’s loaded into a refrigerated loading truck because you weren’t sure when the truck was going to arrive. Your customer receives milk that has spoiled, and you’re on the hook to reimburse them.
Whether you’re working with couriers, shippers, or in-house last mile delivery teams, communication is key. Warehouse managers or dispatchers need to know precisely when delivery trucks will arrive, so they can schedule picking and packing at the right time.
Pro Tip: The easiest way to coordinate picking, packing, and last mile delivery is with route optimization software, such as OptimoRoute, that provides live tracking.
7 Distribution Center Best Practices
To turn your distribution center into a well-oiled machine, you need to optimize your processes for efficiency and profitability. Use these best practices to reduce wasted spend, move products through your supply chain faster, and ensure a better experience for your customers.
1. Use route optimization software to sync up with last mile delivery
We discussed the importance of coordinating with last mile delivery. But how do you achieve total supply chain synchronization? One highly effective tool is route optimization software with live tracking.
OptimoRoute enables warehouse dispatchers to see where delivery drivers are in real-time, so they can schedule the picking and packing to occur just before a truck arrives—and minimize the amount of time products are sitting on a loading dock.
Route optimization software also reduces wasted spend and improves customer experience by ensuring every delivery driver is taking the most efficient route possible. OptimoRoute makes it easy for dispatchers to schedule multiple truckload pick-ups for individual drivers with the “Return to Depot” feature.
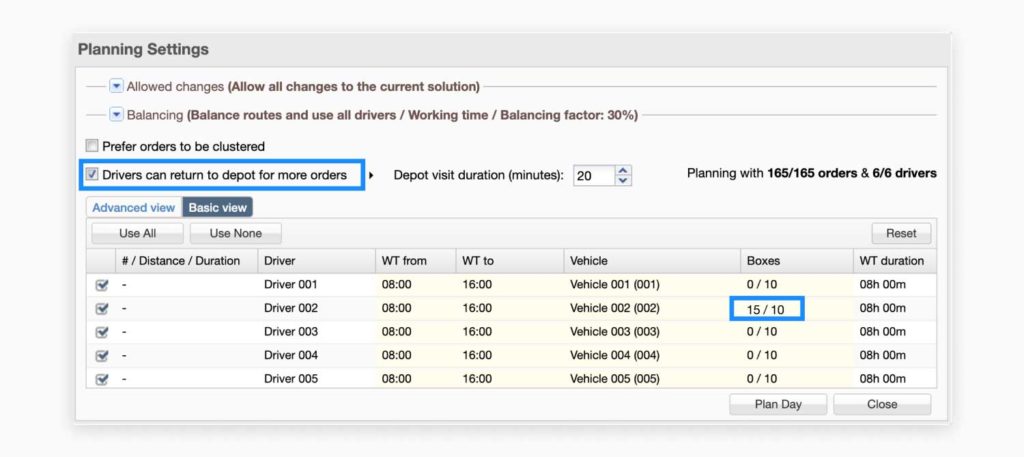
Plus, when you use OptimoRoute, Realtime Order Tracking is available for customers, too. Reduce delivery exceptions by providing your customers with a live view of their delivery driver. They’ll know exactly when their package is going to hit their doorstep, which means less redelivery attempts and fewer incoming customer service calls from customers wondering when their order will arrive.
2. Optimize your warehouse with a warehouse management system
When you’re managing what feels like a million moving pieces across dozens or hundreds of employees, you need advanced tools. You need a warehouse management system (WMS)—because managing a supply chain without one is like trying to call a radio station hotline with a rotary phone.
