Transportation Costs for Businesses: The Breakdown
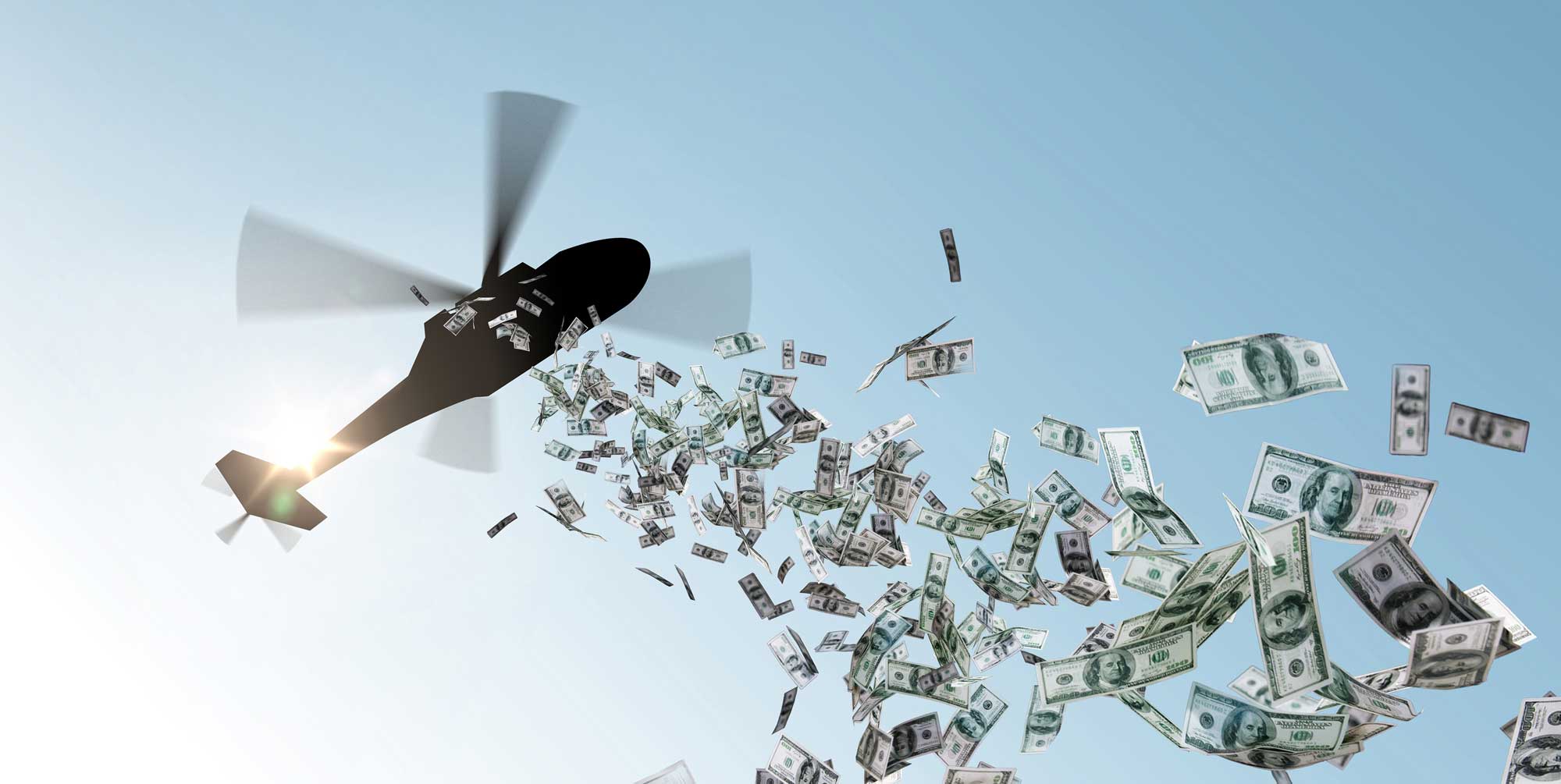
Transportation and shipping are by far the most expensive part of logistics.
Transportation alone costs US businesses over $1.04 trillion (or 10.4% of total revenue), according to the 2019 Annual State of Logistics report.
But what is it exactly that makes transportation such a significant cost center? And what can you do to tackle this problem?
In this guide, we’ll take a closer look at transportation costs, why it costs businesses so much, and how you can reduce these costs.
Let’s dive right in.
To navigate to the section which interests you the most, click below:
- What Are Transportation Costs?
