Food Warehousing: Beat the Clock With Supply Chain Optimization
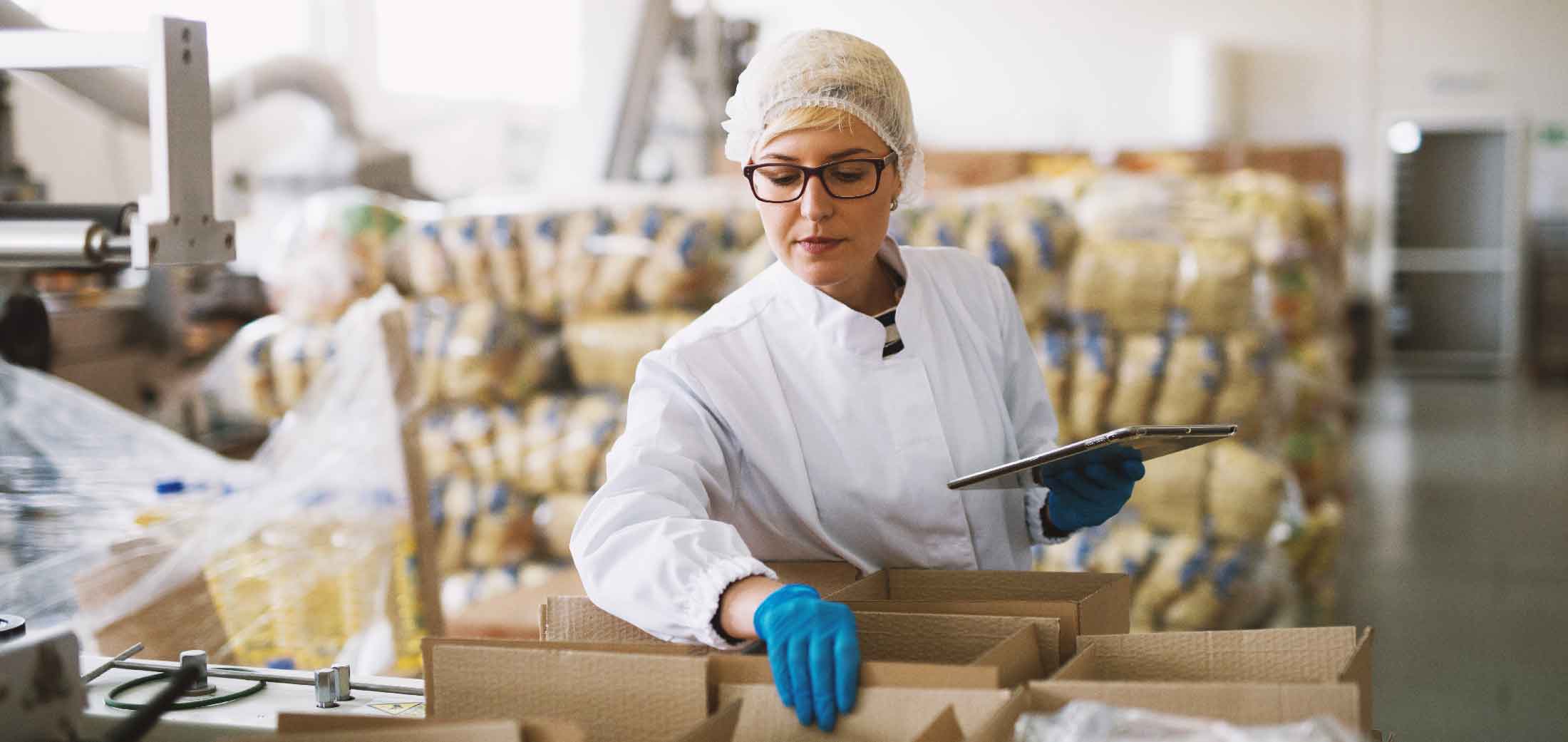
One of the biggest challenges food warehouses face is beating the clock. Time, it seems, is never on your side. Food expires, dairy and frozen products spoil if they spend too much time at the wrong temperature, transporting products requires careful synchronization of several moving parts, and disruptions happen all the time.
