7 Tips to Improve Maintenance Planning and Scheduling
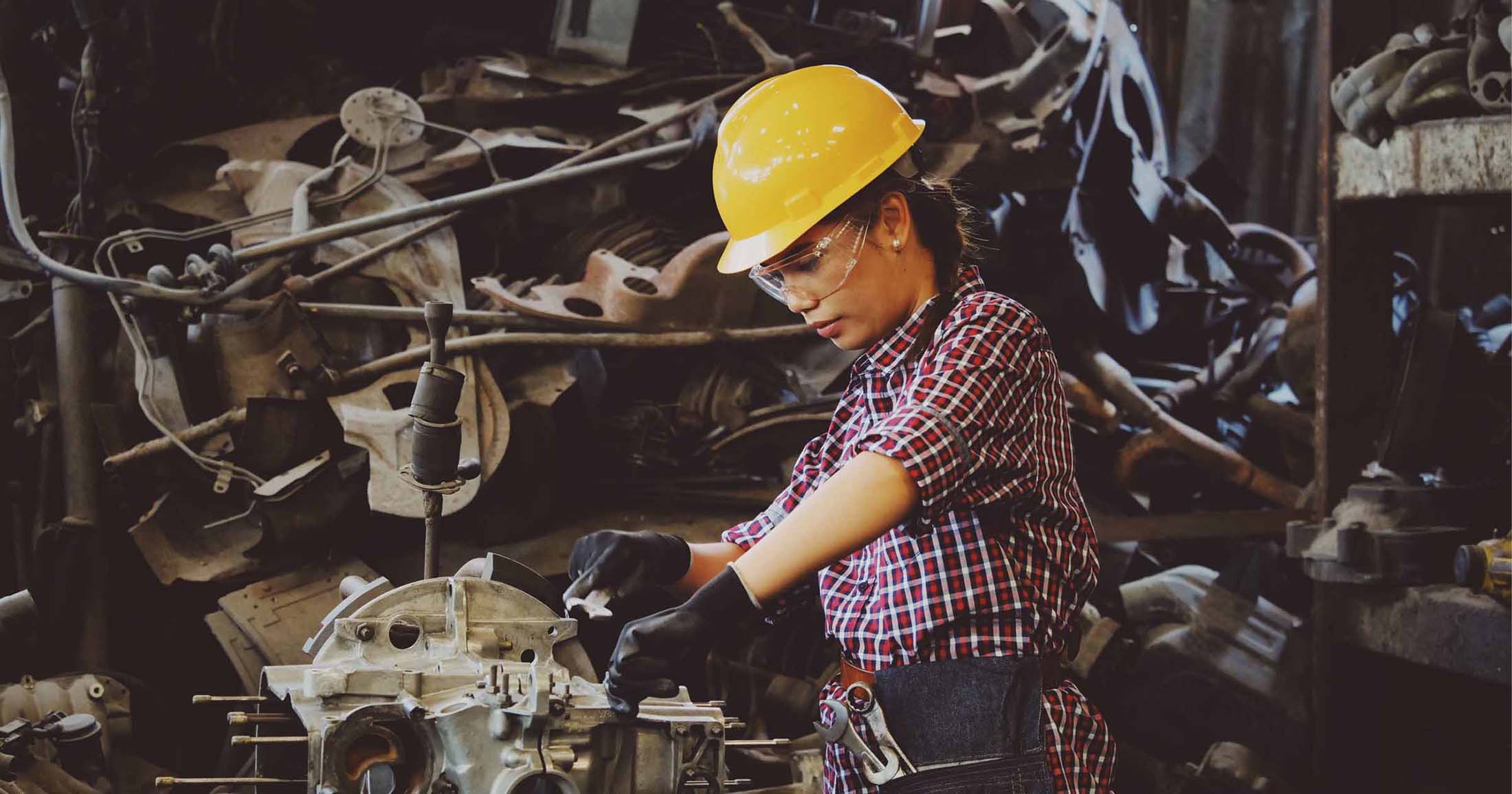
If your truck has ever had mechanical issues at the last minute, it likely ruined your delivery schedule. And if you have to pull a truck from duty, there’s a chance some orders won’t get delivered—which negatively affects your customer satisfaction rating and may lower your revenue.
One way to prevent last-minute mechanical issues from happening or happening again is through effective maintenance planning and scheduling. These tips will help you move from reactive maintenance to proactive maintenance. Plus, we’ll show you how OptimoRoute helps maintenance departments and maintenance supervisors complete more low-priority tasks without adding extra man-hours.