- What Are Examples of Transportation Costs?
- What Affects Transportation Costs?
- Planning, Dispatching, and Routing: The Hidden Transportation Cost
- How Do I Lower My Transportation Costs?
What Are Transportation Costs?
Transportation costs are all the expenses related to the transportation of raw materials, finished products, and employees. It’s the money behind making sure all moving parts get where they need to be so your customers get their product or service on time.
Which area costs your business the most depends from industry to industry. For a distribution company, it’ll eat up the majority of your revenue. A software company may only transport a few field sales reps.
Let’s take a closer look at some examples of transportation costs for different companies.
What Are Examples of Transportation Costs?
There are many different types of transportation that add up to the total cost of one-tenth of your revenue or more (see our guide to transportation terms if there are any terms you don’t recognize).
Freight: Large scale transportation of goods and products.
When most people think of transportation, freight is the first thing they think of. Large containers filled with your company’s products shipped via cargo ships, freight trains, or FTL trucks.
In freight, the basic costs you’ll get billed for include these four items:
- Line haul
- Pickup and delivery
- Terminal handling
- Billing and collecting
Depending on the arrangement, you may also have to pay for your own insurance.
It’s important to deliberately choose your carriers, and build relationships to get special deals over the long term.
Your logistics costs will be a big part of your operating costs and impact your profitability.
Last mile delivery: Getting an order to the customer’s door
Last mile delivery is the process of delivering an order to the customer’s door. Since more and more shopping happens online, this is becoming a bigger and bigger cost center for businesses.
According to Statista, delivering a single order costs $10.1, on average. If you want to offer free delivery (to compete with Amazon and other major retailers), that means you need a profit of at least $10.2 per order.
It’s a huge challenge to implement at scale, which is what often makes it the most expensive part of the supply chain.
If you outsource it to third-party services, funded shippers like USPS typically have cheaper pricing.
Business trips: Transporting employees for sales meetings
The average business trip costs companies $1,293, according to Runzheimer. Even with limited sales staff, these costs can really add up.
These are all economies of scale, so if you’re a smaller business, you’re probably going to be paying significantly more. That means a larger percentage of your revenue and profits will get eaten up.
In industries where field sales is common practice, this can cost your business tens of thousands of dollars per year per employee.
Field service or house calls
Does your business offer house calls or field service? Getting your technicians to the customer can be a large business expense.
Mileage and fuel usage will affect these costs, as well as local fuel prices and tolls. These vary depending on the state, county, or countries. In the United States, gas prices vary from $1.82 to $3.32 per gallon, depending on the state, according to AAA. So good refuel timing is essential.
If you support commuting workers, whether or not they use public transportation will also make a big difference.
Maintenance and depreciation of fleet assets
If your company has a privately-owned fleet, this is the last category of transportation costs.
It doesn’t just apply to trucking companies. Plumbing businesses and other contractors with branded vans are also affected. Fixing broken down vehicles and routine maintenance is expensive.
Plus, no matter how well you maintain your vehicles, they will depreciate in value.
The overall cost of transportation depends on your entire transportation infrastructure.
Let’s take a look at some of the factors that impact the prices at a more granular level.
What Affects Transportation Costs?
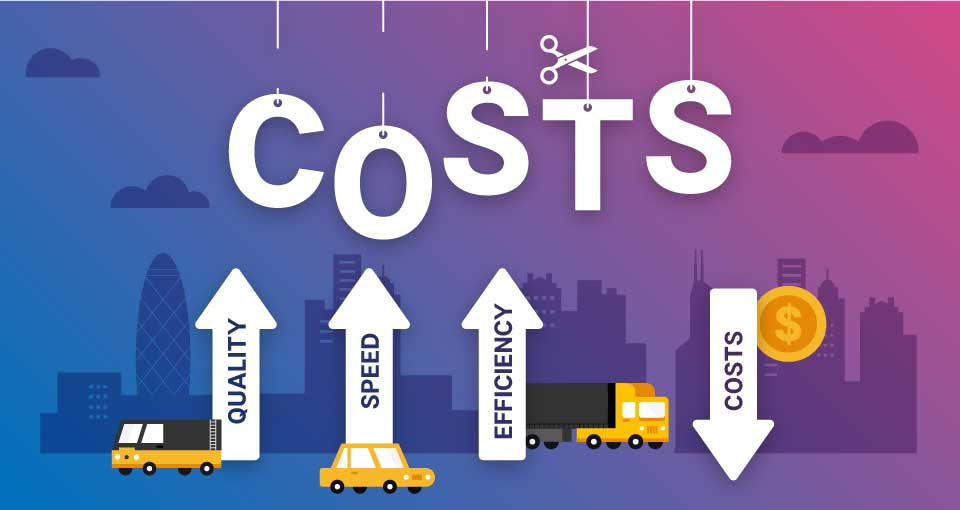
When a shipper offers you a quote, there are many factors that impact the final price. For Instance, are you transporting goods using maritime transportation, or transporting freight by air?
