Warehouse Layout + Route Optimization Software: The Essential Tools for On-Time Deliveries
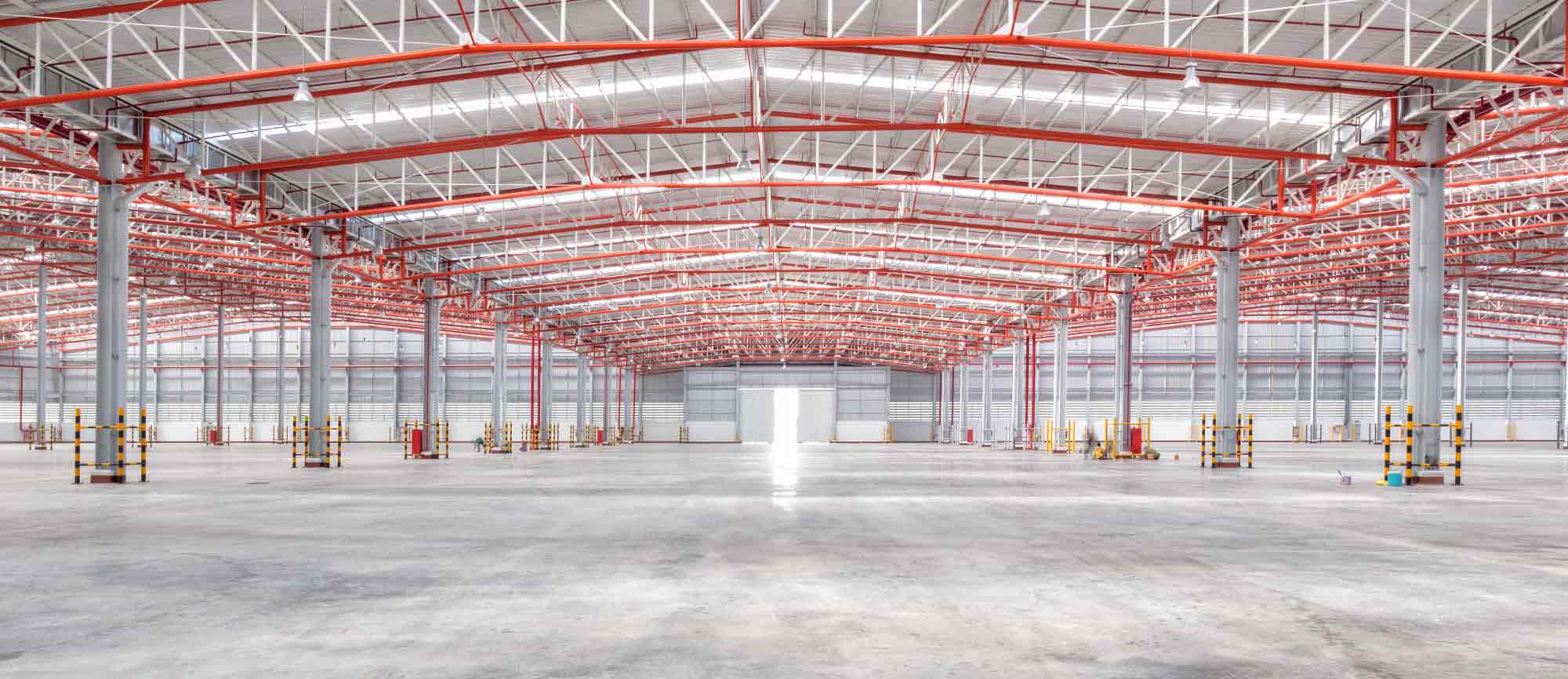
When companies want to improve their on-time delivery rate, they often focus on their delivery team. But that’s only part of the equation.
Delivery starts in your warehouse and ends on the road. So if you want to increase your on-time delivery rate, you need to optimize routing from the moment a customer order comes in.
Inside your warehouse, you control the environment. Design a great layout and your warehouse operations will naturally run more smoothly. Once you step outside, you can use advanced software such as OptimoRoute to increase your turnaround times.
Put these together? You’ve got a fully optimized route from your warehouse to your customer’s front door—and the perfect equation for on-time deliveries.