Food warehousing is a hard job, but it’s also extremely rewarding. After all, you’re a guardian of the food supply chain, delivering vital sustenance to the community.
And thankfully, there is a way to make your essential work way easier—by optimizing your supply chain.
Here’s how to simplify food warehousing and beat the clock with supply chain optimization:
- Begin Food Warehousing With the End in Mind
- Optimize Last-Mile Delivery With OptimoRoute
- Track Inventory in Real Time
- Protect Your Food Grade Warehouse Inventory
- Streamline Employee Training and Scheduling
- Use Analytics to Pivot Food Grade Warehousing
How to Optimize Food Warehousing in 6 Steps
Here we walk through a simple 6-step process that businesses can follow to optimize their food warehousing, gain efficiency, and boost their bottom line.
1. Begin Food Warehousing With the End in Mind
In his book The 7 Habits of Highly Effective People, Stephen Covey touts the benefits of “beginning with the end in mind” as a strategy for aligning tasks with a bigger goal or final objective. For food warehouses, beginning with the end in mind is the key to supply chain optimization and completing work in a timely fashion.
The end of your product journey—when your product finally reaches your customer—is your North Star. Every single supply chain process leading up to final delivery should be optimized for that end because the consumer drives your revenue. Without the consumer, you have no business; but keep them coming back, and you’ve got a recipe for long-term success.
If you start with the consumer and work backward, you quickly see that your delivery territory dictates the type of delivery vehicle you need: You don’t want products to spoil on their way to the consumer. For example, you could safely deliver cheese in an insulated bag if you’re only driving a few minutes away. But if that cheese is going to be on a delivery vehicle for eight hours, this presents a cold chain logistics problem and you’ll need to put it on a refrigerated truck. So, before you can pick the right delivery vehicle, you need to consider where you’re going.
Similarly, packing needs to be done in a way that prevents spills or cross-contamination during last mile delivery. How do you determine the precise packaging you’ll need? You consider the truck or vehicle they’re going onto and whether it’s a simple flatbed or has built-in food storage racks. To determine the best tactics for each step in your food logistics supply chain, you need to consider the one that comes after it—you need to work backward.
2. Optimize Last-Mile Delivery With OptimoRoute
Now that you know how to approach supply chain optimization, let’s talk about how to make it easier and faster: use software.
OptimoRoute is software designed to optimize (speed up and increase the efficiency of) the last mile of your supply chain, beginning with the customer experience.
Customize customer updates, then set them to automatically go out to customers when an order is en route. Your consumers will receive a live tracking link so they can see exactly when their order is going to arrive. Realtime customer notifications not only increase customer satisfaction, they also increase the likelihood of customers being home at the time of delivery and reduce the number of incoming customer service calls by as much as 70%. And yes, you’ll also get a superior rating for amazing customer service.
To get products to your customers, OptimoRoute enables dispatchers to route and schedule thousands of deliveries up to five weeks in advance in a matter of seconds. We have yet to meet a person capable of that kind of lightning speed calculation on their own, but if you know a superhero who can do this, we’d sure love to meet them! For the rest of us mere mortals, robust software is a powerful tool. Using OptimoRoute, all you have to do is upload delivery orders from a spreadsheet, input delivery windows and driver/vehicle constraints (such as a refrigerated truck), and click “Plan routes.”
To give you an idea of just how fast these calculations happen: Hardie’s Fresh Foods reduced their planning time by 87.5% and manpower required to do that planning by 60% when they switched from manual planning to using OptimoRoute. Their delivery capacity also increased 14%, fleet mileage went down 20%, and driver costs went down 12%.
