Maintenance Management: Have You Got All the Angles Covered?
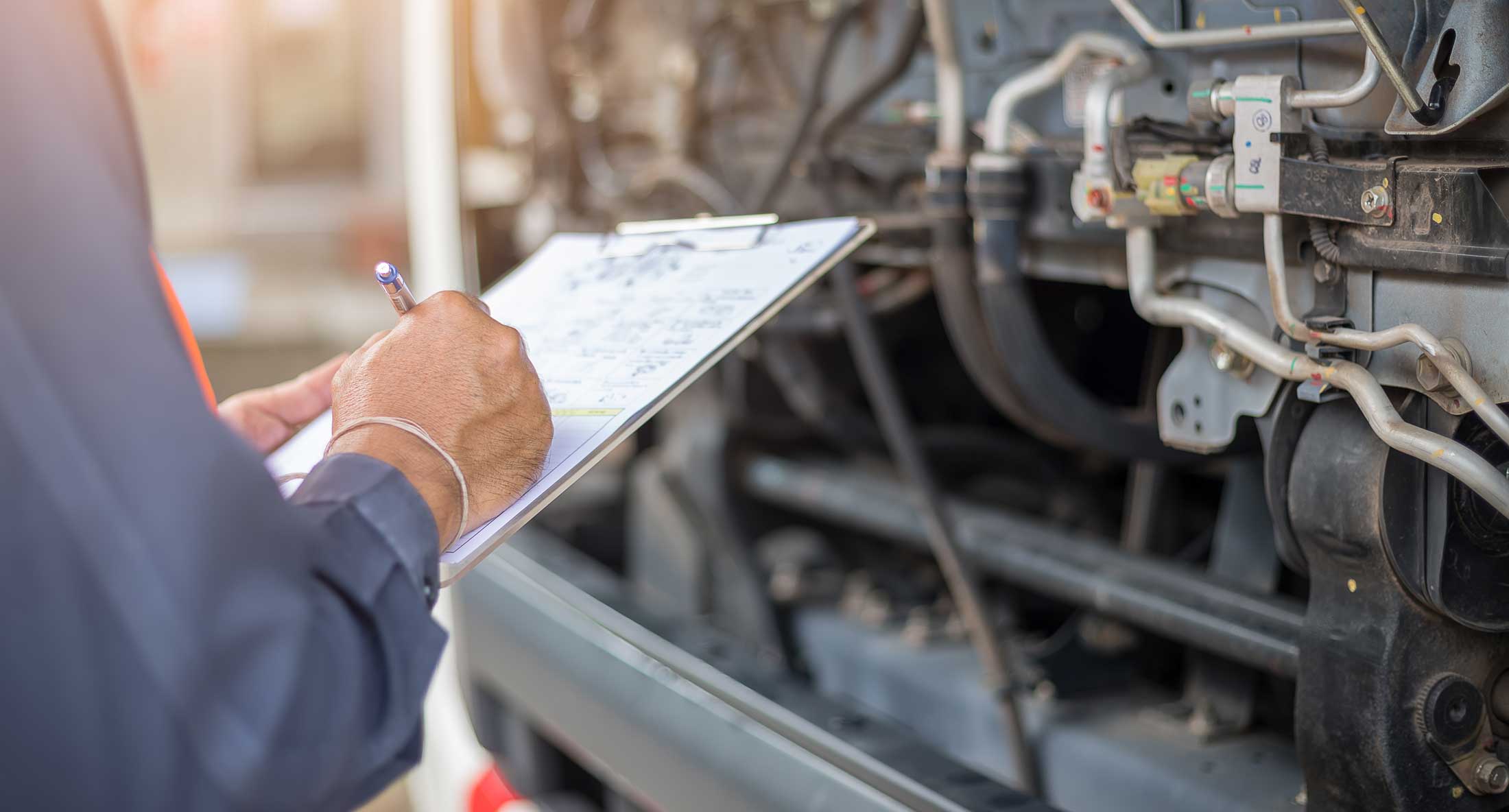
Since you’re reading this, you’re probably wondering: What is maintenance management, and why does it matter?