Topics covered in this article:
- Warehouse Layout Must-Haves
- What to Consider When Designing Your Warehouse Layout
- Warehouse Layout Design Software
- Use OptimoRoute to Conquer Last-Mile Delivery
(If you want to review some common warehouse terminology before you start, we also have a guide for that!)
Warehouse Layout Must-Haves
Before you start thinking of how your warehouse is laid out, let’s review the basics. No matter what type of products you manage, for an efficient warehouse and streamlined inventory management & order fulfillment your facility layout needs to include these essential elements:
Inbound Receiving Bay: Begin with a receiving bay. Make sure you allow enough space for products to be unloaded and scanned before being put away.
Storage Areas: Shelving units and pallet racking needs to be wide enough (and strong enough) to safely secure your inventory. Make sure your storage capacity can accommodate your inventory: if you need to store long objects, such as lumber or construction supplies, cantilever racks are a great option. If you offer food warehousing, make sure you consider how much of your storage space will need to be controlled at various temperatures, and block off areas for frozen foods, refrigerated foods, and dry goods.
Packing Space: Ensure there’s a large enough picking area for material handling; leave ample space for pickers to transfer product to packers, and for packers to prepare orders for shipping. Designate space for shipping materials to be stored as well.
Outbound Loading Docks: Your packing department should be located close to loading docks but not so close that they crowd the loading bay. Block off space for pallets and cargo to be staged before delivery trucks are loaded.
Office: Every warehouse needs a central command area or office where managers, dispatchers, and project-management teams can safely work away from the warehouse floor.
Break Room: You’ll also need an area for employees to sit during their break, lockers where employees can store personal belongings during their shifts, and a small kitchen or at least a refrigerator for employees to keep their lunch.
It’s a good idea to consider your parking lot and driveway structure as well. Your internal floor plan affects the flow of traffic outside of your building, so take time to think about how trucks will move in and out of your loading docks and how you want employees to access the building. You may need additional work areas if you have a quality-control division or a returns department.
What to Consider When Designing Your Warehouse Layout
There are several things you need to consider when creating your warehouse layout. Each of these elements will affect your process efficiency and on-time delivery.
Safety
Make sure everything is up to code. You don’t want to have to go back and redesign something or cease operations because your new warehouse layout doesn’t abide by OSHA guidelines. You’ll need to factor in enough space for equipment, such as forklifts, to safely navigate through aisles. Leave plenty of room for employees to safely walk down aisles and pass each other between storage bins. Also leave enough headroom for forklifts and machinery to clear lighting fixtures.
Proper ventilation is essential. You need to ensure that exhaust and carbon monoxide from forklifts, delivery vehicles, and other equipment won’t build up within your facility. Designate space for spill cleanup and eye-washing stations if you are going to store chemicals.
Traffic flow
Your warehouse layout should remove inefficiencies streamline the movement of products through each department and make all of your distribution center processes easier, from receiving shipments to auditing your warehouse. For example, your packing department should be located near your loading docks, not near receiving. Optimizing your warehouse layout like this ties in heavily with our distribution center best practices and procedures.
You should also consider the order-picking process you plan to use. Let’s say you operate a food warehouse, and you have three different zones: dry goods, refrigerated foods, and frozen foods. It would be smart to plan the zones in that order, with dry goods farthest from your loading dock because those items can withstand greater temperature fluctuations.