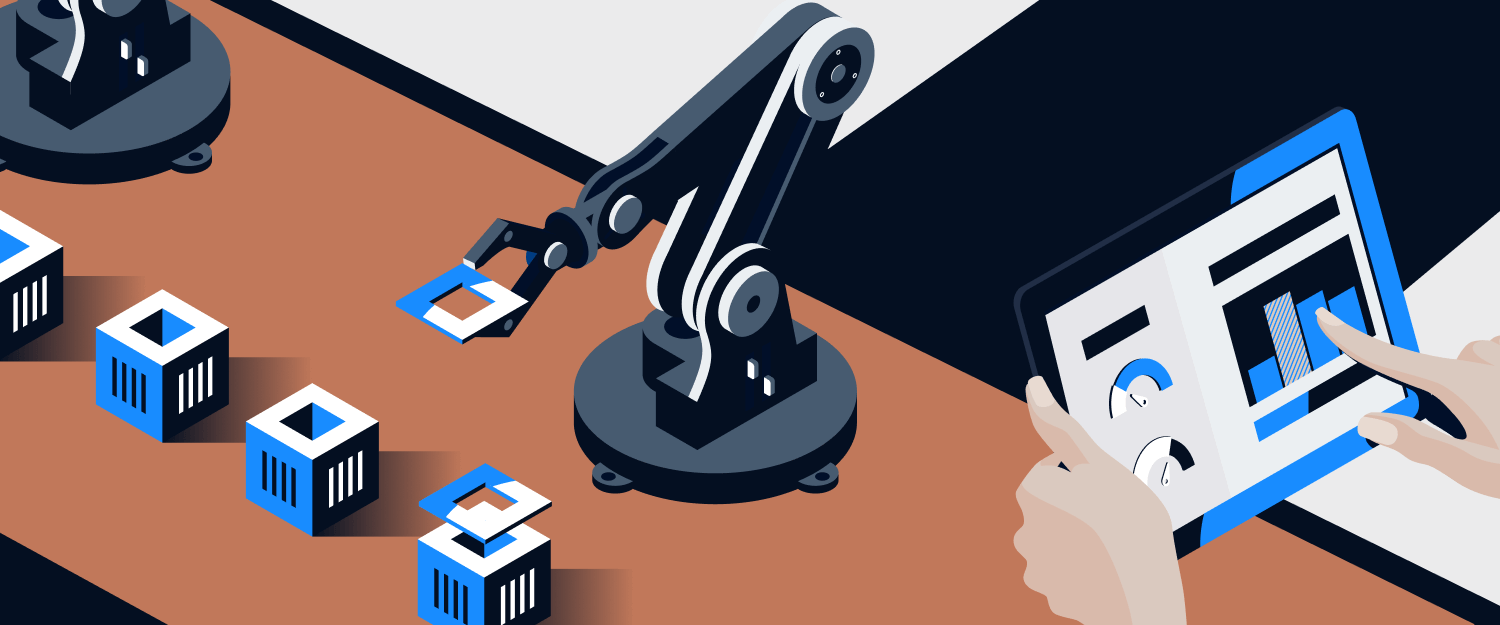
A WMS is software that acts as a central command for warehouses and distribution centers. It helps your entire team manage physical inventory, stay on top of product expiration dates and replenishment, identify specific product locations, and much more. With a WMS, you can scan the barcodes of incoming supplies during the receiving process, and your pickers can see those items seconds later in the updated inventory list. It reduces human error, improves picking accuracy, and provides real-time visibility within your facility, no matter how large or spread out it might be.
Pro Tip: Integrate your WMS with your route optimization software, and you’ll be able to easily track products from receiving to final delivery. OptimoRoute Web Service API integration is easy to use and works with third-party software, including warehouse management systems such as Sortly and Fishbowl.
3. Find the best picking process
Each picking process offers unique advantages. Don’t be afraid to test out different methods to determine which one works best for your team and facility layout.
Single order picking is effective for smaller, low-volume warehouses, but it doesn’t typically work as well for large warehouses handling a lot of outgoing orders each day.
Picking waves help distribution centers of all sizes reduce traffic on busy warehouse floors and synchronize packing times with the arrival of the delivery trucks.
Batch and cluster picking can each cut down on picking time if you have a lot of orders comprised of multiple SKUs.
Zone picking is a great option if you operate a large warehouse with multiple storage areas. Using this picking method, pickers retrieve products from smaller zones, and then orders are combined before packing rather than having one picker run all over an expansive warehouse to assemble an order. Food warehouses and distribution centers with refrigerated and non-refrigerated sections often employ zone picking.
The key to finding the best picking method for your distribution center is trial and error. Some warehouses even use a combination of methods, such as zone picking combined with cluster picking (where each picker within a specific zone uses cluster picking) to maximize efficiency. Radio frequency identification picking also helps speed up picking times by eliminating the use of paper orders. Picking lists are sent directly to pickers via a wearable electronic device.
4. Perfect your warehouse layout
Optimizing the layout of your warehouse has the power to set your team up for smooth supply chain sailing or sink your whole operation. Efficient distribution centers are mapped out to create a seamless flow of products and personnel, from receiving to delivery truck loading.
Just like choosing the right picking method, laying out your warehouse can take some trial and error. Your most frequently purchased products should be the easiest for pickers to access, and this might mean you’ll need to move products around from time to time. For instance, let’s say you stock artificial Christmas trees. You’ll want them to be easy to access during November and December, but they can probably be safely stored on a high shelf in the back of your facility the rest of the year.
Make sure your aisles are big enough to safely accommodate foot traffic, pallets, and forklifts. Your packing center should be as close to your loading docks as possible, and you’ll need to have a staging area for delivery teams to load and unload vehicles.
