Shift Work Scheduling: How To Schedule Shifts Like a Pro
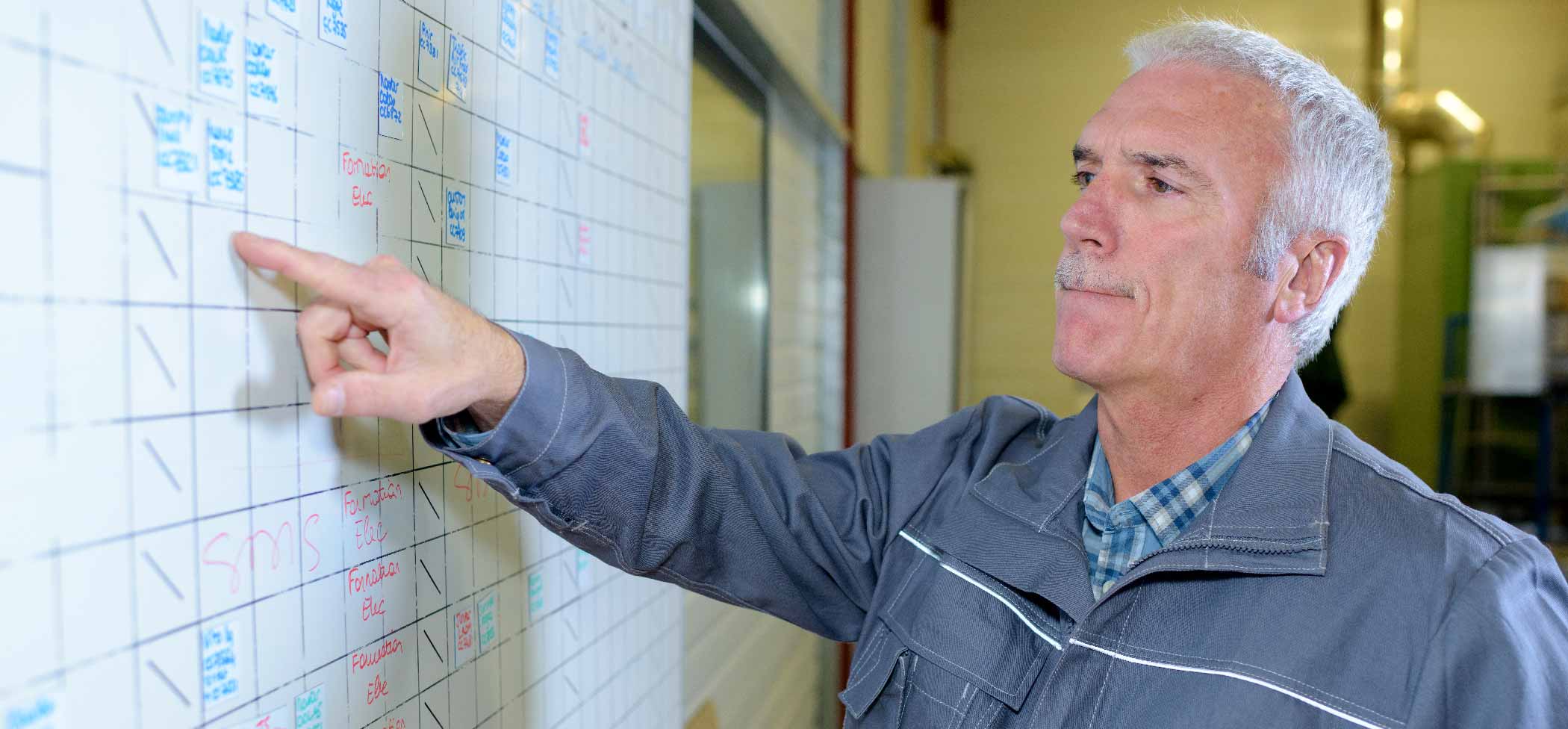
More and more businesses are facing the challenge of staying open 24 hours a day.