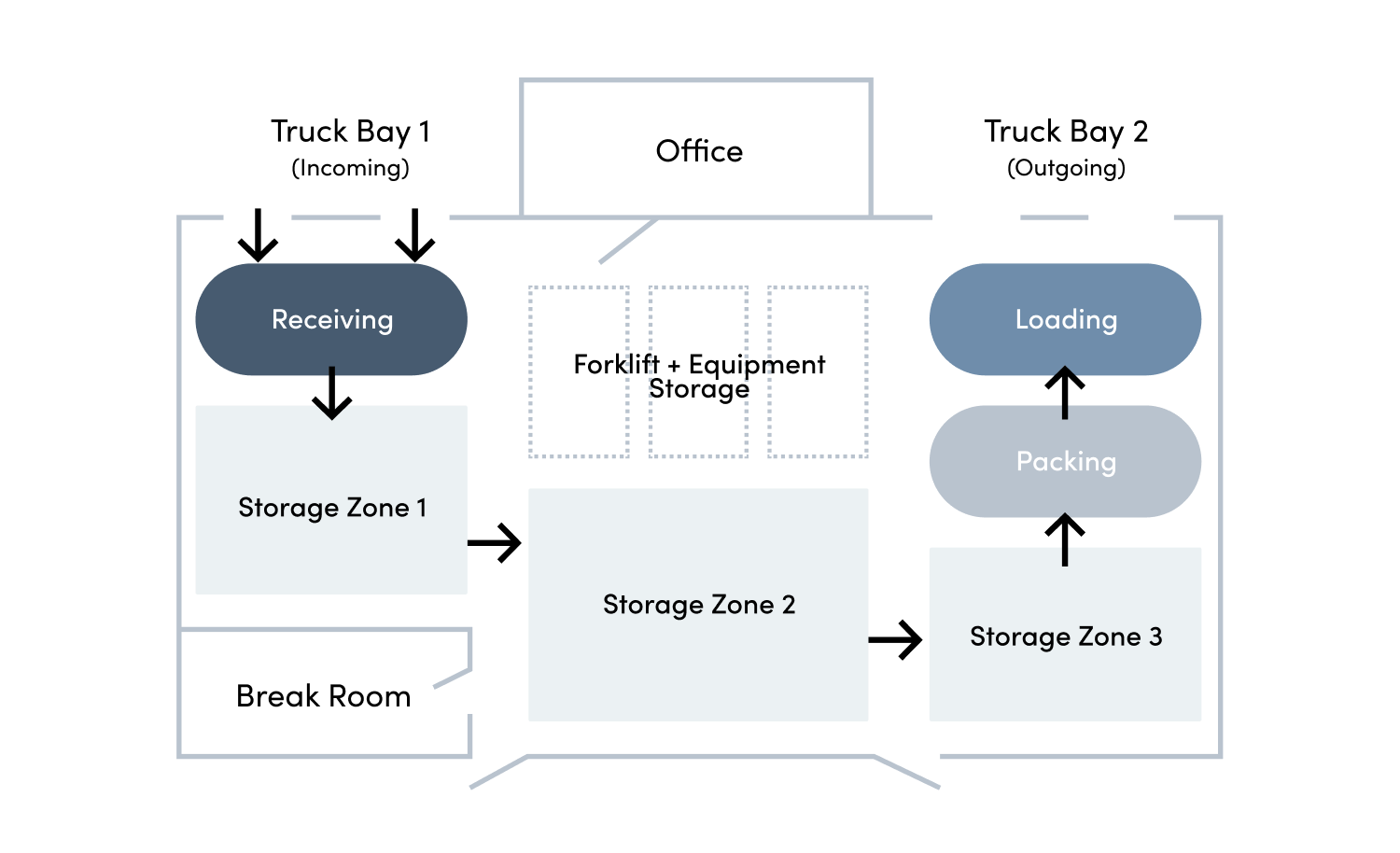
Frozen foods and refrigerated foods should be located closer to your loading dock (in zones 2 and 3 in the layout above).
Within each zone, you can then place the most popular items at the easiest to access ends or points. If we look at the diagram above, popular items in zone 3 should be placed near the top left corner, and items purchased infrequently should be stored near the bottom right corner. Items that are frequently purchased together should be stored close together, too, to reduce the number of steps a picker must take to assemble common orders.
Your delivery or shipping methods
If you have enough square footage, create separate packing zones for items that will be delivered versus items that will be shipped using third-party couriers. Products need to be packaged, weighed, and labeled differently, depending on which delivery or shipping method you’re using. So the more you can separate these two systems, the better.
It may also help to designate different loading docks for different couriers. That way, your team will know to always stage outgoing shipments for couriers in one area, and products for your in-house delivery team in another. The more you can do to clearly differentiate different processes within your warehouse, the less likely your team will make mistakes and the more efficient your whole operation will run.