5. Conduct regular warehouse audits
Warehouse audits are one of the most valuable tools at your disposal. Think of warehouse audits like an open book test. You’re sure to get an A even if you don’t know the answer off the top of your head; you just have to know where to look.
Internal warehouse audits are a way for managers to assess their team’s performance and identify areas that need improvement. Data collection during audits enables warehouse managers to track performance metrics over time, such as the accuracy of inventory counts or how efficiently the order fulfillment process is completed.
Audits should also be used to double-check inventory quality, make sure stock hasn’t expired, and verify that all safety protocols are being followed. While taking time away from actually moving products through your supply chain might slow down operations slightly, regular audits can save your business huge amounts of time and money in the long run.
Just consider forklift maintenance, for example. Audits help you determine if forklifts are being properly maintained. Ten minutes spent checking forklift maintenance logs and verifying that you’re up to date on safety checks could literally save you millions of dollars in damages and lawsuits. That’s what audits are for—they’re your business’ big cushy safety net.
Pro Tip: You don’t have to do one massive audit once or twice a year. Instead, break up your audits into smaller, manageable sections that can be performed once a month on rotation.
6. Set up a seamless returns process
Product returns are inevitable. In fact, RetailWire reported that the average return rate for ecommerce purchases is between 15% to 30%. So, you need to have a system in place to handle these returns, but even more than that, you can use reverse logistics to your advantage.
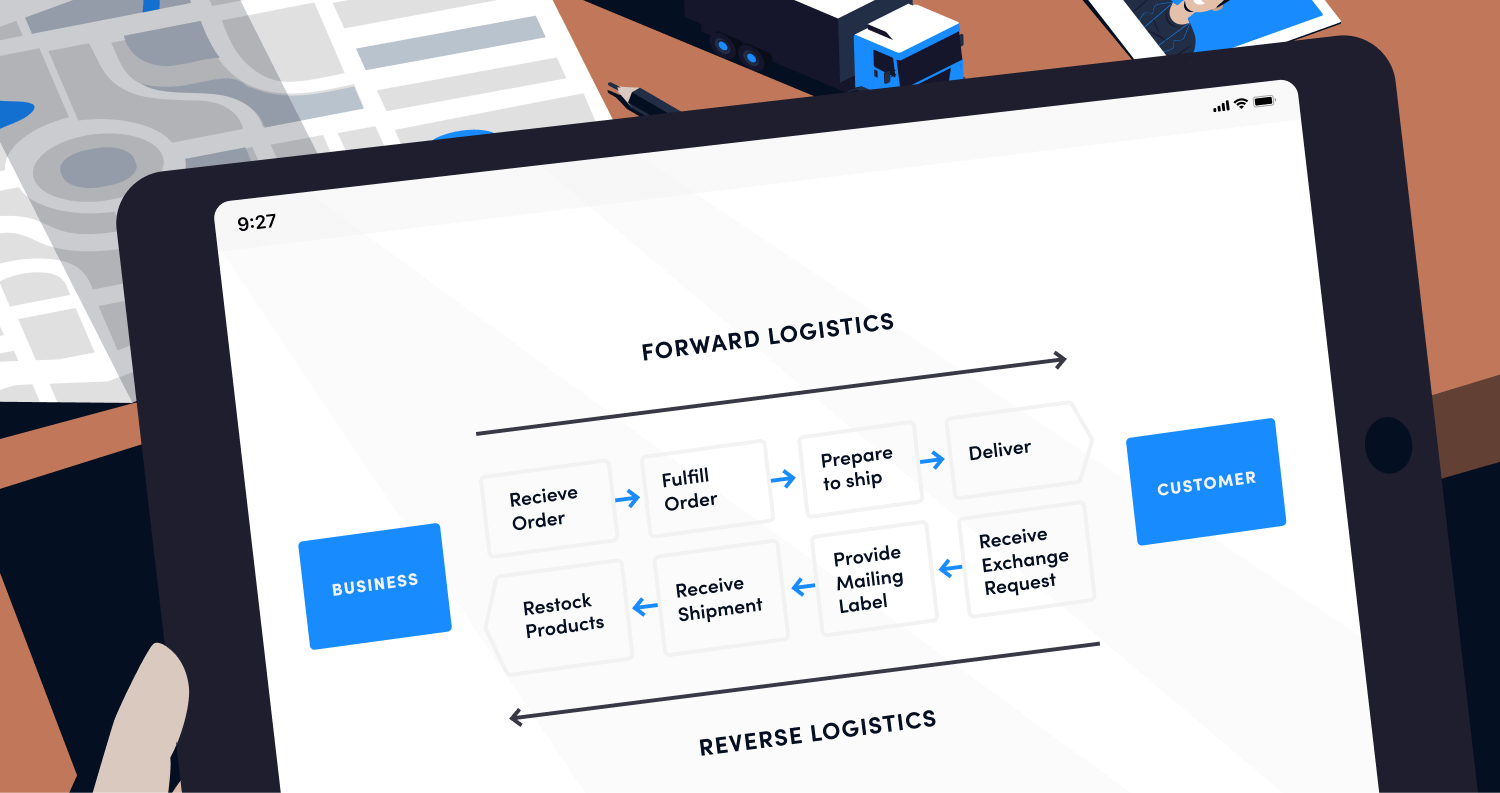
Distribution centers and third-party logistics companies that handle returns offer tremendous value for their retail clients because easy returns drive repeat sales. Ninety-five percent of consumers surveyed for Narvar’s 2017 consumer report, Making Returns a Competitive Advantage, said they would shop with a retailer again if they have a pleasant product return experience. Boost your bottom line by creating a seamless returns process.