Of course, human limitations (as well as legal regulations) make scheduling your team’s shifts across a 24-hour period a challenge. You need to make sure your team is able to stay alert and effective while minimizing the number of necessary workers.
Manually scheduling shifts and trying to keep track of each worker’s productivity is a giant operational hurdle—especially in industries where time blocks aren’t your only concern.
In this guide, we’ll explore common schedules and how you can start optimizing shift work scheduling to boost productivity at your company without needing to expand your management team.
To navigate to the section which interests you the most, click the links below:
- What Is a Shift Work Schedule?
- Fundamental Components of Shift Work Schedule
- What Is the Best Shift Work Schedule?
- Unique Challenges: Scheduling Shifts for Transportation and Field Services
- Plan Schedules for Transportation and Field Service Businesses With OptimoRoute
- Which Companies Use Shifts?
What Is a Shift Work Schedule?
A shift work schedule is a schedule for employees to work in timed blocks throughout specified days of the workweek. Shift work scheduling is a type of forward scheduling that was created to keep a member of a team available whenever a job needs to be done, 24/7.
For example, in a rotating shift schedule, one group of workers handles the day shift while another handles night shifts.
Fundamental Components of Shift Work Schedules
There are 5 fundamental components of a shift work schedule:
- Shift length
- Schedule format
- On-off work pattern
- Overtime
- Scheduling policies
1. Shift length
Shift length is the period of time in each shift. Some shift workers prefer to work longer shifts in order to have more time off and a better work-life balance. 12-hour shifts are a great alternative to 8-hour shifts for this purpose, and they are a great option for many 24-hour operations. However, there are some things you need to think about before you switch to 12-hour shifts, like health and safety concerns, employee morale, production levels, and overtime.
2. Schedule format
Schedule format is how employee shifts are combined into a schedule. The two most common schedule formats are rotating shifts and fixed shifts.
Rotating shifts are when the schedule rotates through a number of different shift patterns. This type of schedule is common in industries where the work volume changes throughout the day.
Fixed shifts are when employees work the same shift pattern every workday. This type of schedule is common in industries with a set amount of work to complete each day.
3. On-off work pattern (aka call in/call out)
On-off work pattern refers to the number of days an employee is scheduled to work, followed by the number of days they are off. This pattern is also called a cycle. There are three types of on-off work patterns:
Weekends off – Employee works Monday to Friday and has the weekends off.
Consecutive days off – Employee has days off during the week
Consecutive days worked – Employee has a day off after working for a certain number of days
4. Overtime
Overtime is when an employee works more than their regular number of hours. Overtime can be voluntary or mandatory.
Voluntary overtime is when an employee chooses to work overtime. This type of overtime is common in industries where employees are paid a premium for working overtime.
Mandatory overtime is when a full-time employee is required to work more than their regular hours. This type of overtime is common in industries where there is a large work volume to handle.
When used properly, overtime can be a great way to meet increased workload demands, while minimizing the need for staffing changes and maximizing employee compensations. However, overtime should be used with caution because it can lead to higher rates of absenteeism, lower productivity, and higher turn-overs, which is something you want to avoid at all costs.
5. Scheduling policies
Scheduling policies are the rules that govern how employees are scheduled and how schedule changes are made.
These policies can include things like overtime limits, call-in procedures, maximum consecutive work hours, and pay policies.
Having proper documentation for your scheduling policies can help you avoid unnecessary conflicts between employees, managers, and the company as a whole. These policies should be created to help your business meet its safety and productivity needs while helping employees meet their scheduling, work-life balance, and personal needs.
What Is the Best Shift Work Schedule?
The best shift work schedule depends on your industry, the number of employees required, regulations, and many other factors.
You can’t just implement a popular type of schedule and hope to improve productivity. It doesn’t work that way.
Different businesses and industries schedule shifts differently, but (for instance) a healthcare worker could do rotational shift work (12-hour shifts):
- 3 Days On—12-hour day shift
- 2 Days Off
- 3 Days On—12-hour night shift
- 2 Days Off
- 3 Days On—12-hour day shift
- 5 Days Off
- 3 Days On—12-hour night shift
- Etc.