Certain types of transportation have high costs, while others are more affordable.
Distance
How far are you transporting the package? Long distance shipping is obviously more expensive than sending something to a neighboring city.
Package size
Learn more about how to optimize this area in our guide to reducing packaging costs.
Urgency
Another huge factor that impacts the price is urgency. For example, sea freight with a deadline of 6 months or more is a lot cheaper than a rush job using the exact same pathway.
Shipping accuracy
Failed deliveries mean your delivery drivers have to go out of their way to make the delivery a second time. That’s why shipping accuracy is so important.
Handling
Are you shipping sensitive goods that need to be handled with special care and attention? That will cost extra.
Domestic or international?
International trade and shipping include extra fixed costs in tariffs and taxes. Domestic shipping typically only includes VAT for the actual transport services.
Planning, Dispatching, and Routing: The Hidden Transportation Cost
When you first start handling deliveries for your business, doing things manually isn’t a problem. With only a few calls per day, it’s easy to just open Google maps and give your drivers orders.
But this changes as your business grows.
At scale, doing things manually or with an inefficient system can lead to:
- Needing to hire extra dispatchers and operations managers to plan and manage your fleet of drivers.
- Planning inefficient routes and schedules that increase fuel and driver costs.
- Slowing down deliveries (costing you customer loyalty and future purchases).
It’s impossible to scale good decision-making without the right system in place.
How Do I Lower My Transportation Costs?
Thankfully, you don’t have to sit back and accept your high transportation costs. You can take steps to reduce them.
Find the best carrier deals for freight and personnel transportation
Do you rely on third-party transportation? For freight, use a transportation management system to identify the best carrier deals for every shipment in real time. It’s a simple change that can save you tens of thousands of dollars per year.
For personnel, try to focus on one or a few carriers and negotiate a special deal for all your employees. Again, the potential savings are huge.
Plan more efficient routes to reduce fuel costs and driver costs
If you handle shipments in-house, the most impactful thing you can do is to improve your routes. With less time on the road, you’ll save big on fuel, and reduce driver and overtime costs.
Route optimization software like OptimoRoute can make your life a lot easier. What sets OptimoRoute apart is its ability to quickly plan complex routes at scale, accounting for all real-world variables, and also adjust the routes on the go.
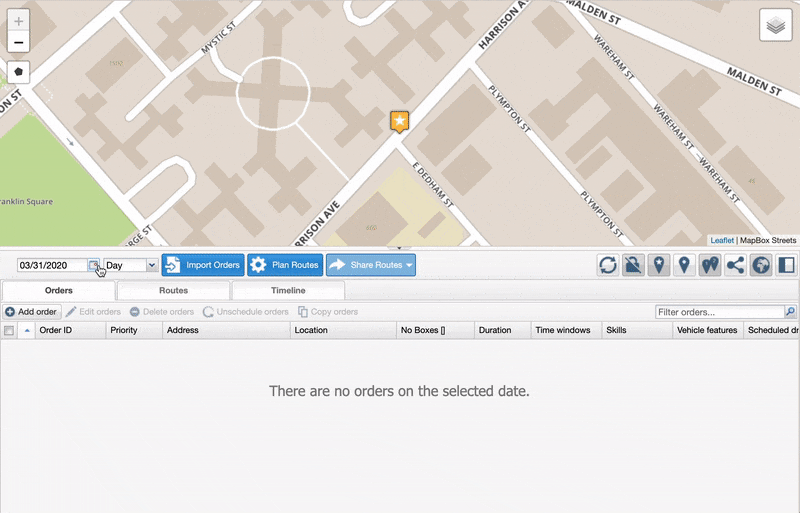
Using our software helped Biomed Care Services reduce the size of its fleet, save fuel on deliveries, and save £3,000 on delivery costs every single month.
Planning was sped up from days of draining manual planning, to just a few minutes of adjustments. Combined with the better routes, that made it possible to handle 25% more orders with a smaller fleet.
Maximize vehicle utilization and fleet efficiency
Whenever a vehicle or driver is sitting idle, they’re only costing your company money. By improving utilization, you may be able to reduce your fleet size and keep all deliveries on time.
