Maintenance Management Software (CMMS): Definition, Key Features & Best CMMS Solutions [2024]
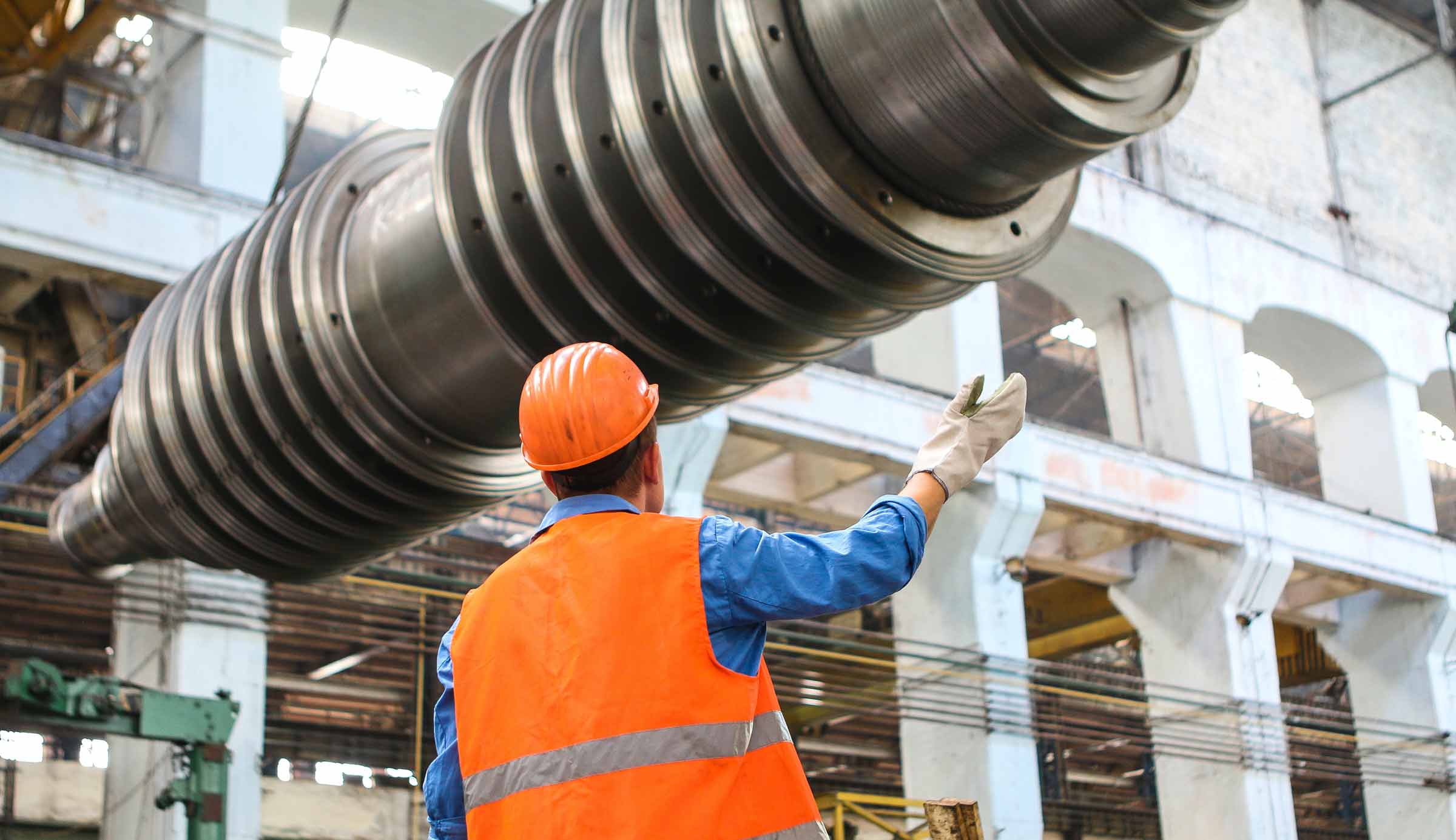
Managing the maintenance for your company’s equipment or facilities seems like a straightforward task. But 70% of companies aren’t aware of when their equipment needs maintenance.
Lack of awareness for equipment and facilities maintenance is dangerous for your business. If a machine on your factory floor shuts down without warning, you’ll miss your production goals and, by extension, your revenue goals.
It’s dangerous for your employees too. If your team is operating equipment that hasn’t been maintained at the right time, they can be hurt.
