How Logistics Scheduling Keeps Everything on Track (and How to Simplify It)
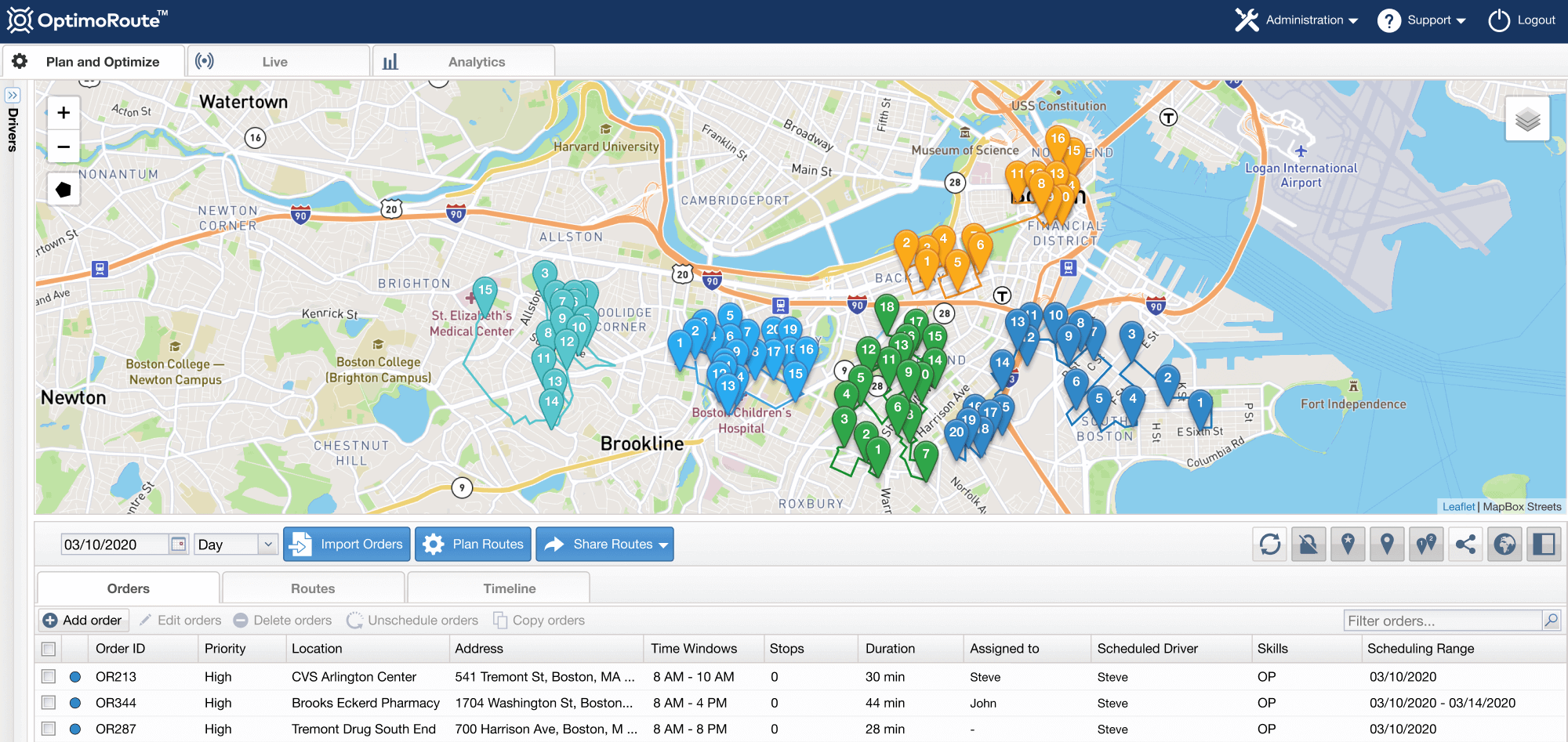
Scheduling is one of the most important factors in the success of any logistics chain. Done right, it can drive revenue. Done poorly, it can cause your whole operation to come to a grinding halt.
There’s nothing worse than falling behind on production or missing a shipment because a certain stage of the logistics chain wasn’t completed at the right time. Logistics scheduling is how you make sure that doesn’t happen.
In this piece, we will demonstrate why logistics supply-chain scheduling is an important skill and will show you how to easily streamline the entire scheduling process. You’ll also learn why last-mile delivery is the most important stage when it comes to your customers’ satisfaction.
What is Logistics Scheduling?