With OptimoRoute’s planning and Analytics features, Biomed was able to reduce its fleet by 33%, while increasing its delivery capacity.
Minimize failed deliveries with Realtime Order Tracking
Any failed delivery adds extra delivery costs and ruins your relationship with your customer.
Use OptimoRoute’s Realtime Order Tracking system with text message notifications to avoid confusion.
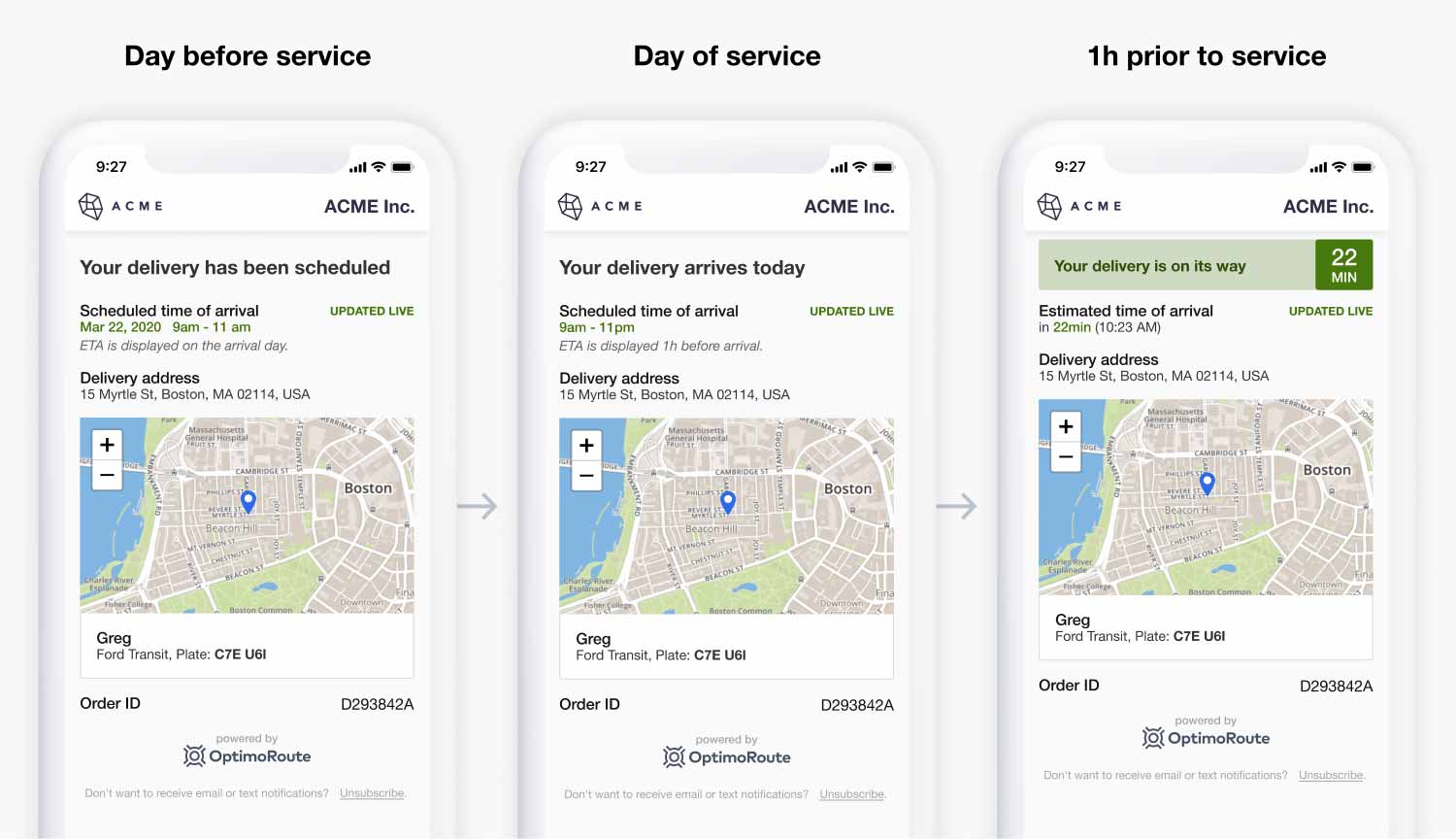
Reduce human errors with a driver app
A single typo (which is easy enough even on computers) can mean hours of drive time or additional miles traveled and shattered schedules.