Maintenance management software (CMMS) helps companies streamline and automate the processes they need to maintain their equipment and facilities. With a CMMS, companies can efficiently maintain their machinery and facilities on time and avoid harmful consequences that come with faulty equipment or damaged facilities.
Maintenance management software doesn’t make sense for every business that has maintenance needs. Small businesses and businesses with multiple locations may be better served by using route optimization software instead.
Let’s break down what maintenance management software is, what businesses need it, and the top CMMSs in the market right now. We’ll also share why CMMS tools aren’t enough — businesses need to add route optimization tools to the mix as well.
Jump to the section that most interests you:
- What Is Maintenance Management Software? Why Is It Important?
- What Does Maintenance Management Software Do?
- What Businesses Need Maintenance Management Software?
- 4 Top Maintenance Management Software Solutions
- CMMS Tools Aren’t Enough. You Need Route Optimization Too.
- Enhance Your Maintenance Management Software With Optimoroute
What Is Maintenance Management Software? Why Is It Important?
Maintenance management software, also known as computerized maintenance management systems (CMMS), refers to the tools that help companies keep track of and service their inventory, parts, vehicles, and other equipment.
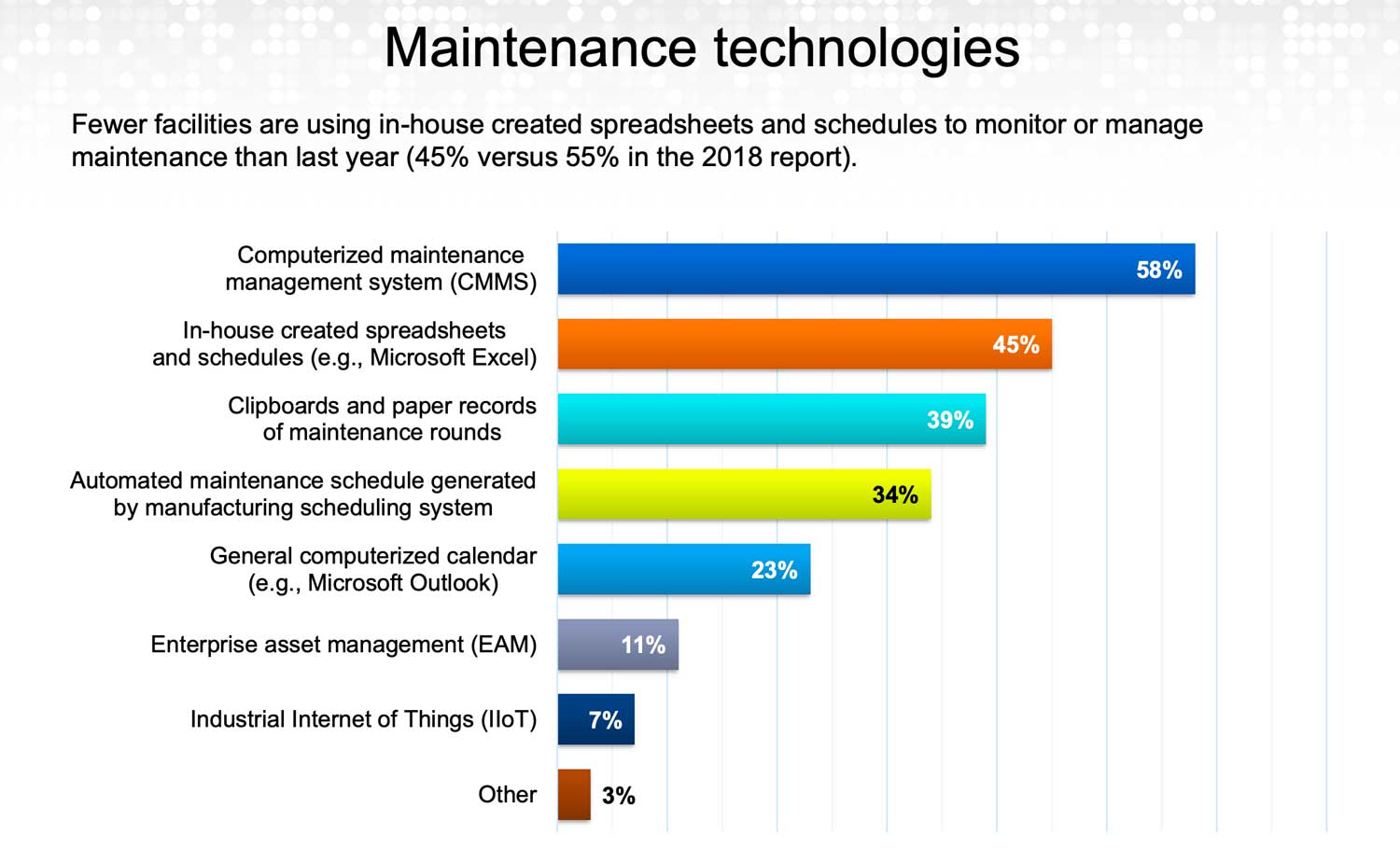
CMMS tools help companies efficiently manage equipment service. A 2019 survey revealed 45% of facilities use spreadsheets to manage their equipment, which leaves room for errors and oversight by service teams.
