What Is an ERP Inventory Management System? [2024 Software Guide]
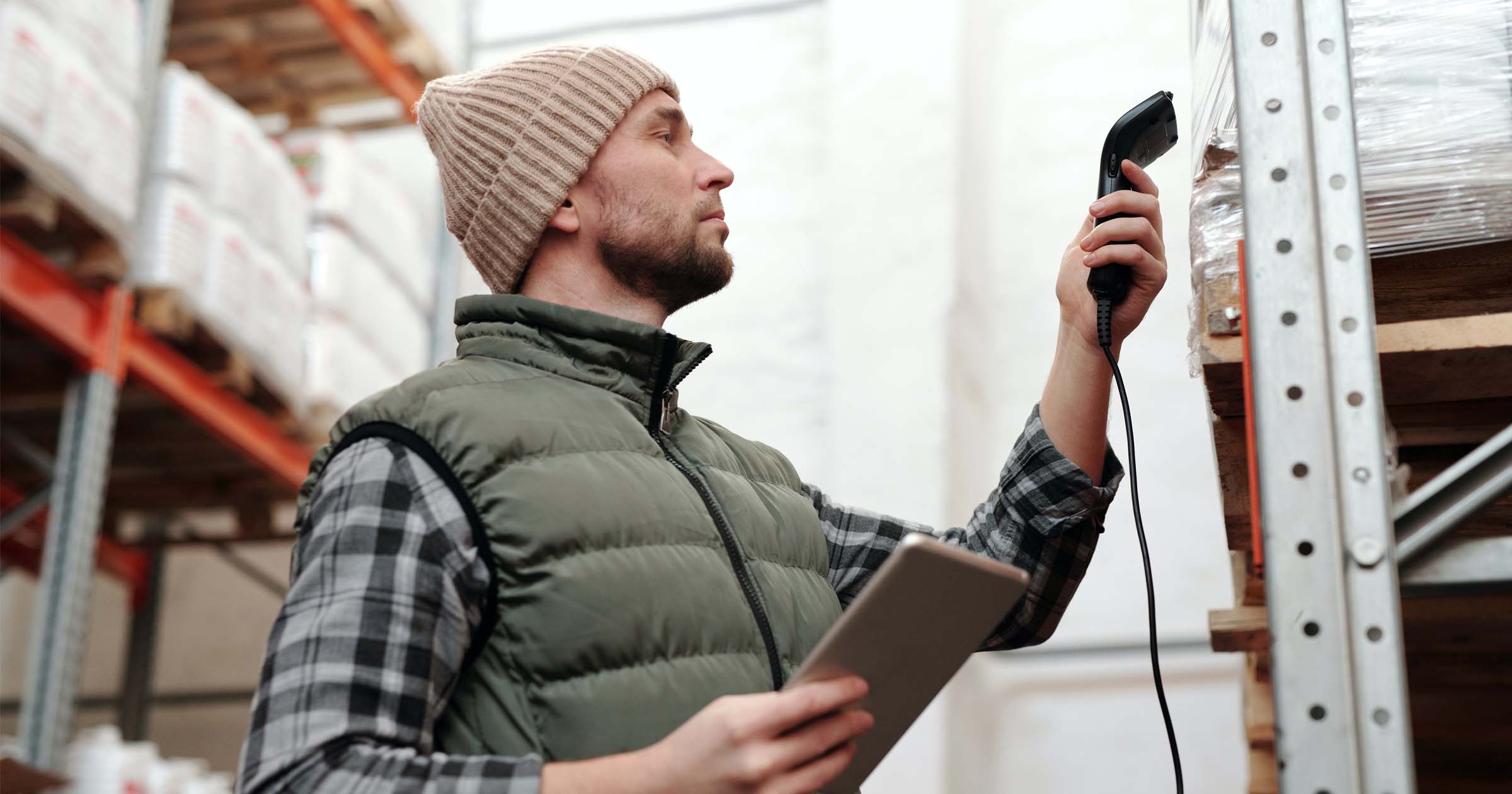
Accurate order fulfillment isn’t enough to set yourself apart from the competition. 41% of customers blame retailers for late deliveries. So, whether your business relies on a third party or an in-house team for delivery, your brand is responsible for making sure customers receive their orders on time. Implementing and optimizing an ERP inventory management solution can help your business optimize inventory levels, boost warehousing efficiency, and improve last mile delivery.