Instead of dedicated night shift workers, all staff typically rotate shifts once a week, or once every two weeks with plenty of time off.
To get a complete guide to optimizing your business’ shift work schedule, check out “Schedule Optimization: How to Optimize Schedules for Your Customers & Workers.
The Dupont schedule is a common employee work schedule for manufacturing and maintenance companies:
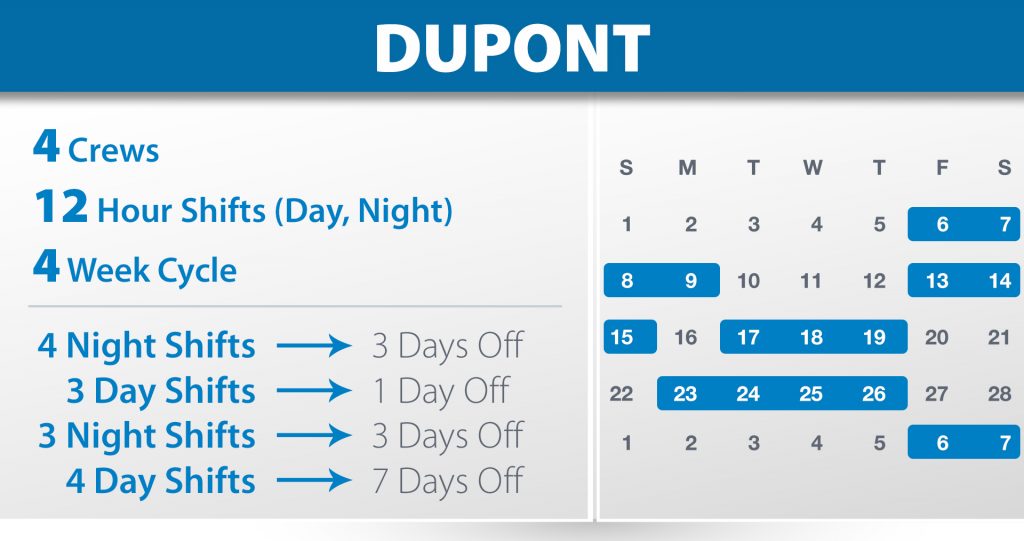
But for industries like transportation and field maintenance, scheduling isn’t as easy as mapping out blocks on a calendar.
You also have to consider industry regulations, estimate driving times, and keep your drivers safe.
Let’s take a closer look at their unique challenges.
Unique Challenges: Scheduling Shifts for Transportation and Field Service Companies
Trucking, delivery, and field service companies with fleets of drivers or technicians face unique challenges when it comes to employee scheduling.
It’s not just about time on duty. Dispatchers must also consider how many deliveries or service calls each driver or technician can make. If not, you risk total chaos.