When you’re running a business, the last thing you need is an abrupt failure of equipment. If it’s a key piece of equipment, it can bring your entire business to a grinding halt.
According to the 2019 Maintenance Report, 40% of unscheduled downtime is caused by aging equipment, and 24% by unexpected mechanical failure.
Maintenance management can help you prevent mechanical failures caused by a lack of service. It can even expand the lifespan of aging equipment until you can afford to replace it.
Let’s dive deeper into what exactly is included in the term maintenance management, which businesses use it, and how to improve it in your company.
To navigate to the section which interests you the most, click below:
- What Is Maintenance Management?
- Why Is Maintenance Management Important?
- What Are the Types of Maintenance Management?
- What Companies Need Maintenance Management?
- Do You Need a Digital Maintenance Management System (CMMS) Software?
- Improve Your Maintenance Program Efficiency
What Is Maintenance Management?
Maintenance management is the process of planning, scheduling, and managing maintenance for parts, vehicles, and other essential equipment.
It involves predicting potential issues and scheduling regular maintenance tasks to eliminate them.
A basic example is scheduling regular oil changes and checkups for the trucks in your fleet. More complex strategies involve using machine learning to predict which parts are experiencing the most stress and need to be replaced.
With more real-time data, you can streamline your maintenance process and make it more cost-effective.
But that’s not the only reason why it is so important for businesses.
Why Is Maintenance Management Important?
According to ServiceMax, 70% of companies aren’t aware of when their equipment needs maintenance.
That significantly increases the risk of unscheduled downtime, which can be incredibly expensive. According to Aberdeen, the average cost of unexpected equipment downtime is $260,000 per hour.
If it’s a key machine, it can interfere with your entire product life cycle or supply chain.
Even on a smaller scale, a single unexpected vehicle breakdown means a full truckload of delayed shipments, including possible ruined merchandise and lost revenue.
Beyond the cost savings, a reliable maintenance plan can also help with regulatory compliance and avoiding fines.
The concrete benefits and cost savings vary based on the type of maintenance management you choose.
What Are the Types of Maintenance Management?
There are many different strategies for maintenance management, including preventive, reactive, predictive, and more.
Let’s take a closer look at the pros and cons of each type.
Reactive maintenance
Reactive maintenance (or breakdown maintenance) is a typical approach for many small businesses. Basically, you wait until the equipment breaks down before you do anything about it.
Of course, you risk losing time and money on unexpected breakdowns, no surprise here. But unscheduled maintenance tends to be more expensive as well.
It’s a bad idea.
Preventive maintenance
With preventive maintenance, you regularly schedule maintenance activities. You can use time or a metered metric like miles driven to set the schedule.
Getting an oil change every 6 months or 5,000 miles is an example of this strategy in action.
The upside is that it’s easy to implement, and can reduce unnecessary breakdowns and repairs.
But it’s not perfect. You may spend money and time on equipment that doesn’t need it. Plus, roughly or heavily-used equipment may not get enough attention.
Predictive maintenance
Predictive maintenance is when you monitor the condition and performance of equipment in real-time to schedule servicing and avoid downtime.
It’s the perfect way to keep maintenance costs low, while also keeping your business running.
In addition to predicting issues, most companies also do some preventive maintenance tasks like lubrication or oil changes.
Usage-based maintenance
Usage-based maintenance measures the usage of equipment and uses the metrics to forecast and schedule the next service. It is a step above preventive maintenance, while not fully predictive.
It could measure miles driven, number of products handled, or something else. It depends on the business.
UBM is cheaper to implement than full-fledged predictive analytics, with similar benefits. Especially for transportation-related maintenance, as many fleet managers already have the functionality.
Reliability-centered maintenance
Reliability-centered maintenance is about working backward from your company’s most essential processes. Then you work out which ones are likely to break and adjust your maintenance operations.