Jump to the section that most interests you:
- What Is ERP Inventory Management?
- How an ERP Inventory Management System Can Benefit Ecommerce Companies
- Things to Look for in ERP Inventory Management Software
- How to Optimize Last Mile Delivery to Make Your ERP System Count
- FAQs About ERP Inventory Management
What Is ERP Inventory Management?
Enterprise resource planning (ERP) refers to the process of integrating and centralizing a variety of key business processes and tools. The goal behind this integration and centralization is to provide a holistic approach to business, where one workflow informs another. For example, organizations that integrate their forecasting and ordering workflows streamline how they maintain inventory levels.
The acronym also describes the types of software that facilitate this process by combining the workflows and tools businesses use to keep operations running. ERP inventory management systems act as a central platform that houses all of the tools businesses need to manage their inventory. Housing all of the tools together in one platform makes everything easier to access, saving managers time.
Some common ERP inventory management system functions include:
- Product tracking
- Barcoding and tagging
- Supply chain management
- Logistics planning
- Reporting
- Inventory forecasting
How an ERP Inventory Management System Can Benefit Ecommerce Companies
There are many benefits of ERP inventory management, including integrating key functions, centralizing data, and helping you scale business operations with ease.
Integrate supply chain and logistics functions
ERP inventory management systems integrate two vital functions: supply chain management and logistics planning. These terms are so closely linked that they’re often used interchangeably. However, they are two distinct practices—and they rely on each other to be effective. Supply chain management describes how businesses oversee the inventory lifecycle, beginning with creating products from raw materials and ending when customers receive their orders. Logistics is the process that coordinates the movement of raw materials, finished products, and information within the supply chain. So, while the two processes might be different, keeping them siloed doesn’t make sense, which makes the centralization and data-sharing capabilities of an ERP vital for retailers.
This integration is particularly important for efficient order fulfillment, which can have a drastic impact on how customers perceive your brand. To complete orders, organizations need to effectively coordinate deliveries. But without information about the supply chain as a whole, the process of coordinating the logistics of last mile delivery is impossible to do accurately. For example, let’s say a customer orders a custom piece of jewelry from an online jeweler. To provide an accurate delivery timeline to the customer, planners need to know details about the entire supply chain. This includes such information as what materials the manufacturer will need to order and how long it will take to create the jewelry.
Access more data and improved analytics
Even small errors in data can have expensive consequences for businesses. For ecommerce companies and retailers, inaccurate data can lead to problems like skewed inventory projections, missed reorder points, and disrupted order fulfillment timelines. Many systems are designed to automatically collect data. This not only saves time by eliminating the need to manually track data but also minimizes the chances of human error in data entry. And because ERP integrates multiple tools, the platform is able to collect data about many different aspects of your business. And the more data you have, the better your business analytics will be, and the more accurately you can forecast your business needs.
Scale easily
As your business grows, so will your customer base, which means higher sales and larger inventories. But more products in your inventory mean more things to keep track of. The larger your inventory grows, the more difficult this becomes, and the more complex your workflows will be. ERP inventory management solutions help make it easier to scale by automating the tasks that become more nuanced and complex as your business grows. For example, the platform can monitor inventory levels and automatically order replenishment stock when product is low.