OptimoRoute lets you easily assign delivery territories, plan routes with different starting and ending locations, and assign drivers multiple loads in a single shift. Dispatchers get live tracking so they can see where each truck is (or if they get held up in traffic) to coordinate picking, packing, and loading at precisely the right time. Dispatchers can even make adjustments to delivery routes after drivers are already in the field and send changes to the OptimoRoute Driver app on a driver’s phone.
3. Track Inventory in Real-Time
Real-time visibility is essential for food warehouse optimization and inventory management. When you know where things are, you don’t waste hours tracking them down. Knowing which food products are expiring next week or next month allows you to plan accordingly. It’s often what you don’t know or can’t find out quickly that kills optimization.
Traceability is a critical part of optimizing food logistics from point of production to point of sale—and knowing where your products are in real-time makes it a whole lot easier to maintain. A warehouse management system, or WMS, is software that gives you real-time visibility within the four walls of your warehouse. It abolishes the need for mounds of paperwork and clipboards and speeds up operations across your food distribution center, as well as simplifies the process of auditing your warehouse. Warehouse audits can be a source of anxiety, but when you use a WMS to schedule and monitor your audits, they become much less intimidating.
A warehouse management system, or WMS, is software that gives you realtime visibility within the four walls of your warehouse. It abolishes the need for mounds of paperwork and clipboards and speeds up operations across your distribution center floor, as well as simplifying the process of auditing your warehouse. When receiving clerks scan barcodes on incoming stock, those products immediately become visible to everyone else on your team. After those products are put away, your WMS keeps track of product expiration dates. You don’t have to worry about a pallet of expired food contaminating surrounding stock or attracting unwanted pests.
When orders come in, pickers receive pick lists via a handheld or wearable computerized device, which tells them where items are within your facility and what sequence to pick them in. The best part? WMS such as Logiwa or Infoplus Commerce can be integrated with route optimization software like OptimoRoute to give you real-time visibility from your warehouse all the way to your customer’s front door—seamlessly.
4. Protect Your Food Grade Warehouse Inventory
Once you’ve streamlined the day-to-day operations of your food warehouse, you can dig a little deeper. If food grade storage isn’t protected, your food is vulnerable to spoiling, food waste is likely, and food safety issues may arise. Accidents happen, but there are things you can do to mitigate your risks, and these tools will help:
Programmable thermostats give you more control over the temperature across different areas of your warehouse floor. Adjust for busy times of day, especially near loading or receiving docks where outside air gets in. If you have cold storage facilities, make sure to monitor the temperature in those storage areas closely.
Occupancy sensors automatically adjust lighting based on where activity is happening in your facility. Set lights to shut off or dim when there’s nobody nearby to keep the temperature from rising too high (and save on your electric bill). You can also connect occupancy sensors to thermostats to help regulate temperature.
Pheromone traps are a strong defense against common cold- and dry-storage pests, such as moths and beetles. Pest control is, unfortunately, something you must remain vigilant about for sanitation and quality control, and pheromone traps are a great weapon for food storage warehouses.
Catching problems early or preventing them altogether is optimization at its best. The easiest way to save time dealing with tons of spoiled food is to not let it spoil in the first place. Thermostats, sensors, and pheromone traps all help you avoid catastrophe and keep operations on track. And don’t forget about sanitation — make sure you have a good sanitation schedule.
5. Streamline Employee Training and Scheduling
Food warehousing workers need to follow rigorous FDA food handling regulations and safety standards. You are responsible for their training, but that doesn’t mean it needs to be a tedious and time-consuming process. Use software such as Eduflow to create interactive training modules for your staff and streamline the employee onboarding process.
Important note: Food industry training for federally regulated certifications, such as Preventive Controls Qualified Individual (PCQI), need to be led by a qualified instructor to be Food Safety Modernization Act (FSMA) compliant.
When it comes to day-to-day operations, employee scheduling software like PARiM makes personnel planning way more efficient. Easily manage employee payroll reporting, timesheets, uniform assignments, vacation days, and more from one platform.