These tools also help companies avoid unscheduled downtime on the production floor. Equipment downtime is expensive for businesses — according to Aberdeen, the average cost of unexpected equipment downtime is $260,000 per hour.
What Does Maintenance Management Software Do?
CMMS tools have four essential functions for businesses: work order management, inventory management, maintenance checklists, and reporting and analytics.
1. Work order management
Maintenance technicians can use CMMS tools to create and track work orders to service equipment on both a reactive and a preventative work order management schedule.
Reactive management refers to situations where a piece of equipment is damaged and requires immediate repair.
Preventative management (also known as planned maintenance) refers to regular service schedules that fix possible equipment issues in advance.
These aren’t the only types of maintenance management businesses need to keep in mind when managing their equipment and facilities — for more on this topic, check out this article.
2. Inventory management
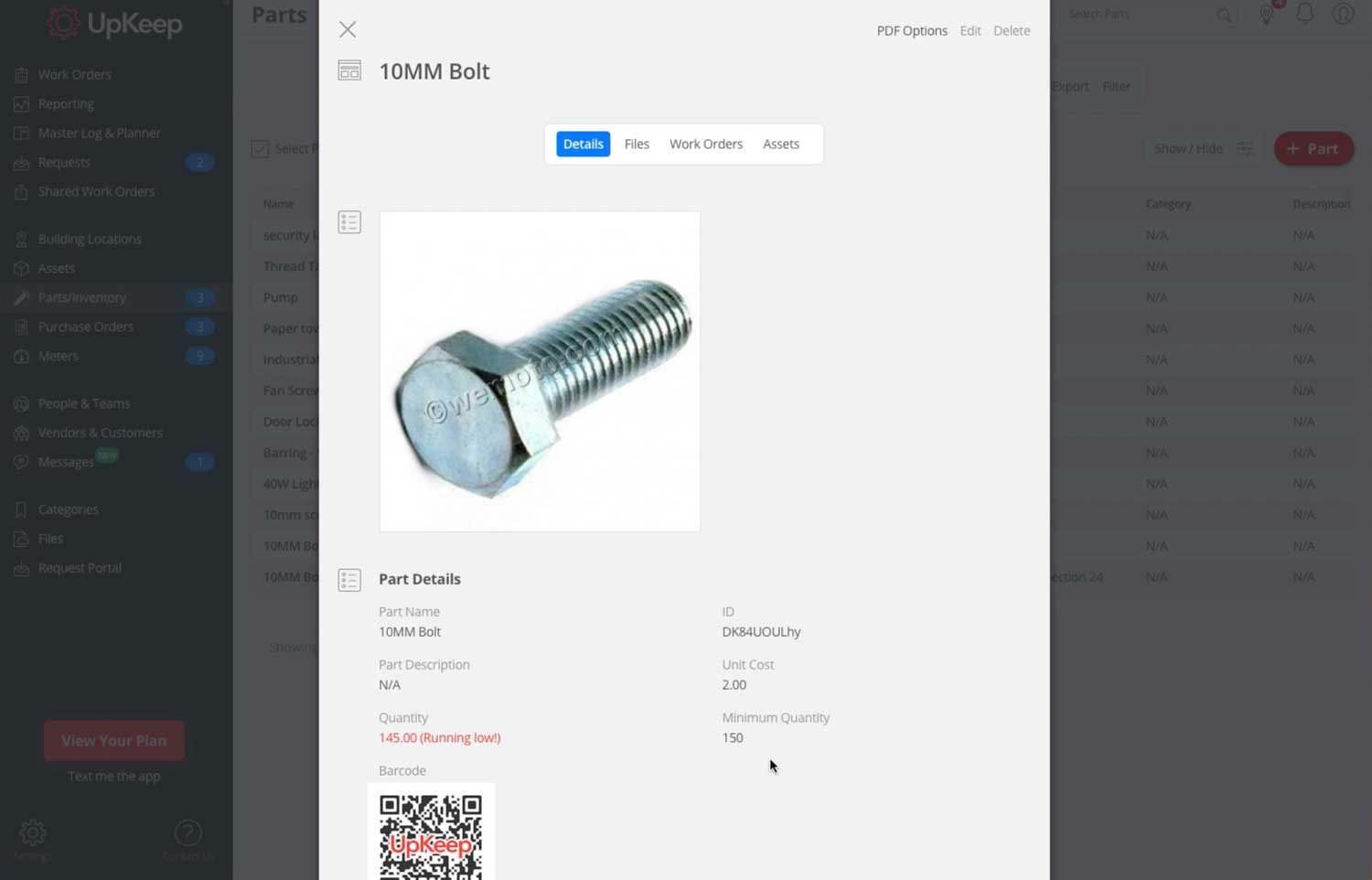
CMMS tools have real-time inventory and asset tracking so technicians can repair the company’s equipment or facilities.