Jump to the section that interests you most:
- 7 Tips for Optimizing and Improving Maintenance Planning and Scheduling
- Automate Planning and Scheduling With OptimoRoute
- FAQs About Maintenance Planning and Scheduling
7 Tips for Optimizing and Improving Maintenance Planning and Scheduling
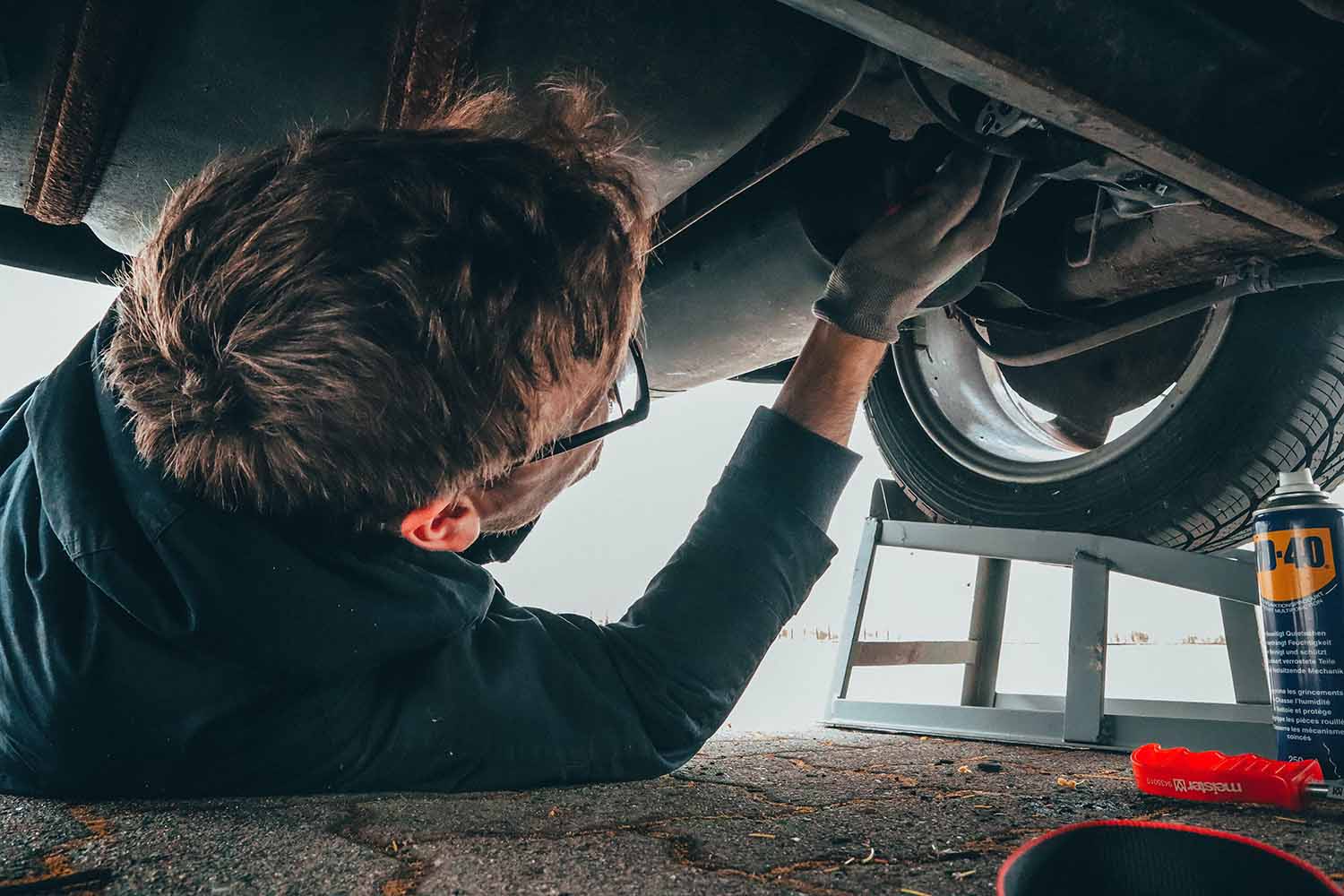
These seven maintenance planning principles and maintenance scheduling tips will help you be proactive and keep your trucks running with minimum downtime.
1. Have a separate job position for planning/scheduling
Don’t overload your fleet manager or delivery manager with the tasks of planning all routes, dealing with delivery delays, and trying to find time for maintenance. If you do, they likely can’t perform at their best and might prioritize routes over proper maintenance, which will lead to mechanical issues.
Rather, create a maintenance management position charged with maintaining the fleet and let your fleet manager worry about hitting delivery goals. Hiring a maintenance manager will reduce the load on your fleet manager and allow all trucks to be routinely checked with higher frequency. Your maintenance manager takes your business from being reactive to truck issues to being preventative—lowering vehicle downtime and saving money.