Warehouse Layout Design Software
Use software to make the design process easier. Here are three different tools you can use to test out layout options and visualize your floor plan before building.
Draft it Free
As the name suggests, Draft it Free is free CAD (computer-aided design) software you can use to mock up your warehouse layout. If all you need is a simple 2D architectural design, Draft it Free is a great choice. And if you decide you need more advanced features, you can always upgrade to their Plus, Pro, or Architectural plan.
SmartDraw
You can use SmartDraw’s warehouse templates as a starting point. Customize your warehouse design by dragging and dropping elements within the grid. You can test out the software at no cost, but you won’t be able to save your work until you create an account. A single membership costs $9.95/month (billed yearly).
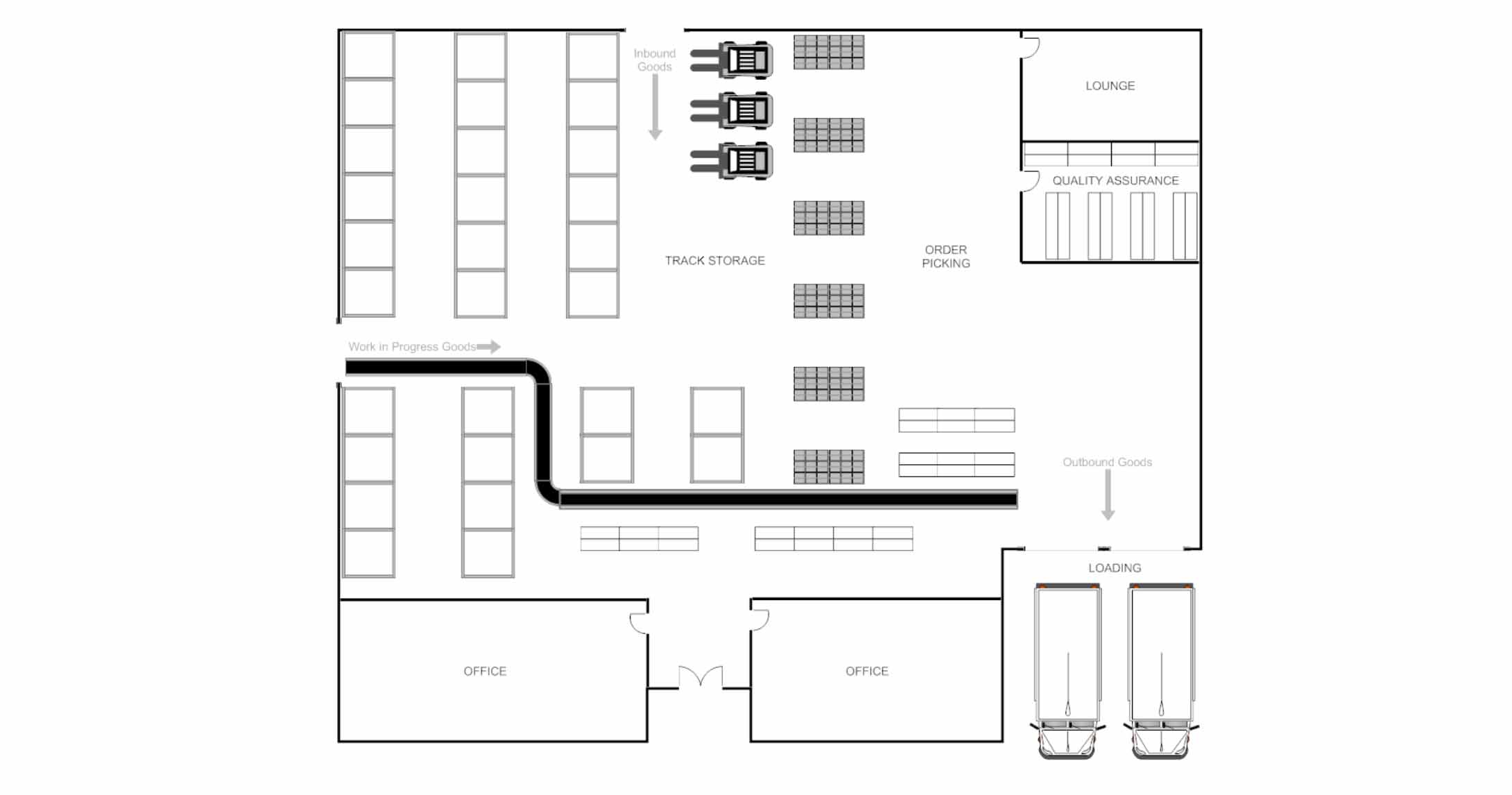
WarehouseBlueprint
If you want 3D mock-ups to help you visualize your design, WarehouseBlueprint has the features you need. With their heatmap extension, you can even map out your supply chain down to individual SKUS and, based on purchase frequency, place inventory within your blueprint. WarehouseBlueprint starts at approximately $57 (39 euros).