Things to Look for in ERP Inventory Management Software
There is no one-size-fits-all inventory system for retailers. But there are a few things that all businesses should consider when looking for an ERP inventory management tool. First, a business needs to look for a tool with pricing that won’t exceed the budget. They should also look for a solution with a user-friendly interface that is based in the cloud for greater accessibility. It’s also important to check what support options the software vendor provides to make sure help is available if there’s a problem with the system. A good ERP tool will also automate key functions like inventory management, warehousing, and order management.
Multi-channel inventory management
Multi-channel inventory management is a process that retailers use to account for the sale of inventory that is sold through various outlets and warehoused in different locations. This can include wholesale, ecommerce, and traditional retail. Software with multi-inventory management features will help retailers in a variety of ways, including:
- Saving time by making it easy for managers to get the information they need with centralized data about purchase orders and inventory levels across all sales channels and warehousing locations.
- Enhancing inventory forecasting by using real-time data to determine inventory needs, set reorder points for replenishment, and avoid problems like low stock levels or complete stockouts.
- Improving customer experience by making it easy for customers to shop for products where they prefer, whether that’s on your website or at your brick-and-mortar store.
Warehousing and stock tracking
Multi-channel inventory expands the reach of sales. But retailers won’t meet demand or maximize profits if they can’t find the products they need to fill orders. This makes efficient warehousing practices vital for all organizations, whether it’s a small business with one storage center or a large corporation with multiple warehouses. An ERP equipped with a warehouse management system helps retailers avoid problems like delayed order fulfillment or missing product by streamlining processes:
- Warehouse design optimizes retailers’ storage by guiding warehouse managers on how to organize inventory and store popular products in easy-to-access areas, making it easier to fill orders.
- Picking and packing streamline the process of finding products within the warehouse and packaging them for shipment and delivery.
- Receiving and putaway facilitate the process of receiving new shipments of inventory and properly storing products in the correct place within the warehouse.
Invoice and purchase order management