Let’s take a closer look at one of the largest trucking companies in the US, YRC Freight:
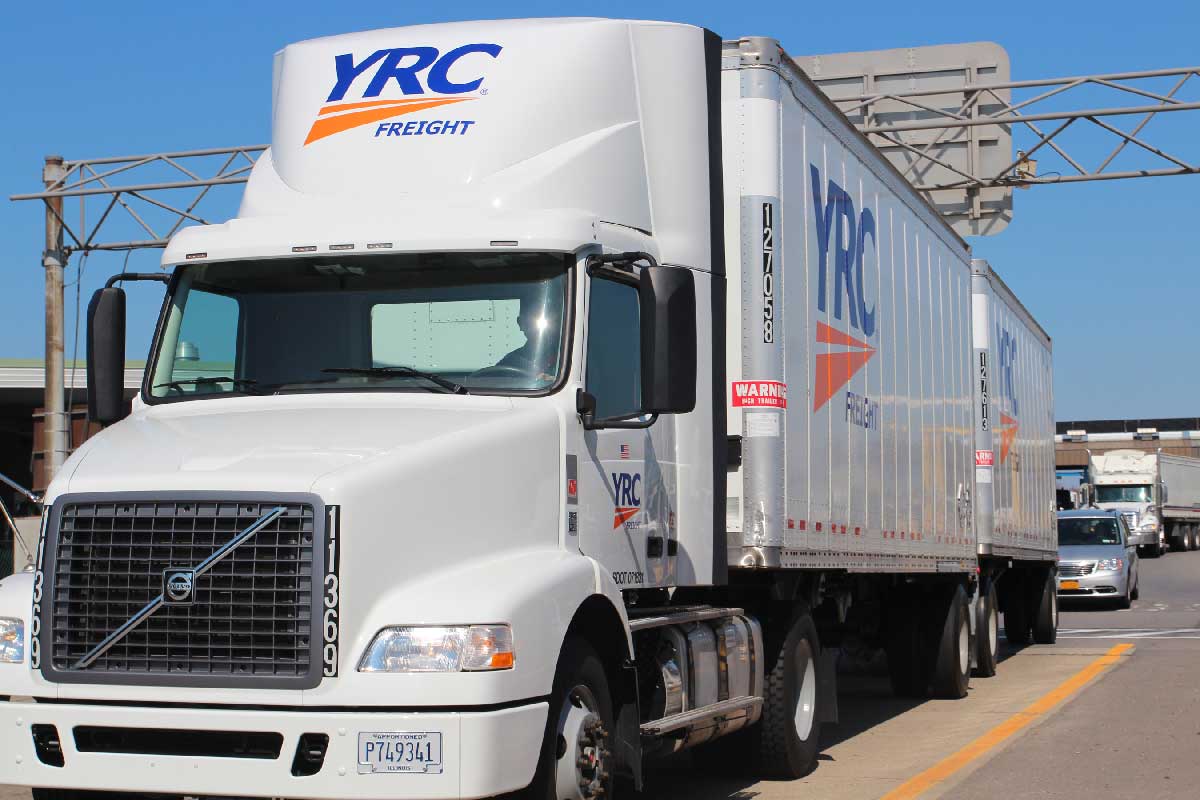
YRC has over 14,000 truck tractors, even more drivers, and over 250 service centers throughout the entire country.
Scheduling efficient shifts isn’t as easy as just mixing and matching. Its dispatchers have to consider long-haul multi-day trips, estimated driving time, mandatory breaks, and much more.
Long-haul routes with mandatory breaks and other regulations
For long-haul trucking, the HOS-regulations mandate at least one 30-minute break for every 8-hour shift on the road.
Truck drivers can spend a maximum of 11 hours driving during a 14-hour window and a max of 60-hours on the road in any 7-day period.
Many carriers still struggle to follow these rules, with hours-of-service violations making up 37.2% of all violations found by the CVSA in 2019.
YRC also has to remain compliant with their government clients like the DHS, and follow CPTAP security protocol.
Accurately forecasting driving times and making deliveries on time
To ensure on-time deliveries, YRC freight’s managers and dispatchers must accurately forecast driving times for multi-state trips and give accurate ETAs to clients.
To try to guess or estimate this manually without the right data is like eyeballing it when building a house—a highly inefficient way to end up with bad results.
Driver safety and productivity
Their managers also have to consider the safety of their drivers, while still keeping productivity high.
That means a delicate workload balance. They have to maximize the usage of each vehicle in the fleet where no driver gets over or underworked.
Plan Better Schedules for Transportation and Field Service Businesses With OptimoRoute
Having a reliable schedule is a necessity for all workers, but the real business impact is bigger for delivery and field service businesses.
If the schedules are off, that means delayed or failed deliveries or missed service appointments.
And there’s nothing consumers hate more than waiting.
According to a 2019 study by Oracle Retail, after a single delayed delivery, 13% of consumers will never do business with a company again.
Unfortunately, when transportation is involved, it’s not as easy as dividing tasks by number and availability.