2. Use a CMMS
A CMMS, or a computerized maintenance management system, tracks the mileage and both the needed and optional upcoming maintenance for each truck in your fleet. In addition, CMMS software tracks vehicle information, logs equipment, performs asset management, and tracks work orders or work requests.
A CMMS software keeps each truck up to date on required preventative maintenance and tracks optional or last-minute maintenance automatically, so these issues don’t get lost in translation on busy days. While this can be done using wipe boards or spreadsheets, you should use maintenance organization software because it can track this information in greater detail by VIN number—increasing accuracy and leaving a detailed trail after maintenance is completed.
3. Base time estimates on data from previous jobs
Track maintenance metrics and key performance indicators (KPIs) over time to help your team better estimate how long a truck will be out of commission and strive for continuous improvement. Your maintenance scheduling will become more accurate as you complete more jobs, allowing for better backlog management. In addition, you’ll be able to see potential avenues for process improvement and become more efficient.
4. Prioritize tasks and projects
Prioritize preventive maintenance over delivery routes to prevent long-term delays with major repair jobs. Give priority to routine maintenance to prevent bigger (and long-lasting) issues down the road.
If you don’t prioritize important maintenance over deliveries, you could end up with a breakdown that will cost you days of preventable and costly shutdown per truck. According to MicroMain, a maintenance planner and software solution, preventative maintenance can save companies money due to reduced downtime, increased efficiency, reduced risk of costly reactive repairs, increased equipment lifespans, and better customer service.
5. Plan weeks ahead
Plan your order delivery schedule and maintenance schedule weeks in advance to see potential delays or time conflicts, something called planned maintenance. Look for slow times when you can pull in your trucks for routine maintenance and ensure you’ll have enough trucks on the road. Planned maintenance saves money and time by giving you the ability to plan around busy or slow times.
Adding a routing and delivery software solution like OptimoRoute to your CMMS can allow for perfect visibility between your delivery schedule and maintenance plan. With a tool like OptimoRoute, you can see what your fleet’s schedule will look like weeks in advance, allowing you to plan which trucks to take offline and what maintenance to schedule.
6. Complete the project plan before planning/scheduling
Before your trucks even pull into the shop for maintenance work, create a plan for what maintenance will be needed and how long each maintenance activity will take to complete. Create a checklist that can be viewed before and when the truck arrives. Make sure to include what items should be pulled out and waiting and what exactly will be done to the vehicle in question.
If you don’t create a solid project plan, you could end up with the wrong maintenance being completed (due to having so many trucks to work on) or delays as your team works to figure out what’s being done. This could end up costing your company more money and time due to extended equipment downtime, slowing down deliveries and leading to longer delays and more revenue lost.
7. Focus on route planning and optimization as a driver of value
Regular maintenance is a required cost as it’s the only way to make sure that your truck doesn’t develop large issues. But, it’s based on miles driven; so, lower the miles driven, to lower costs. Using route optimization you can rest assured that the distances between stops is always optimal.
Planning ahead and optimizing your routes will decrease the cost of operations at your company over time. In addition, using a tool like OptimoRoute, the person creating your routes and schedules, will increase delivery efficiency, leading to higher revenue and customer satisfaction.
Automate Planning and Scheduling With OptimoRoute
You should plan and schedule fleet maintenance in advance because you’ll lower your overall costs and maintain a fleet that’s ready to deliver every order, every day. You could ignore maintenance in favor of doing the minimum or waiting until the last minute, but that’ll lead to potential delays from expensive and time-intensive repairs in the long run.
Make planning your maintenance tasks and coordinating with your maintenance team easier with a CMMS. And lower the need for maintenance by pairing your maintenance program with OptimoRoute. With OptimoRoute, you can see slow periods weeks in advance, giving you time to schedule needed service work. In addition, you can lower miles driven, making required servicing less frequent—increasing revenue and decreasing the time a truck is unavailable.
Simplify your scheduling process and try optimoRoute today, free for 30 days.
FAQs About Maintenance Planning and Scheduling
Get answers to the most popular maintenance planning and scheduling questions.
What are the benefits of maintenance planning and scheduling?
The benefits of maintenance planning and scheduling include a lower chance of a major breakdown, higher fuel efficiency, and the ability to choose the ideal time for a truck to be out of commission.
What tools are useful for maintenance planning and scheduling?
CMMS software solutions, called maintenance management software, can help you track what’s needed for each truck in your fleet. In addition, a routing and scheduling software like OptimoRoute can help you plan your delivery schedule to determine what vehicles are free for maintenance and where they will be should you have multiple locations.
What is the difference between scheduling and planning?
Planning is listing each task, selecting the order for the tasks to be completed, getting a list of items needed to complete those tasks, and accounting for (and getting answers to) questions about the process. Scheduling is setting a time for each task to be completed.
Try OptimoRoute™ for Free
No installation or credit card required