Logistics scheduling is the process of planning specific days and times to move a product or service through a logistics workflow or pipeline. This can include everything from scheduling certain parts to arrive for production or dropping your packaged product off at your customer’s door at a scheduled time.
Why Logistics Scheduling Is So Important
Your whole supply chain begins and ends with logistics, which means logistics scheduling has a huge effect on your revenue. In a global survey, Deloitte found that more than two-thirds of retail and manufacturing businesses with high-performing supply chains show an above-average increase in revenue.
How do you wind up with a high-performing logistics chain? Scheduling early and often is a key factor. One of the most popular methods is called forward scheduling, which involves completing each stage of the logistics chain immediately as soon as the requisite time and resources are available. The better you get at time and resource scheduling, the deeper your understanding of each step in the logistics process and the better your overall planning abilities will be.
Let’s say you typically schedule 30-minute windows for delivery trucks to be loaded. When one pulls away from your loading dock, another pulls in, and you begin the loading process again. But you have two trucks that take 45 minutes to load because they are slightly larger. Every day that one of those larger trucks is loaded first, your entire team begins their day 15 minutes behind. If your drivers then run into traffic or get hung up on a tricky delivery, a 15-minute delay can snowball into a 2-hour delay by the end of their shift. If one piece of the logistics puzzle is operating inefficiently (or running behind schedule), it will affect every step in the process that comes afterward, and small delays add up quickly.
Logistics scheduling helps reduce these time delays by showing managers where congestion or hold-ups are occurring and then giving them the power to make corrections. A schedule that is precisely broken down becomes a road map for the success of your entire supply chain.
Last-mile delivery ensures that your customers keep coming back
Last-mile delivery is the final stage in a delivery process where goods are physically transported to consumers, typically from warehouses or distribution centers. As the customer-facing part of the logistics process, last-mile delivery is one of the most important components in the entire process. No matter how seamless your procurement, production, and packing processes are, if your deliveries are late, you’re going to have unhappy customers.
Resource and time scheduling for last-mile delivery have become increasingly challenging thanks to retailers like Amazon offering fast and free delivery options on everything from food to electronics. More than half of online shoppers say that they want their products delivered in 3 hours or less. Pair this expectation of an ultra-fast turnaround time with customers’ low tolerance for tardiness and it becomes clear that even small businesses need to nail last-mile delivery.
Luckily, improving your logistics scheduling process by harnessing the power of technology can reduce the time it takes to plan last-mile deliveries by as much as 90% while increasing efficiency and tripling capacity.
Real Results of Logistics Scheduling
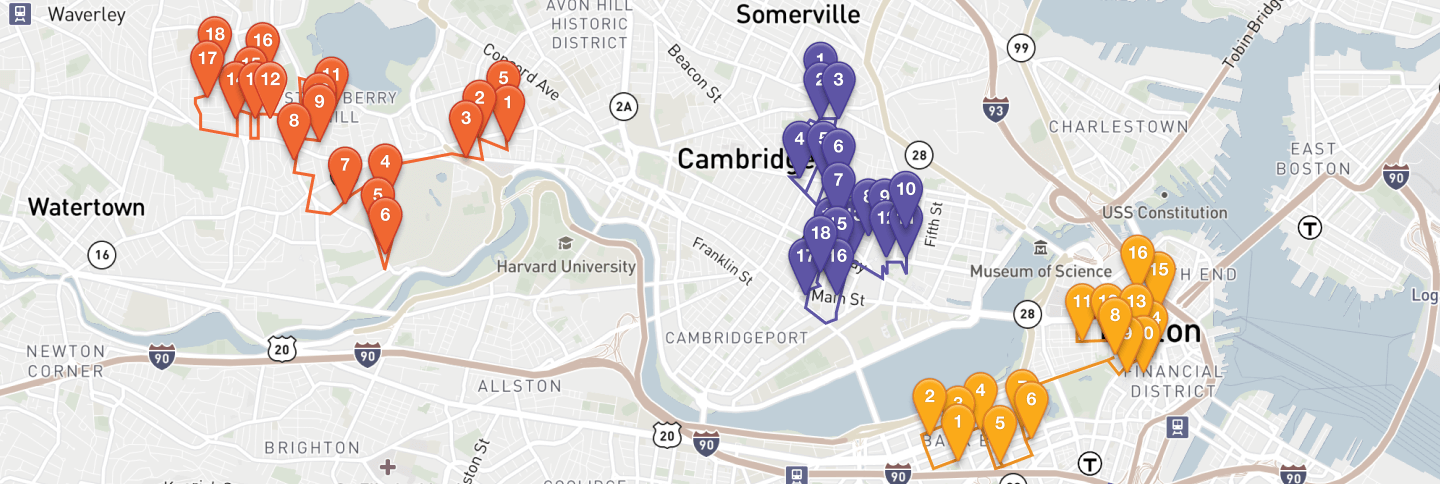
There are numerous benefits available to companies that streamline their logistics process, all of which add up, helping to increase revenue. Here are just a few:
Better risk management + scalability
Scaling any part of a logistics chain requires precise knowledge of how long each step in a pipeline takes. And logistics scheduling provides solid numbers you can work off of to achieve almost any business goal. Whether you need to order more supplies or hire seasonal employees, logistics schedules show you what needs to be done today, tomorrow, next week, and/or next month to get the job done and meet demand.