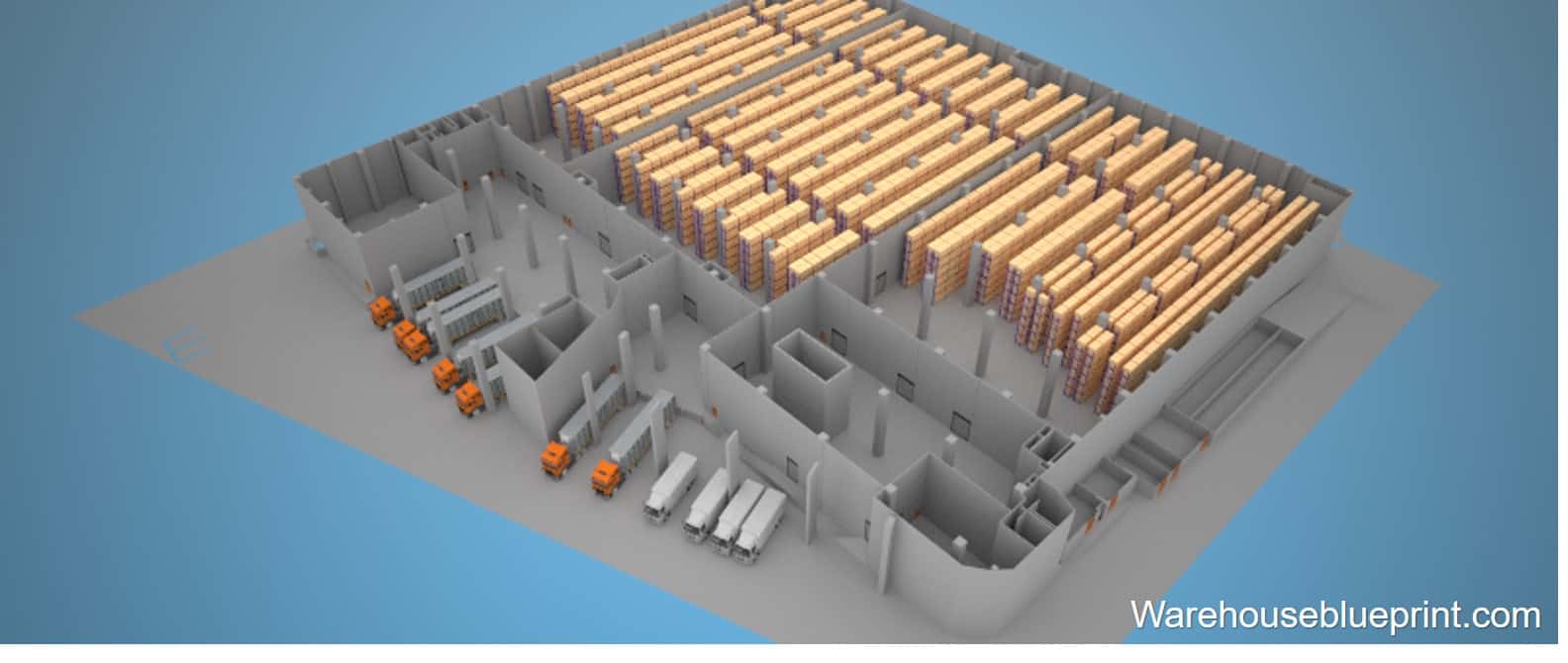
If it’s possible, walk through your layout in the space before you build your design. Tape or mark out where everything will go in your empty warehouse space, and have a few employees walk through workflows. This is a great way to spot issues before you’re too far along to be able to adjust.