If you don’t have the spare parts to fix a damaged vehicle or piece of equipment, your repairs will get delayed.
CMMS inventory management tools help you restock parts so you can avoid running out when you need them the most.
3. Maintenance checklists
Checklists ensure all your technicians follow the same process for repairs.
In order to fix a problem or finish servicing quickly, a technician might skip key steps to get the job done. This might cause issues later on because the repairs were not fully addressed.
Another reason to use checklists is to give your team the flexibility to assign less experienced technicians to repair equipment. They can follow the steps in your checklist to make sure they repair that equipment as well as a more experienced employee. This reduces dependencies on senior technicians.
4. Reporting and analytics
CMMS software gives you the ability to evaluate your team’s performance and identify your best performers as well as technicians who might need more training and support.
You can also identify which of your assets have been repaired the most, which helps you decide whether you need to replace them.
What Businesses Need Maintenance Management Software?
CMMS platforms work best for businesses that manage their equipment and facilities in one location in these industries:
- Manufacturing
Manufacturing companies rely on specialized machinery to produce their goods. CMMS tools enable them to maintain their equipment regularly and ensure they don’t suffer from unexpected equipment failures or worker accidents linked to faulty machines. - Facility maintenance
Facility maintenance teams can use CMMS tools to manage maintenance work for HVAC, electrical, and plumbing units across a business’s facility. - Agriculture
Agricultural businesses can use CMMS tools to handle maintenance operations for their farming equipment year-round. - Property management
Property management companies can use CMMS tools at each of their properties to manage maintenance requests and conduct preventative maintenance for shared appliances like laundry machines, fitness equipment, elevators, etc. Check out our guide on property management software for more solutions to streamline property management.
4 Top Maintenance Management Software Solutions
If you’re in the market a CMMS system, you have plenty of highly-rated options to choose from. All four maintenance management solutions we mentioned here contain work order management, inventory management, maintenance checklists, and reporting functionalities. They also have accompanying iOS and Android mobile apps to give technicians the flexibility to log work order status updates from their mobile devices.
1. UpKeep
UpKeep is a CMMS solution used by brands like Marriott and Yamaha. It’s one of the highest-rated CMMS solutions on Capterra, with a rating of 4.7 from 1,200+ reviews. It’s one of the only solutions to offer 24×7 live support, and it also offers a free version businesses can try before they decide to sign up for a premium plan.
2. Fiix
Fiix is a CMMS solution offered by Rockwell Automation, which is one of the oldest manufacturing services and industrial automation brands in the U.S. Fiix offers integrations with enterprise resource planning (ERP) and internet of things (IoT) tools like Nanoprecise and Oracle NetSuite. It also offers a free version for businesses to try before they decide to sign up for a premium plan.