You may use a mix of preventive and predictive maintenance to achieve goals. It’s a great way to boost core maintenance KPIs and reduce unscheduled downtime.
What is the most popular maintenance strategy?
In 2019, the most popular strategy was preventive maintenance, used by 78% of companies. It’s the easiest kind of maintenance program to set up.
Regular lubrication, oil changes, replacing worn with new spare parts, it’s not complicated. It’s the easiest way to do effective maintenance.
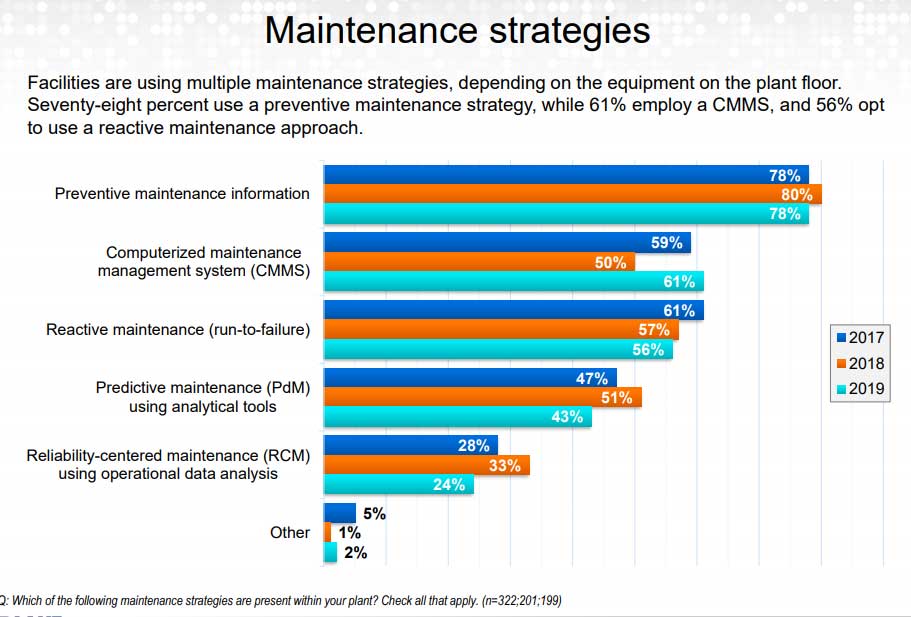
Of course, if you want your maintenance managers to make more informed decisions, you can invest in PdM or CMMS systems.
What Companies Need Maintenance Management?
Many different companies rely on maintenance management to keep their business running at full capacity.
Let’s take a closer look.
Field service and maintenance companies
If clients hire you to keep their companies running, you need an effective system for managing maintenance.
From work order management to predicting and preventing issues, you need a process in place. Trying to do things manually will only lead to confusion and bad decision making.
Logistics, distribution, and delivery service companies
Without an effective maintenance management program, you won’t get the most out of your private fleet.
Vehicles may break down unexpectedly causing delays (or ruining sensitive goods like food). You’ll also spend unnecessary time and money on lightly-used vehicles.
HVAC installation, repair, and maintenance companies
For HVAC companies, a data-based maintenance program is key to keeping your customers satisfied.
You don’t want the AC to break down within a few months or years of installation. That could ruin your reputation.
A great program can also secure ongoing revenue rather than just a one-time installation fee.
Pool maintenance companies
Today, most pools rely on a few different machines to stay safe and clean. If you don’t have an efficient maintenance program, you risk algae growth, pump failures, and losing your clients.
Do You Need a Digital Maintenance Management System (CMMS) Software?
For smaller companies and maintenance teams, you don’t need to implement a dedicated solution.
Preventive or usage-based maintenance can give you 90% of the benefits, with a lot less up-front investment.