On the flip side, your logistics schedule can be used as a road map for spotting areas where you can cut costs if demand suddenly decreases. In the face of unforeseen circumstances, well-planned schedules can help managers determine which supply orders can be delayed or canceled, whether workers’ hours can be reduced, and which supplies need to be used first so they don’t expire.
Less overhead + fewer stockouts
A great schedule ensures that every step in a logistics process is moving at just the right speed to get a job done on time — not too early and not too late. This balance is key because it results in both less overhead and fewer stockouts (which cause significant customer churn).
Let’s say you run a custom graphic T-shirt business, and you have bulk orders of blank shirts delivered on the first Tuesday of every month. You have a small warehouse and limited space for surplus materials. You know that in April (leading up to Mother’s Day) you see a rise in demand for women’s shirts, but in late May and June (leading up to Father’s Day), you see a rise in demand for men’s shirts.
Using keen logistics scheduling, you could adjust your men’s and women’s T-shirt supply deliveries to accommodate this demand without needing extra space in your warehouse. You might double your April order of blank women’s shirts and cancel your May order. Simple logistics scheduling like this can save you square footage in a warehouse and ensure that you don’t run out of shirts to print during a rise in seasonal demand.
More time + fewer expenses
Proper logistics scheduling ensures that you’re planning ahead rather than scrambling to catch up. Ordering supplies early reduces the occurrence of rush orders (and the higher costs they incur). Effective last-mile logistics scheduling reduces haphazard routing and trips back to a depot, which means less mileage, lower fuel costs, and less vehicle-maintenance expenses.
Efficient scheduling, by definition, takes less time, which means management teams will have greater capacity to focus on logistics strategy and higher-level planning.
More on-time deliveries + happier customers
We discussed the risk of losing customers (and revenue) if your last-mile delivery is subpar. The good news is, well-executed last-mile delivery offers some huge benefits. Great last-mile delivery scheduling results in more on-time deliveries, which means more happy customers and more positive reviews.
The process of last-mile delivery scheduling requires that managers gain a deep understanding of not only how long driving from location to location takes but also how long a driver needs to be stopped to drop off a package. By understanding and accurately scheduling each window, your entire operation runs more smoothly, and it becomes easier to deliver on time.
Driver breaks can then be scheduled to have the least impact on an overall route, and driver workloads can be better balanced across an entire fleet. It will become easier to create schedules that ensure on-time delivery, which will keep your customers coming back.