Eliminate the chance of your dispatchers accidentally miss typing an address and send exact delivery locations to drivers with the OptimoRoute Mobile App.
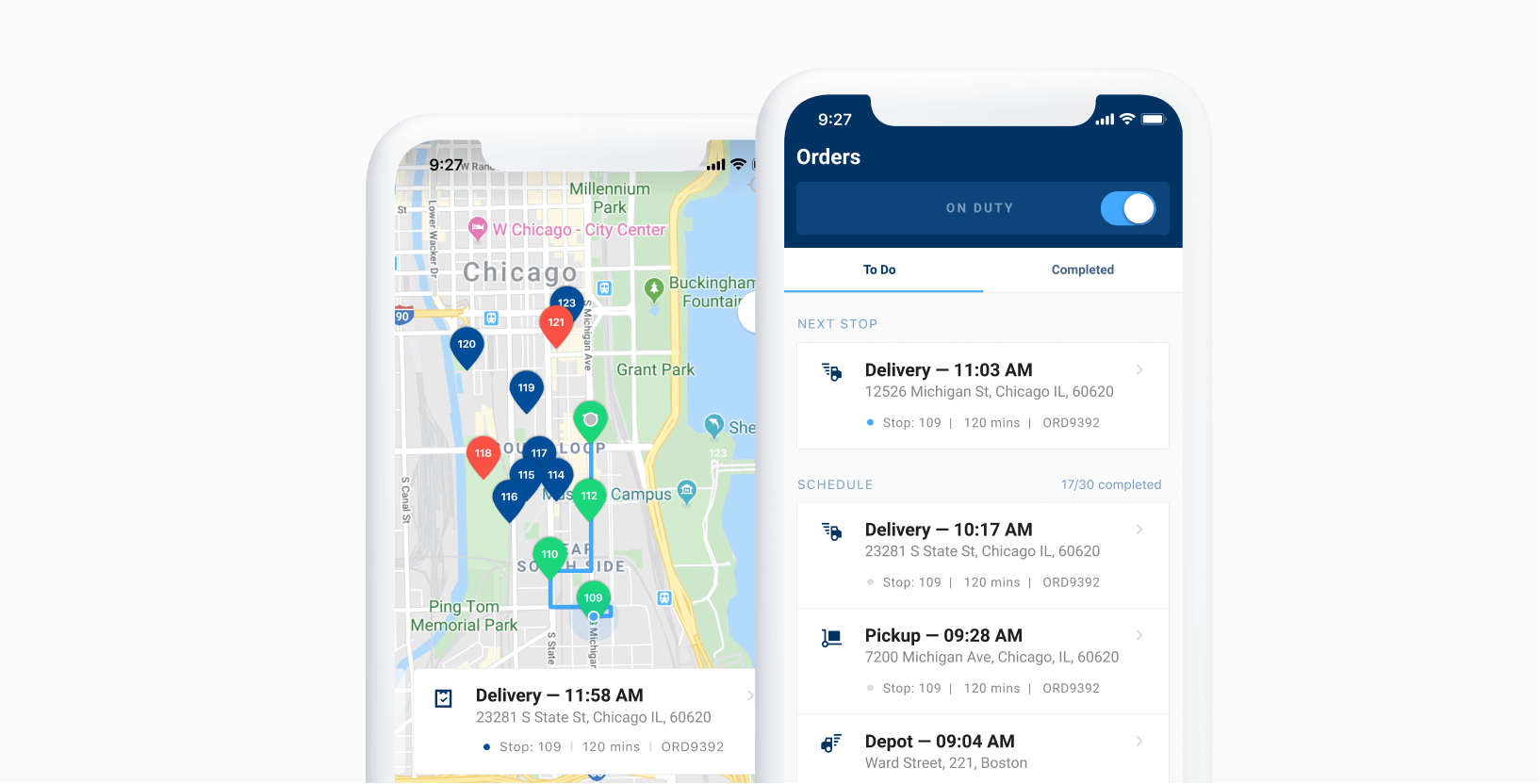
Conclusion
If you’re looking to reduce your transportation costs, OptimoRoute is your new best friend.
Not only can you optimize routes for your drivers, but the Mobile App also reduces human error, and helps avoid failed deliveries with Realtime Order Tracking.
By importing orders in bulk planning routes automatically, you also eliminate a lot of time-consuming manual labor and significantly speed up the process and all packages.
Start your 30-day free trial today to see how OptimoRoute can reduce your transport costs.
Try OptimoRoute™ for Free
No installation or credit card required