Multi-dimensional, long-haul routes and schedule planning
Most staff scheduling is one dimensional, meaning it only looks at time and available staff and doesn’t consider other factors that affect a worker’s shift and productivity.
A truly comprehensive work schedule includes more than just basic work hours.
An example for a truck driver would be:
- Long-haul overnight routes: Many drivers complete routes through multiple states and several days. With OptimoRoute you can plan overnight stays, with the previous night’s stop as your starting location the next day.
- Route optimization: finding not just the schedule for your driver, but the most efficient routes to maximize their productivity.
- Accurate ETAs and forecasting to ensure each driver can finish within their shift, and ensure on-time deliveries or appointments.
- Break optimization: is the driver getting breaks at the optimal time and location?
- Docking optimization: does the driver end their shift at an optimal time to dock and reload the truck?
OptimoRoute is designed to consider all real-time factors that impact businesses with fleets of drivers.
Let’s look at it in action.
Plan efficient schedules at scale with our smart software
With OptimoRoute, you can easily plan schedules and routes for hundreds or even thousands of deliveries or work orders at a time.
All you have to do is import your order list.
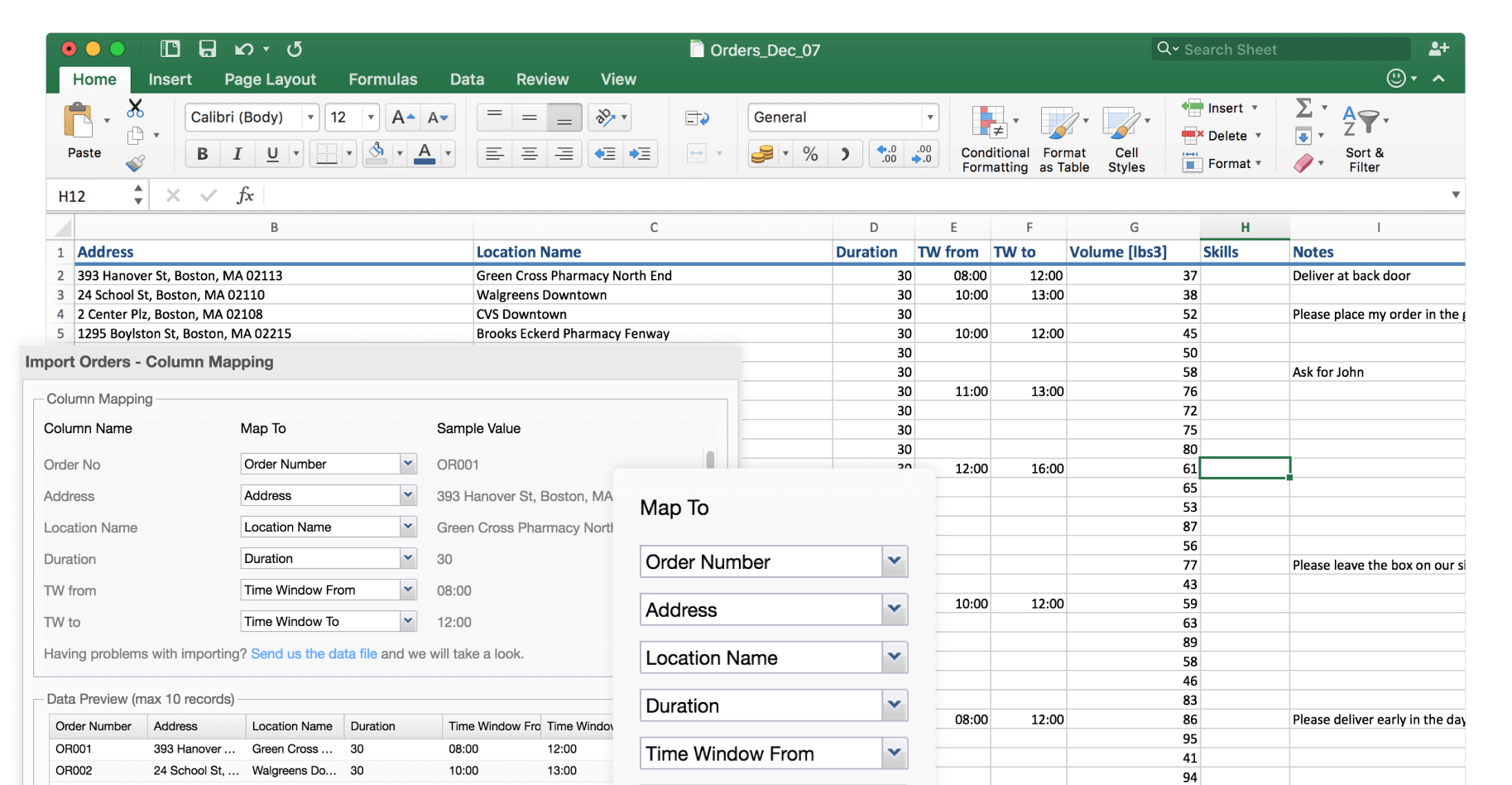
OptimoRoute automatically estimates driving times based on updated traffic data, unloading times (based on number of packages), breaks, and more.
You can then choose how to balance the workload, for example choosing to utilize your entire fleet of drivers.
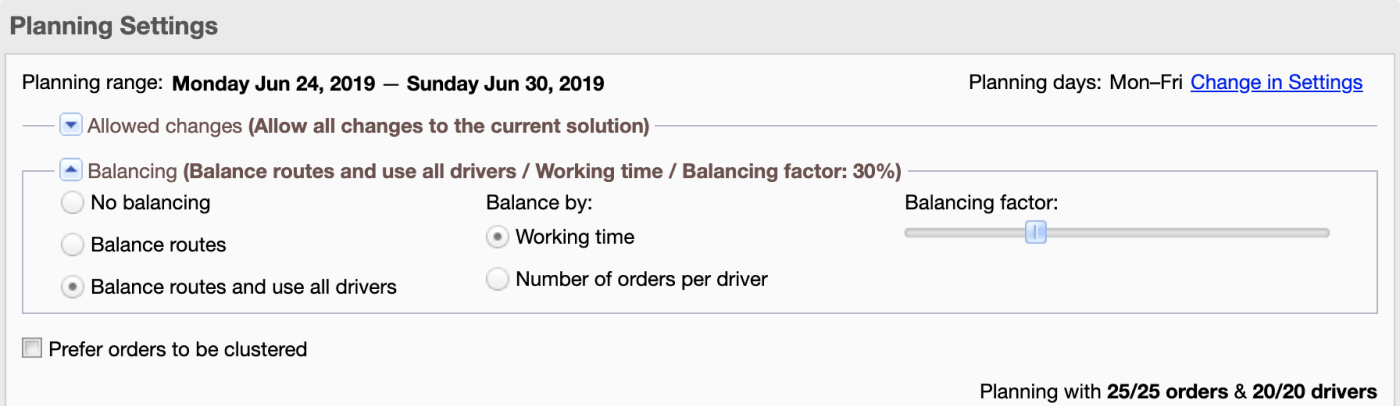
Finally, OptimoRoute automatically distributes the deliveries, and creates efficient schedules and routes respecting the service areas and shifts of each driver.