How to Improve Logistics Scheduling With the Right Software
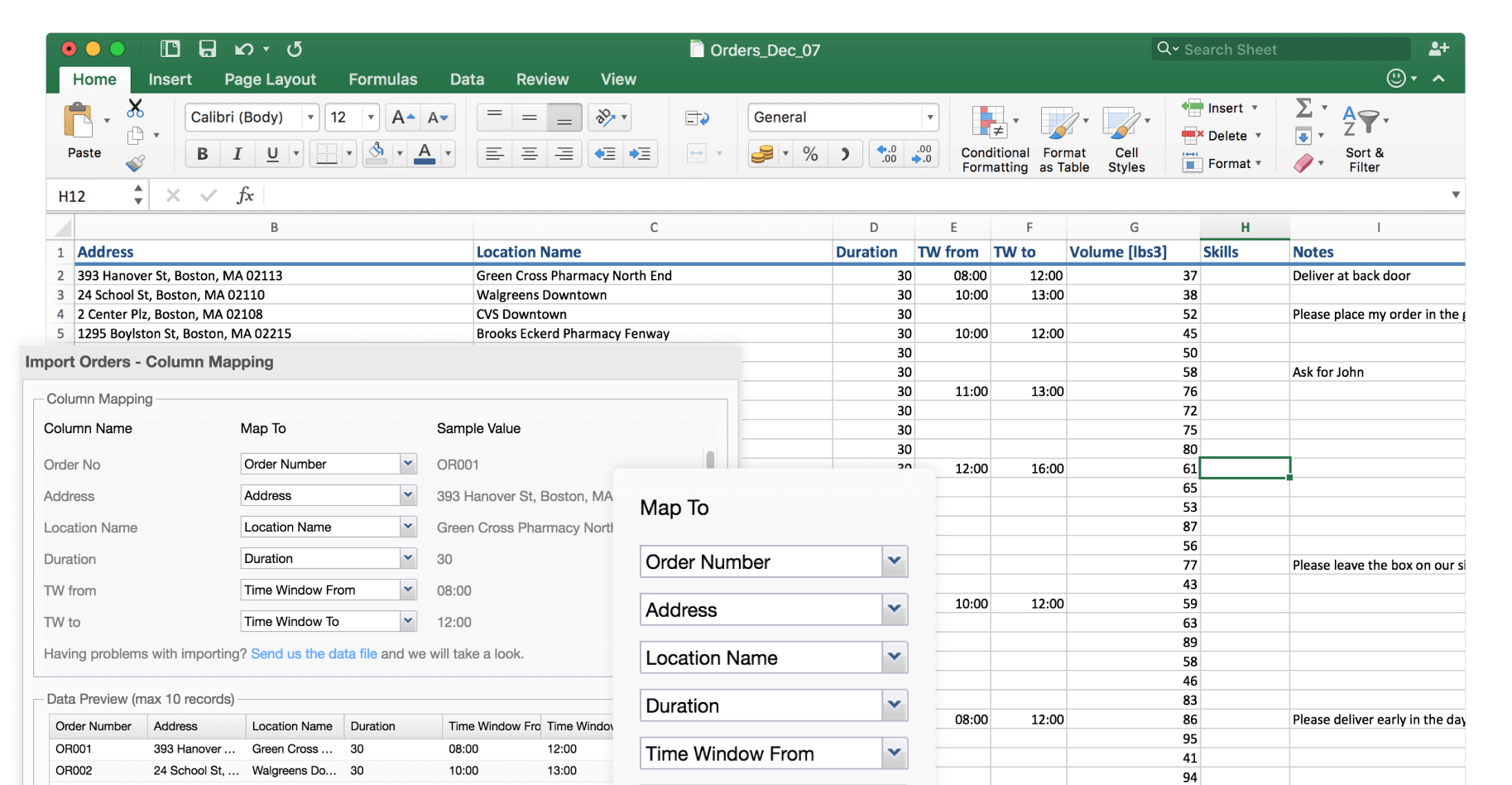
Logistics scheduling involves a lot of numbers and a lot of moving pieces. Many scheduling problems are the result of slow manual calculations and can be solved simply by embracing technology. Using the right software for each stage can help you achieve synchronicity across your entire supply chain and save your employees lots of time.
Here are some of the key logistics touchpoints to consider and how you can simplify these processes with technology.
Procurement
Spend-management software, such as Procurify, can save you a lot of time and money. Ordering supplies can be a huge headache if your company doesn’t have an easy process in place for expense approvals. If your procurement team has to wait around for approval every time they need to order something, this can seriously affect your turnaround times across an entire logistics chain.
Procurify’s vendor-management feature enables managers to fill out and send purchase orders in a matter of seconds. Real-time budget-tracking clearly shows you how your expenses are adding up and keeps spending on track. Preapproved spending limits reduce the need for lengthy approval processes and keep your whole logistics pipeline flowing efficiently.
Inventory management
Keeping track of stock is extremely difficult without software like Sortly, which makes product tracking and stock-level management intuitive. Sortly provides a user-friendly way for product companies to manage supply levels, minimize warehouse costs, and avoid stockouts.
Taking the graphic T-shirt business example from above, Sortly would clearly show how many blank shirts the company currently had. This could be broken down by men’s versus women’s shirts, colors, sleeve lengths, fabric type, and much more. Instead of having to manually count stock and take notes with a pen and clipboard, everything is accessible via a phone, tablet, or computer when you use Sortly. Real-time visibility from anywhere gives managers and leadership the power to make informed decisions.
Last-mile delivery
If you’re looking for a last-mile logistics scheduling solution, OptimoRoute can help. Our software gives logistics schedulers the ability to plan five weeks in advance. Hundreds of optimized routes with multiple constraints can be scheduled with the click of a button, and schedules can be easily adjusted if unexpected changes occur or new customer orders come in.