Pro tip: Driver scheduling can be done through OptimoRoute for food warehouses that operate their own delivery team.
6. Use Analytics to Pivot Food Grade Warehousing
Every business has room for improvement, but finding bigger-picture inefficiencies can be tricky, especially for food service businesses where there are so many variables to take into account. Software analytics give you easily understandable metrics and insights about your business that you can use to make smart adjustments, get things done faster, and scale up successfully.
Tomato Mountain Farm, for example, used their OptimoRoute analytics to spot inefficiencies in their delivery system. They realized that they could execute more orders (and leave a smaller carbon footprint) with less driving if they reorganized their delivery territories and assigned a specific day of the week for each zone to receive deliveries. Based on insights gleaned from their analytics, Tomato Mountain Farm successfully pivoted. They increased their subscribership from 300 to 1,200 members without quadrupling delivery planning and execution time.
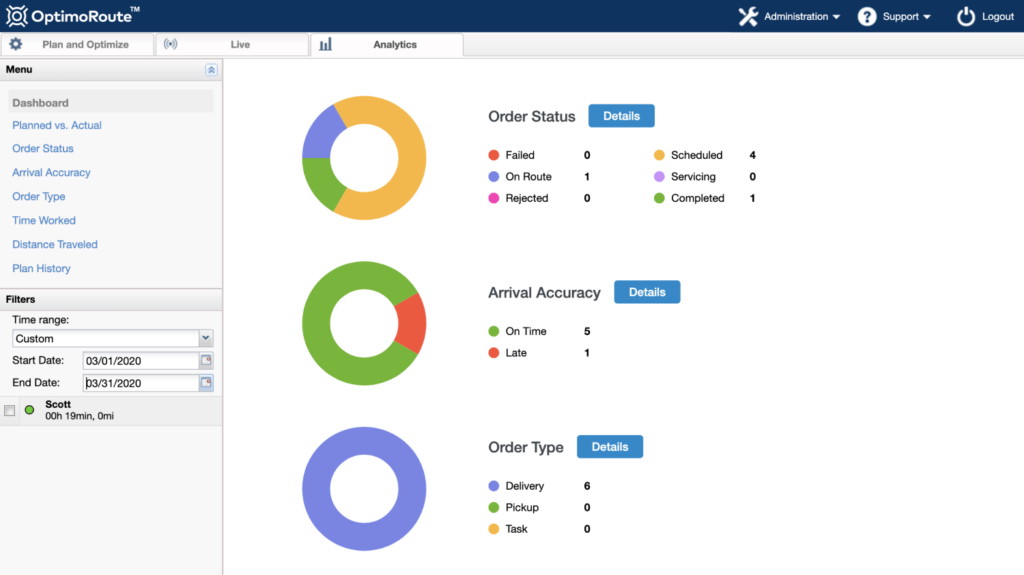
Most WMS, employee scheduling, and other software have analytics, too. Whether you want to identify areas of wasted spend or calculate exactly what you need to expand your business, analytics is the best place to start.
Food Warehousing FAQ’s
What is food warehousing?
Food warehousing is the process of storing food products before they are sold or further distributed. Warehousing operations span the food supply chain to provide storage, handling, and other services.
How do you store food in a warehouse?
Warehouses have a variety of methods for storing food products, from dry storage to freezer storage. It all depends on the food product being stored.
What is the importance of food warehousing?
Proper food warehousing helps food companies minimize the risk of spoilage or contamination. Warehousing is also important for ensuring timely delivery of products and optimized food distribution.
Try OptimoRoute Free for 30 Days
Few things make a food-buying experience better than getting a free sample. And at OptimoRoute, we think you should get to sample software, too. That’s why we offer a 30-day risk-free trial. Get started today. No credit card required.
Try OptimoRoute™ for Free
No installation or credit card required