Pro Tip: OptimoRoute can help with returns pick-up and get products back to your warehouse faster by combining drop-off and pick-up routes.
7. Reassess and make adjustments
Supply chain logistics are complex and always changing, so it’s important to reassess and adjust your warehousing processes periodically. Products may need to be rearranged based on seasonal demand. Employees may need additional training as they get promoted or whenever new safety protocols are adopted. Ask employees, from pickers to managers, where they think your processes could be improved. Trust your “boots on the ground” and tap into their unique experience.
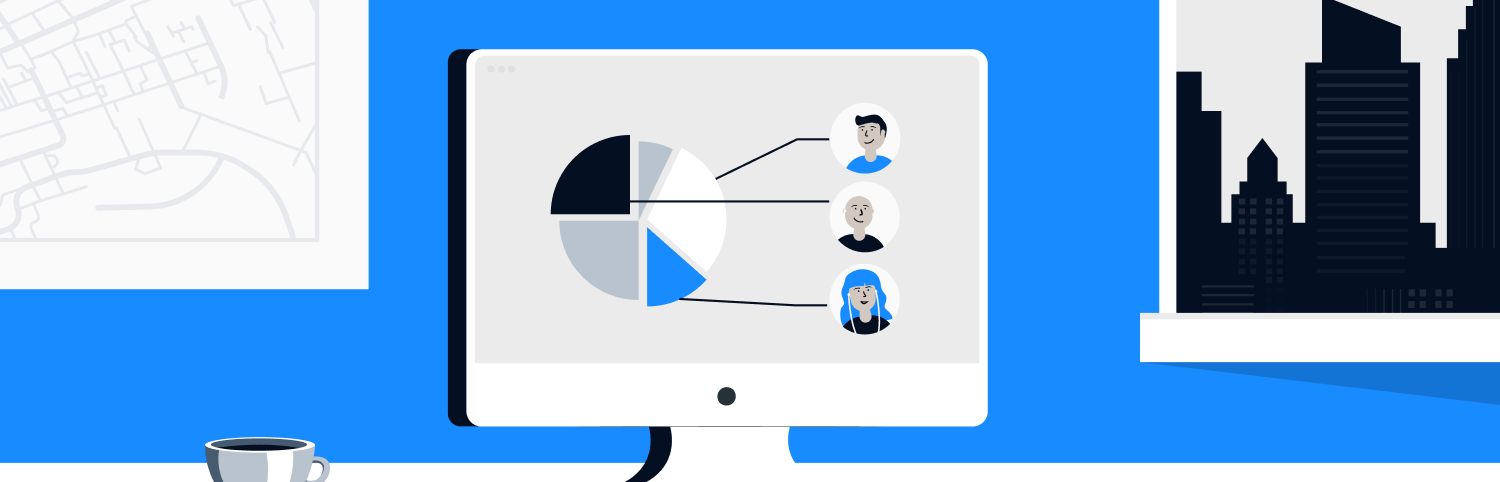
Use analytics to identify areas in which your team can improve or processes can be refined. OptimoRoute, for example, uses automation to track delivery teams’ on-time delivery rate for each driver and your team as a whole. You can see what’s going on from the minute the items leave your warehouse to the minute they are delivered. You can check the analytics in your WMS for statistics on how your warehouse operations are running. Use these insights to affect changes that drive your bottom line and increase operational efficiency.
Try OptimoRoute Free for 30 Days
Streamlined warehouse processes and optimized last mile logistics are the perfect pair. Together, they help you deliver an elite customer experience and drive your bottom line. Get started with OptimoRoute free for 30 days. Need help integrating our software with your warehouse management system? Our support team is here to help. Just send us a message or give us a call, and we’ll walk you through every step of the way.
Try OptimoRoute™ for Free
No installation or credit card required