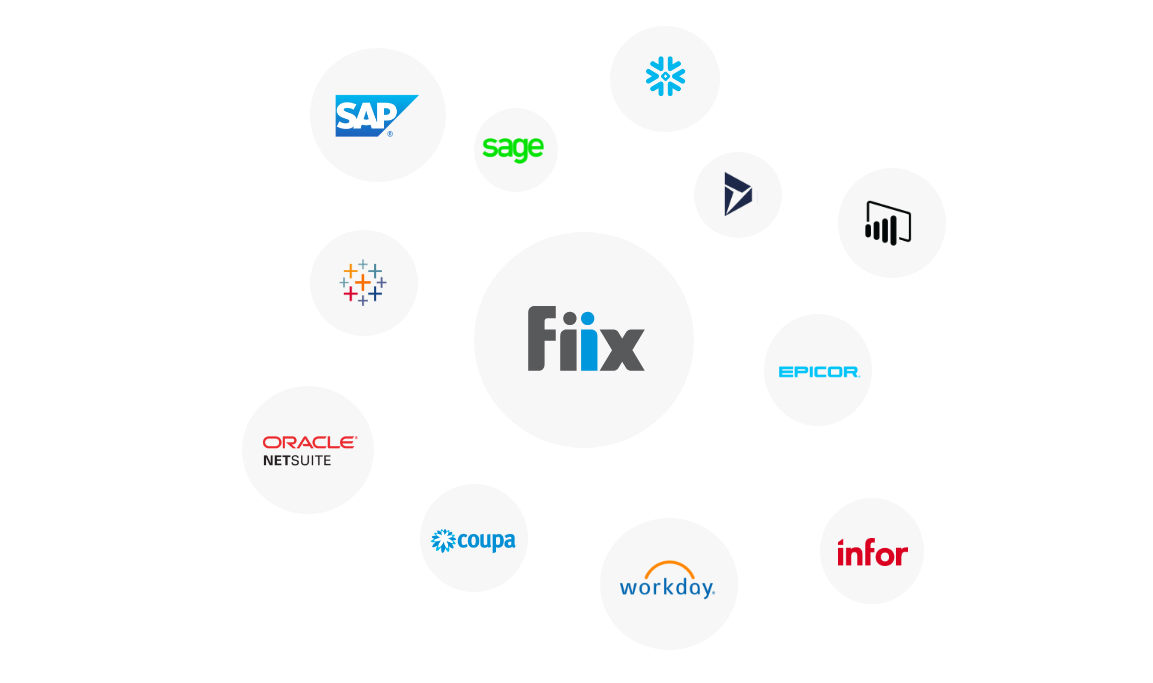
3. Hippo CMMS
Hippo CMMS is a CMMS solution optimized for facilities management teams. It has interactive floor plans businesses can use to pinpoint facility issues and areas of improvement. It also offers onsite facility audits to businesses looking for preventive maintenance solutions.
4. eMaint CMMS
EMaint is one of the oldest CMMS solutions in the market since its creation in 1986. It’s a well-rated CMMS tool for businesses — it was declared the 2020 Gartner Peer Insights Customers’ Choice for Enterprise Asset Management Software and was rated as Best Support by G2 in Fall 2020.
CMMS Tools Aren’t Enough. You Need Route Optimization Too.
If you’re a small business or a business managing your equipment across several locations at a time (like a field service management (FSM) business or a logistics and delivery business), you might want to consider a more flexible solution to optimize your maintenance management needs.
Small businesses don’t need to use a CMMS solution in their daily operations. They don’t have the scale of equipment or facilities that require a CMMS solution to help manage them. Small businesses should consider going with a more flexible platform that scales with them instead of paying for features they don’t need.
FSM and logistics businesses operate across multiple locations in their daily operations. FSM businesses send technicians to multiple customer sites to service their equipment and their appliances. Logistics businesses send their delivery teams across distribution centers and customer locations.
CMMS solutions aren’t sufficient for these types of businesses because they don’t have route optimization features. Without FSM technicians and logistics personnel can spend time and money in the field inefficiently. They often visit fewer customers per day or make a lower number of deliveries on behalf of their business.
This is where route optimization software like OptimoRoute comes in. OptimoRoute’s route optimization features make it easy for FSM and logistics businesses to route their orders efficiently and save them money in the long term. Companies like Telgian and Hardie’s Fresh Foods have reduced their resource costs and increased their delivery capacity with OptimoRoute.