Scheduling is easy and efficient for orders with faster turnaround times, too. Businesses like Evolution RX, an independent pharmacy in Texas, use OptimoRoute to plan and schedule complimentary deliveries of prescriptions to local customers.
With OptimoRoute, individual vehicle cargo space can be factored into planning so that full capacity is utilized and trips back to a depot to reload are minimized. Businesses such as The Little Posy Co., a flower and gift shop in Western Australia, use this ability to ensure that their delivery operations are as efficient as possible, even on busy holidays, when they commonly see a 400% increase in order volume.
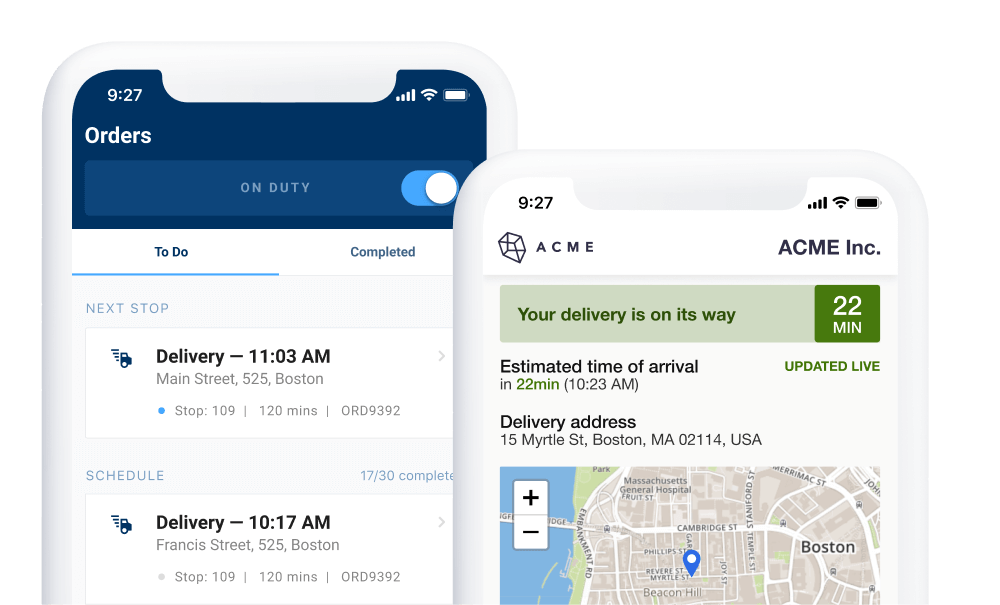
Reduce your operational costs by 30%
Increase delivery capacity by 43%
Plan 7x faster
Just like Procurify and Sortly, OptimoRoute offers real-time visibility, but for your entire field service team. Live tracking uses breadcrumbs to show managers where drivers are in the field, so any deviations from their planned route are easy to spot. These breadcrumbs and the OptimoRoute analytics tools can help managers improve employee scheduling, appointment scheduling, and routing in the future. Live tracking keeps customers happy, too. Tracking links show consumers where their package is and let them know precisely when it will arrive.
OptimoRoute has intuitive features for scheduling driver breaks and workload balancing as well. When it comes to last-mile delivery, OptimoRoute streamlines the entire scheduling process, which benefits your business, customers, and employees.
Reverse logistics
Whether you’re picking up used appliances and bringing them to a recycling facility or handling product returns/exchanges, reverse logistics is a major part of the logistics process for many businesses. Paying close attention to this portion of logistics scheduling can save you a lot of time and help mitigate some of the negative effects of product returns.
Both OptimoRoute and Sortly will increase the efficiency of reverse-logistics scheduling and planning. OptimoRoute enables pickup routes to be combined easily with preexisting delivery routes, which cuts down on planning time, fuel costs, and driver hours. When it comes to product returns, Sortly makes restocking products easier and mitigates any confusion that could occur from changes in stock levels.
Depending on what type of company and logistics you’re managing, there are many other software and selling platforms that can help you streamline logistics scheduling. Shopify offers a range of solutions for ecommerce stores. Integrating your tech stack will simplify the process even further and save you even more time.
Your Partner in Logistics Scheduling and Beyond
The OptimoRoute team is here to help you with overall scheduling, planning routes, and using data analytics to improve your last-mile and reverse logistics. We’ve helped hundreds of businesses, from small family-owned shops to large corporations, boost the efficiency of their logistics process and increase revenue. Getting started is easy with our 30-day free trial. Have questions? Talk to a member of our customer support team.
Try OptimoRoute™ for Free
No installation or credit card required