Use OptimoRoute to Conquer Last-Mile Delivery
In the warehouse, the best way to become more efficient is by physically changing your warehouse layout, but outside the warehouse, you don’t have that luxury. You can’t change the roads or control traffic. The best you can do is optimize your own path. How do you do that? OptimoRoute.
Manual planning negatively affects on-time deliveries. It not only slows down the actual execution of last-mile deliveries but also requires more planning time. Hardie’s Fast Foods once routed deliveries manually. When they started using OptimoRoute, their overall fleet mileage dropped 20%, and their delivery-planning process became eight times faster. Their on-time delivery rate also improved from 89% to 94% (1.5% MoM).
Here are just a few of OptimoRoute’s advanced features and automations that you can use to increase your on-time delivery rate.
Automated Route Optimization: Click “Plan routes” and you’ll get the most efficient routes for thousands of deliveries and hundreds of drivers in a matter of seconds.
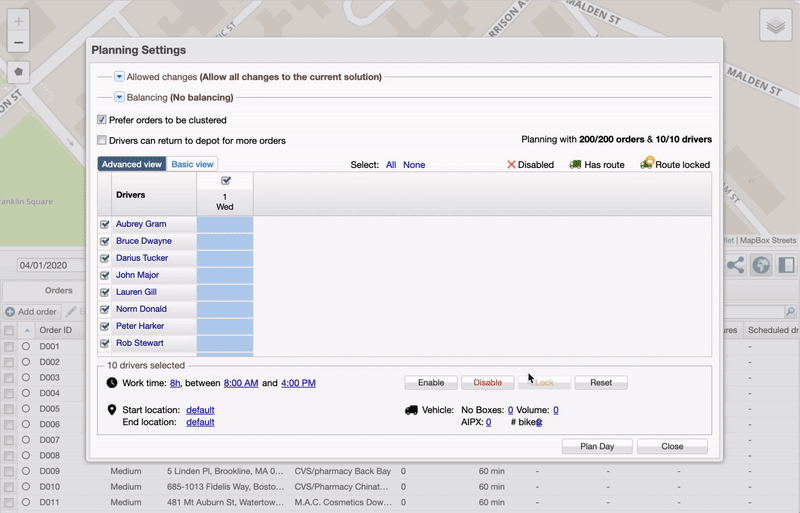
Driver and Vehicle Constraints: Set specific parameters for orders that need to be transported on refrigerated trucks, handled by a particular team, and more. Assign personnel and/or vehicle constraints for temperature-sensitive items, heavy loads, hazardous materials, livestock, or anything else you need to deliver.
Return to Depot: Plan multiple truckloads for individual drivers within a single shift.
Live Tracking: See where delivery drivers are along their route so you can precisely time picking and packing to minimize the time products are sitting on a loading dock waiting to be put on a truck. You’ll also be able to accurately assign loading time slots and increase capacity by reducing delays.
Combined Pickups and Drop-Offs: Easily schedule product-return pickups—reverse logistics—simultaneously with deliveries. Simply enter each vehicle’s unique cargo capacity and OptimoRoute will assign pickups at the optimal point when there is enough free space on a truck.
Real-Time Delivery Tracking: Deliver a superior customer experience with customizable notifications, including a link for customers to view their deliveries en route in real time. If you run in-house delivery, this feature reduces incoming customer service calls by as much as 70%.
You can try OptimoRoute at no risk and see how these features affect your on-time delivery rate. Activate your 30-day free trial today—no credit card required.
Streamline Your Tech Stack with API Integration
Much like a great warehouse layout creates a better flow of traffic across your warehouse floor, integrating your tech stack reduces bottlenecks in your digital workflow. Make sure your software and apps are all connected. Integrate OptimoRoute with your WMS (warehouse management system) or other tech using our Web Service API Integration.
Try OptimoRoute™ for Free
No installation or credit card required