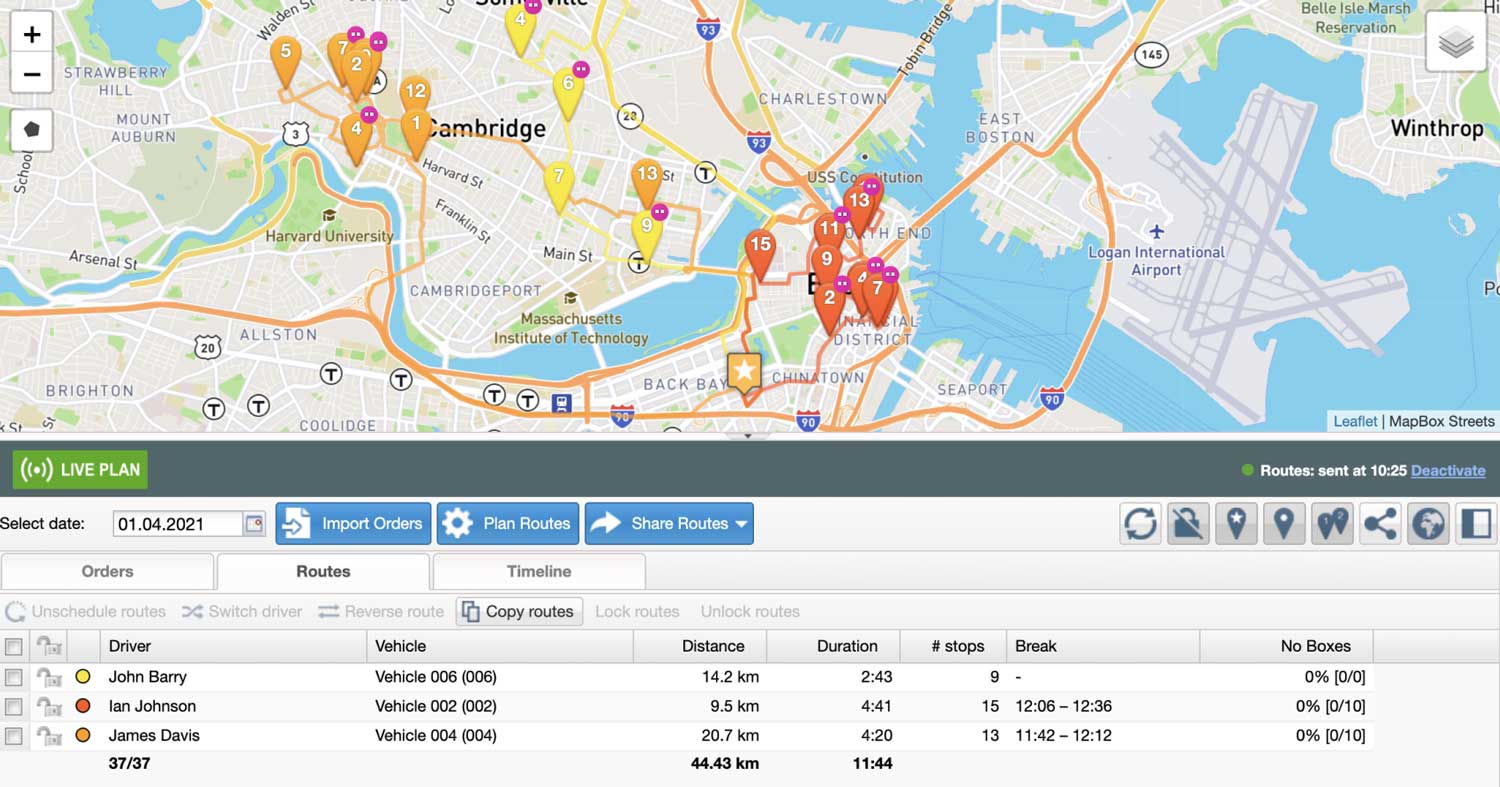
CMMS tools also lack automated planning features important for FSM and logistics businesses. Automated planning is an additional cost that adds up as these types of businesses grow. They become reliant on teams of dispatchers to allocate work orders to technicians and delivery staff, which costs time and money.
With OptimoRoute’s automated planning features, FSM and logistics businesses don’t need large teams of dispatchers to plan their orders. Their route plans are also more efficient because OptimoRoute can account for constraints like vehicle capacity and technician skills, which are important to improve key metrics like on-time delivery and first-time fix rates.
Enhance Your Maintenance Management Software With OptimoRoute
If you’re a business with a single location facility, you’ll find value out of a maintenance management software platform. However, if your business has multiple locations or has to manage maintenance for a wide array of customers, you might be better served using OptimoRoute in addition to your CMMS.
We enhance your CMMS tool so your technicians can visit service sites efficiently. Our Web API can be integrated in your CMMS so data flows seamlessly between them.
It’s free to get started with OptimoRoute. Start your 30-day free trial today!
Try OptimoRoute™ for Free
No installation or credit card required