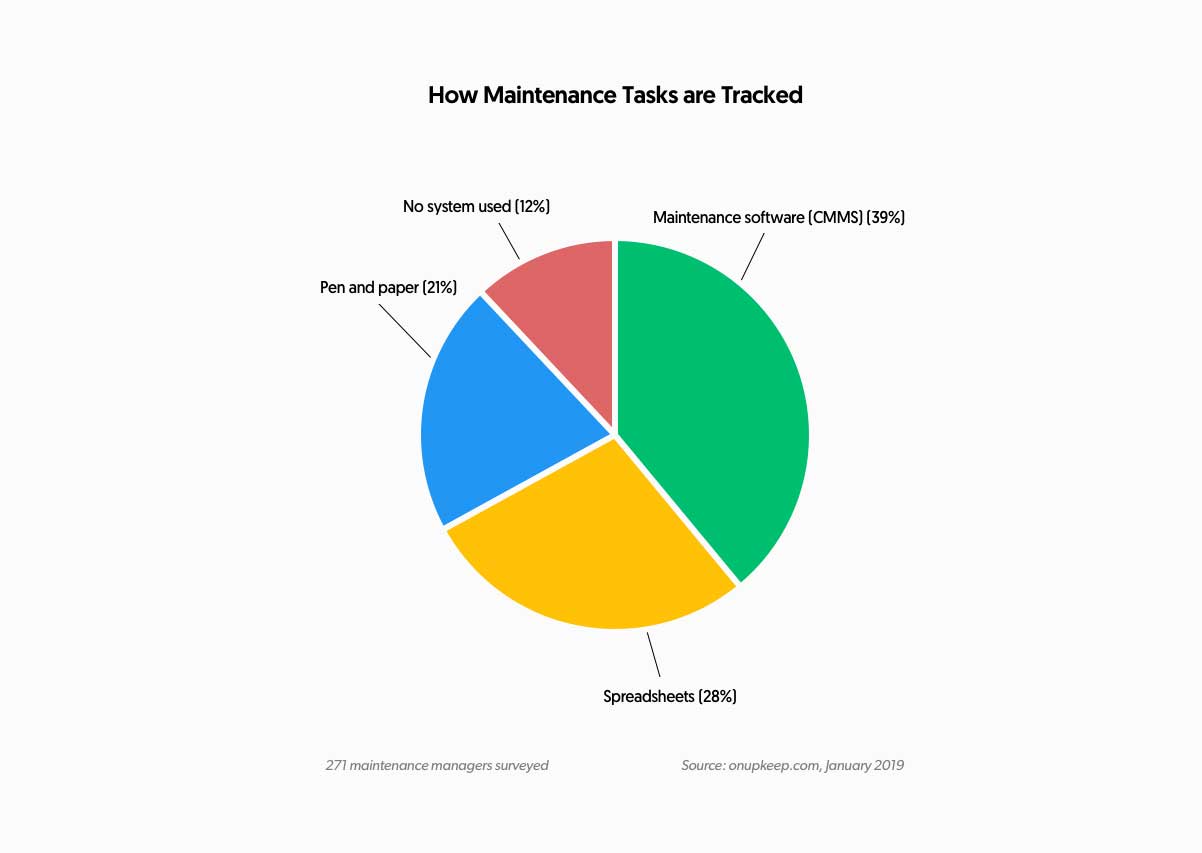
Maintenance management software can be challenging to set up and start using. That’s why the majority of companies still haven’t made the switch.
But the software itself is no longer that expensive. There are a number of upstart SaaS companies in the space. Some start as low as $33 per month.
The problem comes with learning the new system and developing custom APIs to support crucial analytical functionality.
Improve Your Maintenance Program Efficiency With OptimoRoute
Making the switch from spreadsheets to OptimoRoute is an inexpensive and easy way to boost the productivity of your maintenance teams.
1. Maximize the efficiency of your maintenance technicians
With route optimization, manually trying to connect the dots on Google Maps is a thing of the past. Instead, you can import the work orders in bulk.
Just upload your work order sheet, and let OptimoRoute handle the rest.