Effective purchase order management begins when a customer identifies the item they want to buy and ends when the final invoice is paid. A robust ERP system with invoicing functions and point of sale (POS) integration can streamline this process by automatically generating invoices and sending them to customers when they place an order. By integrating invoicing with order management, the ERP can automatically update to signal the warehouse team to begin filling the order.
How to Optimize Last Mile Delivery to Make Your ERP System Count
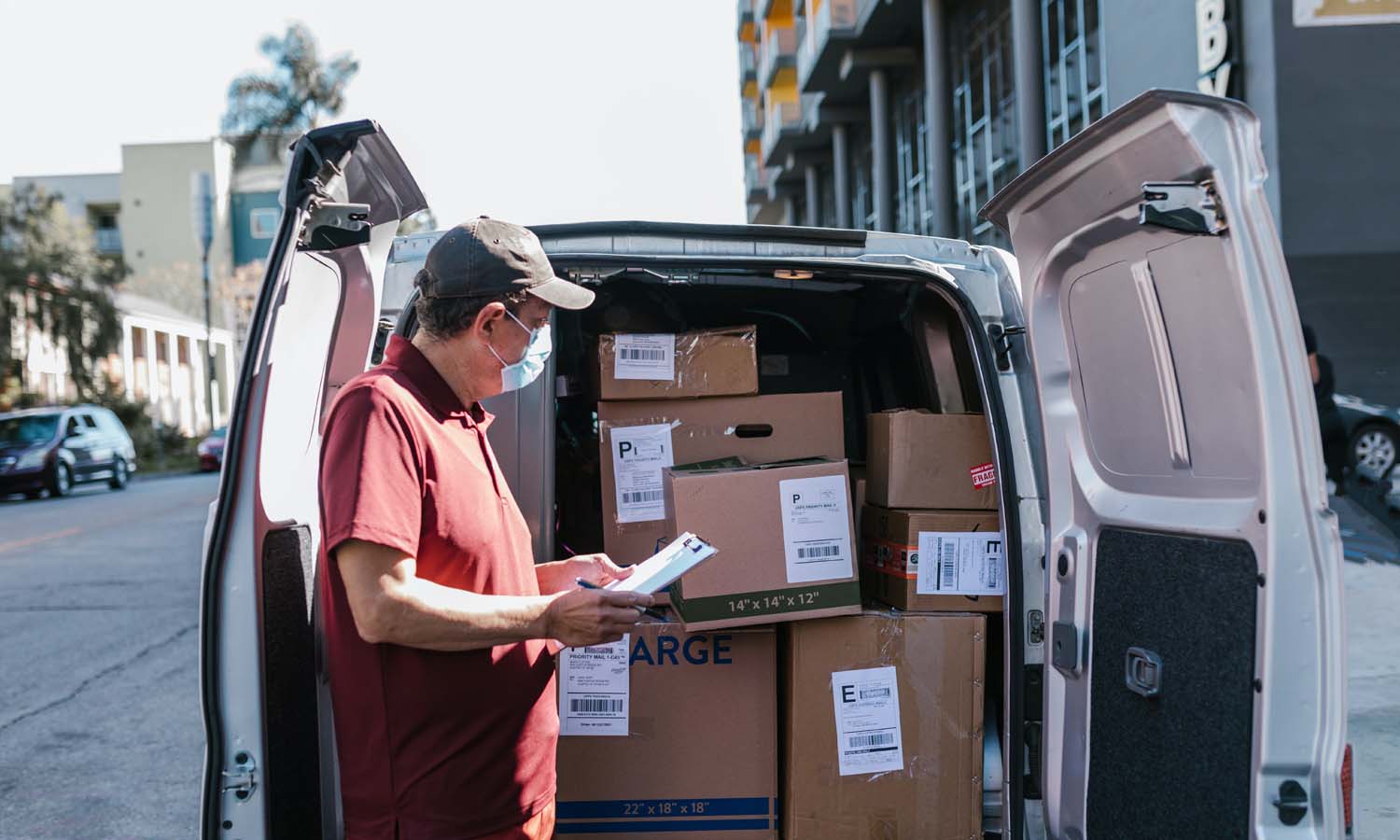
Good inventory management begins with the proper inventory levels and continues until products arrive in customers’ hands. This requires leaders to manage a variety of processes, from the shipment of raw materials to the organization of inventory in the warehouse. Implementing an ERP inventory management system helps streamline these workflows and provides retailers with data insights that improve processes like last mile delivery.
Once you’ve implemented an inventory system, the software will automatically track and store data about all of your business processes. This includes data that can help improve your last mile delivery routes, such as what packages are being shipped and where they need to be delivered. Integrating your ERP with a last mile delivery software like OptimoRoute allows you to automatically generate optimized routes for your delivery team with just a few clicks.
After integration, you can easily import order and delivery details from the ERP to OptimoRoute. Then you can detail specific parameters for the routes, including defining service areas, outlining delivery windows, and setting rules for breaks. Then OptimoRoute can automatically generate delivery routes maintaining all parameters for all drivers and orders at once, saving managers time and boosting efficiency.
Try OptimoRoute free for 30 days to see how it can help improve how you serve your customers.
FAQs About ERP Inventory Management
In this section, we’ll answer three of the most commonly asked questions about ERP inventory management.
What is the difference between ERP and inventory management?
ERP is a broad term that encompasses how organizations integrate a variety of workflows and processes. Inventory management refers to the processes an organization uses for managing inventory, including product tracking, tagging, and forecasting. ERP can apply specifically to inventory management or to other business activities.
How can ERP software help with inventory management?
ERP software centralizes the tools that businesses use to facilitate various inventory tasks. This improves efficiency and saves managers time by making it easier for them to find the tools they need. For example, forecasting helps retailers avoid inventory problems like shortages and stockouts. Meanwhile, warehousing and inventory features help retailers reduce lead times.
What’s an ERP system example?
A few common ERP solutions include Oracle NetSuite, Sage, and QuickBooks Commerce.
Try OptimoRoute™ for Free
No installation or credit card required