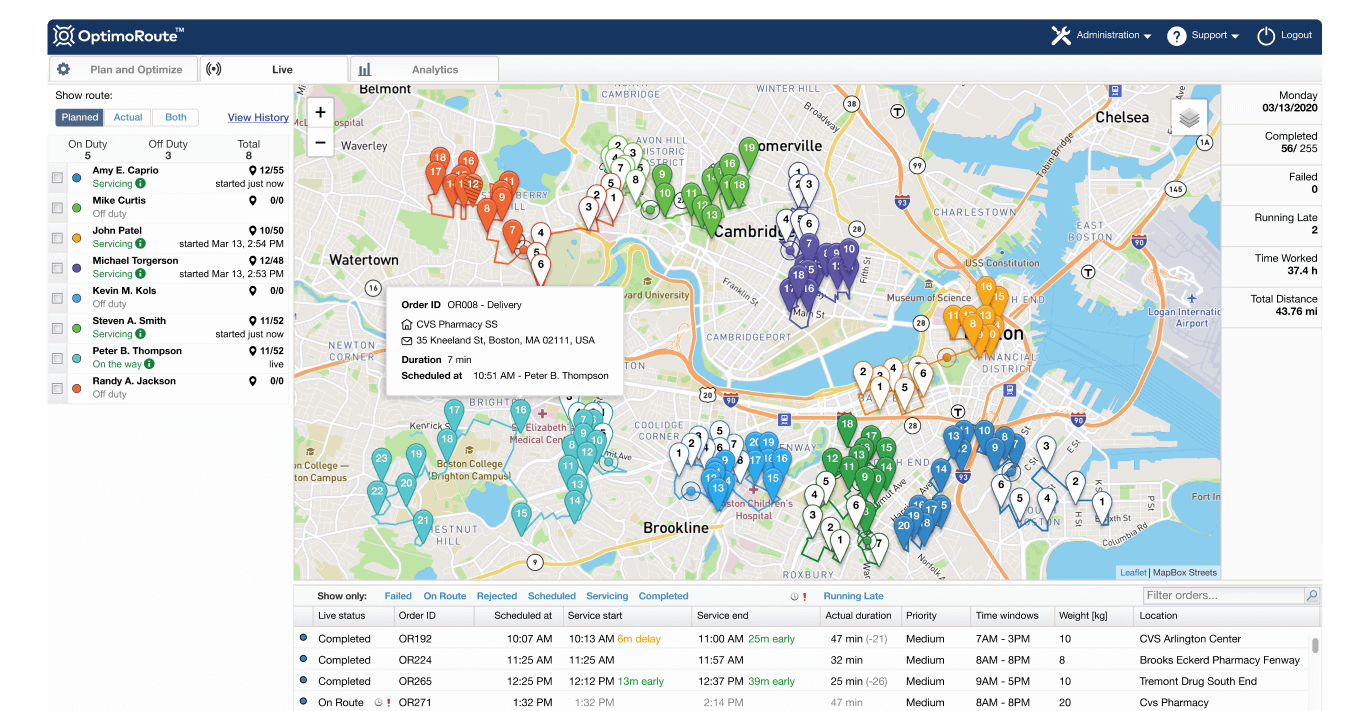
These schedules and routes include mandatory breaks, and uphold all HOS-regulations.
A faster, more productive fleet means happier customers and a healthier bottom line. Plus, more efficient routes will help you cut mileage and labor costs, and improve your on-time delivery rates.
To take our software for a test-drive and create better schedules for your own company, start your 30-day free trial today.
Which Companies Use Shift Scheduling?
But what companies rely on shift scheduling to function?
Manufacturing plants introduced shift work because it was more cost-effective to keep furnaces hot and running 24 hours a day.
These days, companies in a variety of industries have to stay open 24/7 to remain competitive in their market.
Hospitality
Most hotels and motels use shift work scheduling for receptionists. Making sure there’s always someone in the lobby ready to welcome new guests.
Delivery and transportation
Round-the-clock delivery requires drivers to follow fixed shifts to have drivers available 24/7. With added mandatory driving breaks (30-minutes per 8 hours of driving time) long-haul shift scheduling is even more complicated.
Maintenance
With clients needing to keep their operations running smoothly 24/7, maintenance workers also often follow shift schedules.
Medical care and transportation
Medical emergencies don’t care about the clock, so hospitals, emergency clinics, and EMTs need to work 24/7.
Interested in learning how OptimoRoute can improve your company’s schedules and routes? Start your 30-day free trial today.
Try OptimoRoute™ for Free
No installation or credit card required