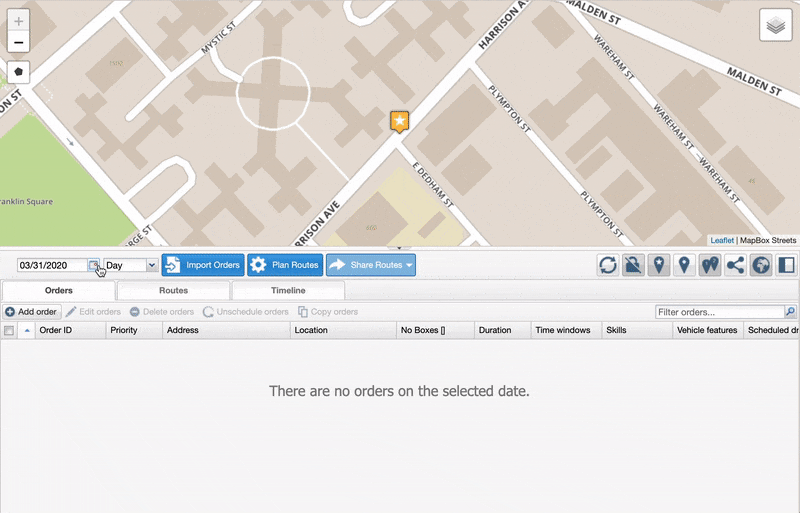
It automatically matches the right technician with the right orders and plans the ideal route for all of their stops.
Southern Star, one of the largest transporters of natural gas in the US, turned to OptimoRoute to empower its maintenance techs.
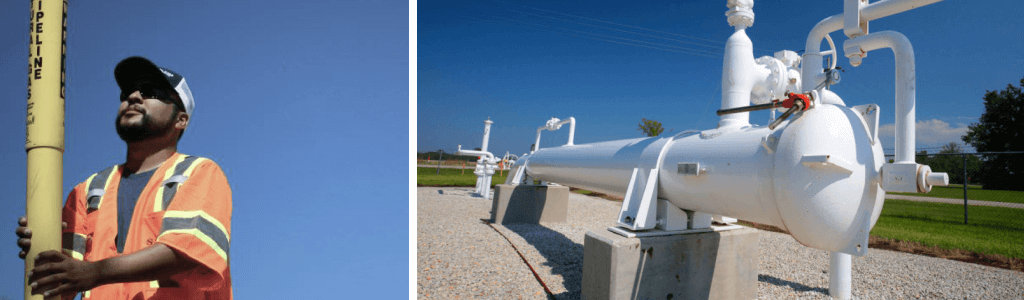
Our powerful features helped it keep and improve on the complex internal workflows. And it saw the benefits quickly.
With faster scheduling and better routes, Southern Star increased its capacity to handle maintenance work orders by 100%. And that’s after completing a nation-wide rollout in just 3 months.
2. Reduce failed maintenance jobs
Leaving maintenance scheduling to a machine may seem like a bad idea. But OptimoRoute has been specifically designed to handle complex real-life variables.
For example, finding the right tech with the right qualifications and tools for the specific work order.
You can set experience, tools, qualifications, and more at the technician level, and OptimoRoute will adjust accordingly. It also accounts for time windows, deadlines, task priority, and more when creating routes and schedules.
But don’t worry, our software won’t go I, Robot on you. Your managers are in full control and can manually confirm and edit every plan. It’s just a lot faster.
3. Boost customer satisfaction and reduce missed appointments
Nothing is worse for a field service company than a missed service appointment. If a customer’s not present, or busy, you need to reschedule.
It’s a nightmare.
Accurate live ETA’s with text messages or email notification of customers is the perfect solution.
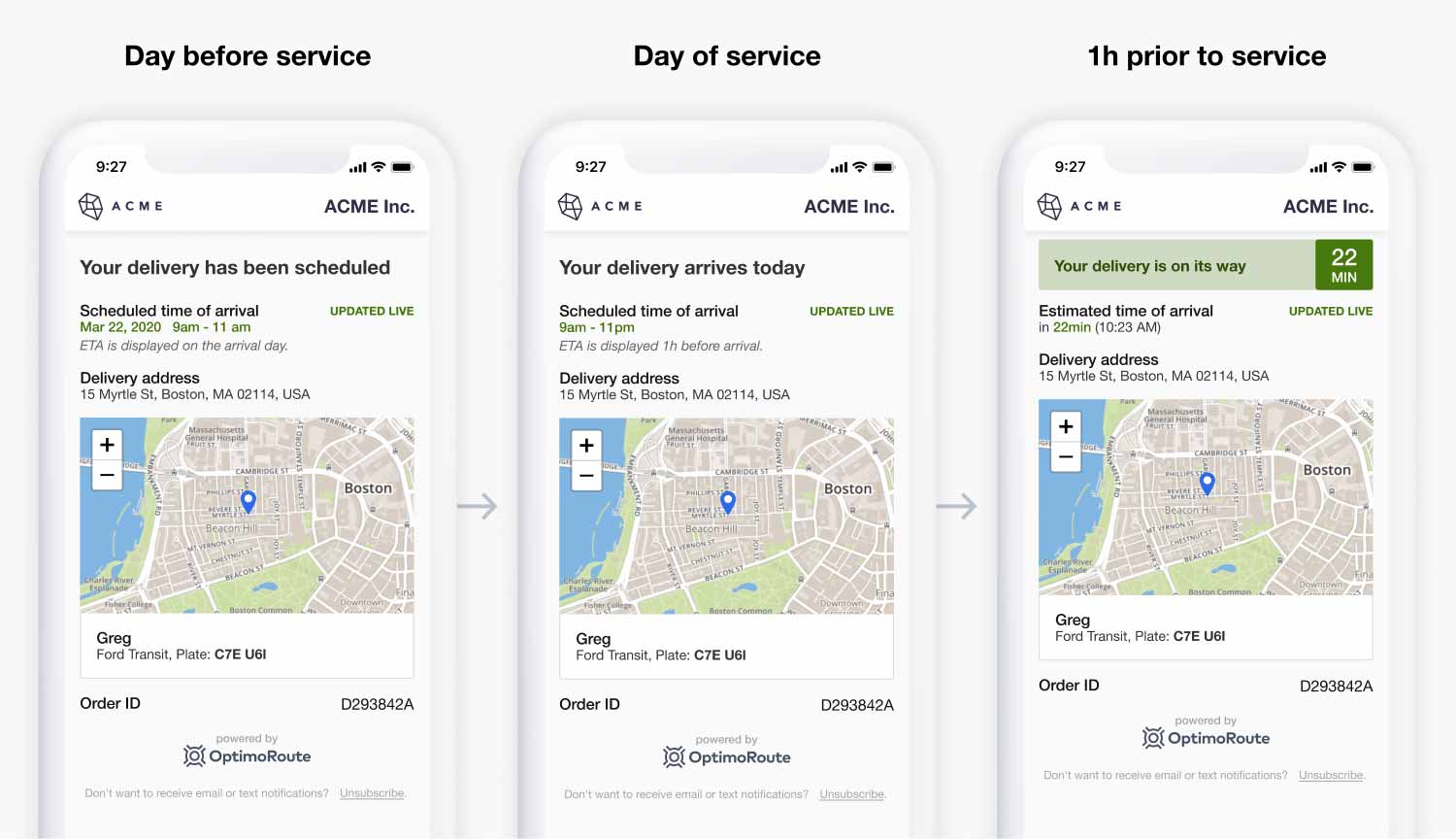
Conclusion
Improving your maintenance program by implementing a complex strategy may seem like a challenge.
But you don’t need to overcomplicate things and invest thousands of dollars in expensive CMMS solutions.
Instead, you can use OptimoRoute to both schedule and distribute work orders and plan the routes for each assignment at the same time.
Start your 30-day free trial today and use OptimoRoute to manage your maintenance teams more efficiently.
Try OptimoRoute™ for Free
No installation or credit card required